screen printing ink plastisol
Screen Printing Ink Solutions
Want to know more solutions ? click the button below
Screen Printing Ink Plastisol Problems and Solutions
With over 30 years of experience, we have a deep knowledge of screen printing and plastisol. We can provide you with professional services and innovative solutions to meet all your screen printing needs.
In addition, we focus on developing and delivering innovative products that are unique to the market. These products not only help you make more money, but also create a safer working environment for you and your team, and protect the earth’s ecosystem.
Many customers choose to print their products with our screen printing inks because of the many advantages of this service. Screen printing plastisol ink are known for their versatility, durability, vivid colors, high cost-effectiveness and fast turnaround
Webbing
Footwear
Gloves
Apparel
Socks
Outdoor Gear
Screen printing ink solutions you should know
We will help customers find and fix screen printing errors. So, what are the common problems that may occur during screen printing? As a screen printing ink manufacturer with more than 30 years of experience, we will tell you how to solve these problems: ink curing problems, color migration, ink thickness changes, poor ink fluidity, poor adhesion to the substrate, blurred or distorted images, inconsistent colors, underexposure or overexposure, registration problems (when printing in multiple colors), screen printing ink plastisol opacity problems, etc.
-
1. Ink curing problem
Problem: Under-curing can cause the print to fade or crack, while over-curing can cause a brittle or discolored surface. Solution: Ensure screen printing ink plastisol reaches 320°F (160°C) to fully cure, using a temperature gun or heat probe to check heat distribution across the print. Over-curing: If discoloration or cracking is observed, control dryer temperature and reduce dwell time.
-
2.Dye Migration
Problem: Dyes in sports fabrics bleed into the ink, especially when screen printing ink colors like white ink or light-colored ink. Solution: Use migration-blocking additives or low-bleed inks—CHJT-8502 flash-cured at lower temperatures to minimize heat-induced migration, especially for synthetic fibers.
-
3.Ink thickness changes
Problem Description: The printed screen printing ink plastisol layer may have inconsistent thickness over the printed area. Some areas may be too thick while others may be too thin. Cause: Uneven squeegee pressure. If squeegee pressure is uneven during printing, it will cause the screen printing plastisol ink to pass through the screen at different rates in different areas, resulting in thickness variations. Improper screen tension. Inadequate or uneven screen tension will cause different parts of the screen to deform differently when printing, affecting ink transfer and causing thickness differences. Solution: Regularly check and adjust squeegee pressure to ensure uniform squeegee width. Use a pressure-sensitive gauge if necessary. Re-tension the screen appropriately following the manufacturer's guidelines for the specific screen material and size. Use a tension gauge to measure and obtain uniform tension.
-
4. Ink fluidity is poor
Problem: The ink is too thick or has poor flow and is difficult to spread evenly on the substrate. Solution: Use curable thinner to adjust the ink viscosity. Maintain a warm working environment as lower temperatures will cause the ink to thicken.
-
5. Poor adhesion to the substrate
Problem description: Plastisol inks may not adhere well to the substrate, causing the printed image to peel or delaminate. Cause: Inadequate substrate preparation. The substrate surface may be contaminated with oil, dirt, or release agents, which prevents the ink from adhering properly. Incorrect ink-substrate combination. Not all plastisol inks are suitable for all substrates. For example, using an ink formulated for cotton on a polyester substrate may result in poor adhesion. Solution: Use special inks before printing. Use different inks for different fabrics, for example, Strong Base Ink - CHJT-5115. Choose the appropriate heat-set ink for the specific substrate. Consult the ink manufacturer's compatibility chart or perform an adhesion test.
-
6. Blurred or distorted images
Problem Description: Printed images may appear blurry, with unclear edges or distorted. Cause: Low-quality screens, screens with too large mesh or screens with inconsistent mesh sizes can cause uneven ink spread, resulting in a blurry image. Incorrect scraper angle or speed. Incorrect scraper angles (too steep or too flat) or scraper speeds that are too high can disrupt ink transfer and cause image distortion. Solution: Use a higher-quality screen with the appropriate mesh count to achieve the desired print resolution. Adjust scraper angle and speed. A general guideline is to start with a scraper angle of about 45 - 60 degrees and then adjust the speed based on ink viscosity and substrate type.
-
7. Inconsistent Colors
Problem description: The color of plasto ink may vary from fabric to fabric or from area to area of the same print. Cause: Inconsistent ink mixing. Color variations may occur if plasto ink is not mixed thoroughly or accurately each time. Different degrees of curing can affect color. As mentioned earlier, incomplete or excessive curing can change the color of plasto ink. Solution: Use a mechanical agitator to ensure that the ink is mixed thoroughly and consistently. (Use uniform force and speed) Standardize the curing process to minimize the impact of curing on color. Use color control equipment such as a spectrophotometer to monitor and adjust color during the printing process.
-
8. Target underexposure or overexposure
Cause: Problems during screen making, such as underexposure or overexposure, can cause the image on the screen to not fully cure or be damaged, resulting in missing images when printing. Solution: Re-evaluate exposure parameters. Generally, for common polyester screens and medium mesh screens, when using standard photosensitive adhesives, the exposure time may be between 2-5 minutes (depending on the light intensity of the exposure equipment), the light intensity should be kept within a suitable range, such as 80-120mW/cm², and the exposure distance can be controlled at 50-100cm. Solution for overexposure: Adjust the parameters of the exposure equipment. Reduce the exposure time or reduce the light intensity. If the current exposure time is 6 minutes and overexposure occurs, you can reduce the exposure time by 30 seconds each time for testing until the appropriate curing effect is obtained.
-
9. Registration problem (when printing in multiple colors)
Poor registration accuracy Reason: Insufficient accuracy of printing equipment. Wear of the transmission parts of the equipment and inaccurate guide devices will affect the registration accuracy between different colors. Movement of the screen during printing. Due to unstable tension or loose fixation of the screen, slight movement may occur during multiple printings, resulting in registration errors. Movement of the substrate during printing. If the substrate is not firmly fixed on the printing table, it will also be displaced during the printing process, affecting the registration effect. For wear of equipment transmission parts/for inaccurate guide devices Solution: Regularly check the transmission parts of the equipment, such as gears, chains, belts, etc. For severely worn parts, replace them in time. For unstable screen tension/for loose fixation of the screen Solution: When stretching the screen, use a tension tester to accurately measure and control the screen tension. Different screen materials and printing requirements have different tension ranges. During the printing process, check the screen tension regularly. If the tension changes, adjust it in time. Check the screen fixing devices, such as clamps, screws, etc. Make sure that the clamps can firmly clamp the screen and the screws are not loose. Tighten the loose screws in time, and replace the clamps with new ones if they are damaged. Consider using a more reliable screen fixing method, such as a magnetic fixing device (suitable for printing equipment parts that can be magnetically adsorbed) or a high-precision pneumatic clamping device to enhance the firmness of the screen fixing.
-
10. Ink opacity problem
Problem: Poor coverage or thin ink laydown and low opacity on dark fabrics. Solution: Use base color when printing on dark fabrics - CHJF-1700 Choose a lower grid count (110-160) for better ink laydown and coverage. Ensure ink viscosity is correct - if the ink is too thick, modify with a thinner.
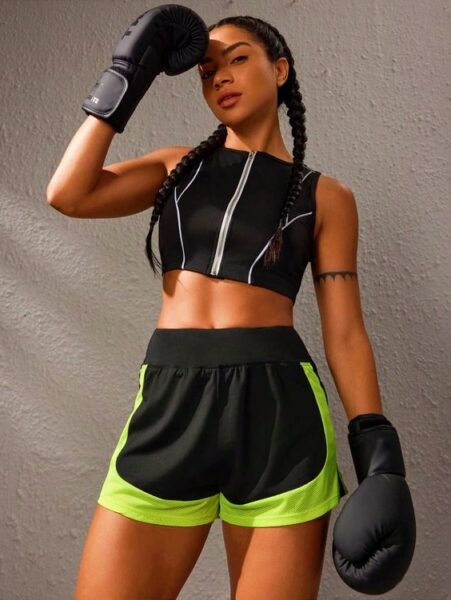
Screen Printing Ink Plastisol Sportswear
Our screen printing plastisol ink are designed to meet the rigorous demands of high-performance sportswear. Whether you’re printing on jerseys, leggings, or compression gear, ECOPrintInk ensures that your designs remain flexible, breathable, and durable, even under the most intense physical activity. Additionally, our inks are environmentally friendly, allowing you to lead in both performance and sustainability, making your sportswear brand a favorite among athletes and environmental advocates alike.
EcoPrintInk delivers premium screen printing ink plastisol specifically designed for the apparel industry, offering outstanding print clarity, vibrant colors, and long-lasting durability. Whether you’re printing on custom t shirts ink, hoodies, or outerwear, our inks ensure your garments stand out with striking designs that are resilient against wear. Our environmentally friendly approach means that each print not only looks great but also contributes to a sustainable future, making your apparel brand a leader in eco-conscious fashion.
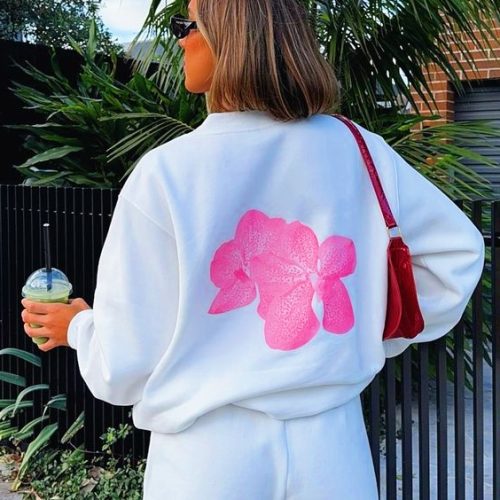
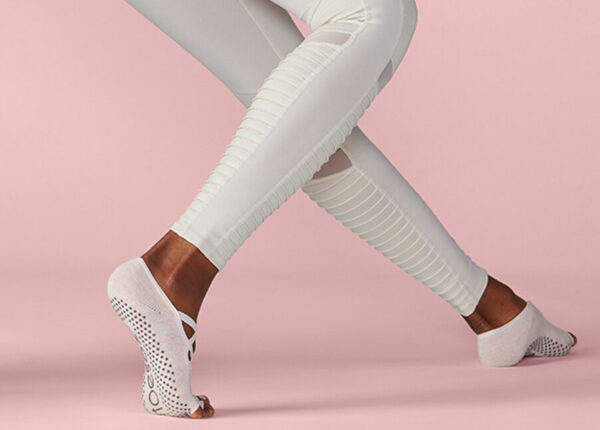
Screen Printing Ink Plastisol Socks
When it comes to sock printing, EcoPrintInk’s screen printing ink plastisol provide the perfect blend of comfort, elasticity, and visual appeal. Our screen printing ink plastisol are designed to withstand the rigors of daily wear and frequent washing, ensuring that your sock designs remain vibrant and intact over time. By choosing our sustainable inks, you can create socks that not only offer superior comfort and style but also reflect your commitment to environmental responsibility, making them a standout choice in the market.
Screen Printing Ink Plastisol Webbing
EcoPrintInk’s eco-friendly screen printing ink plastisol are engineered for webbing applications that demand durability, vibrant color, and strong adhesion. Whether used in industrial, commercial, or consumer products, our inks provide superior performance, ensuring your webbing products endure rigorous use and environmental challenges. With a focus on sustainability, our inks help you create products that not only perform exceptionally but also contribute to a greener planet.
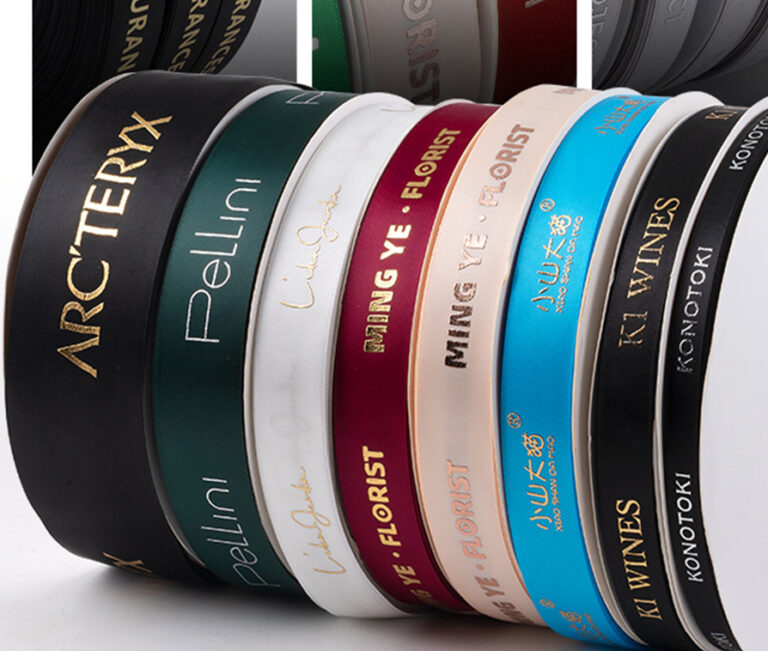
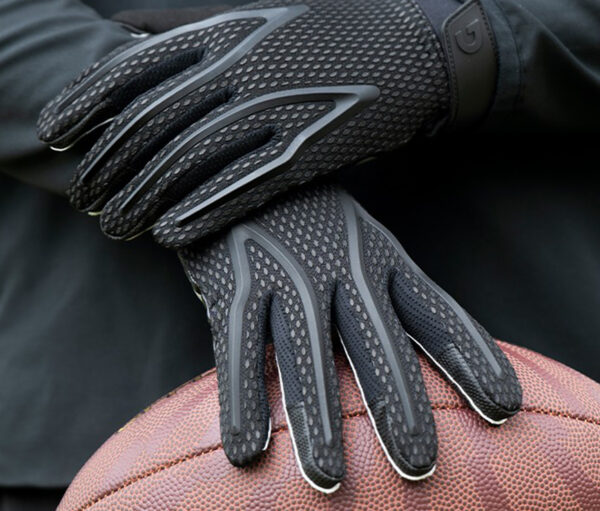
Screen Printing Ink Plastisol Gloves
For glove printing, EcoPrintInk’s screen printing ink plastisol offer unmatched stretchability, durability, and resistance to wear and tear. Perfect for work gloves, sports gloves, or fashion accessories, our ink plastisol ensure that your designs maintain their integrity through heavy use and frequent washing. Our commitment to sustainability means that our inks not only enhance the appearance and functionality of your gloves but also align with eco-conscious production standards, promoting a healthier planet.
Screen Printing Ink Plastisol Footwear
Our screen printing ink plastisol are tailored to meet the unique demands of the footwear industry. EcoPrintInk offers flexible, durable, and rich colors that adhere perfectly to a variety of materials, including synthetic and natural leathers. Whether you’re designing athletic shoes, casual footwear, or high-fashion pieces, our inks provide long-lasting vibrancy and resilience. By choosing ECOPrintInk, you support sustainable practices in footwear manufacturing, ensuring your designs are both stylish and environmentally responsible.
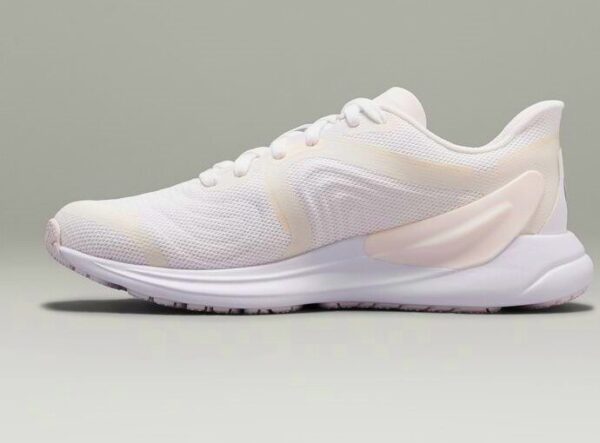
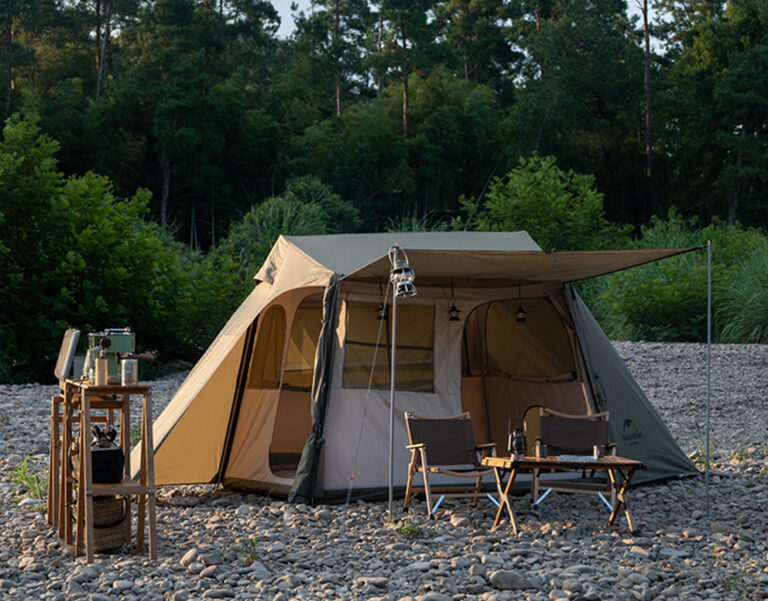
Screen Printing Ink Plastisol Outdoor Gear
Outdoor gear requires inks that can withstand harsh weather conditions and extensive use, and EcoPrintInk’s screen printing ink plastisol are up to the task. Ideal for printing on backpacks, tents, jackets, and other outdoor products, our ink plastisol offer exceptional durability and colorfastness. Our solutions are designed to help outdoor brands create products that not only perform under extreme conditions but also contribute to a sustainable and eco-friendly outdoor lifestyle, ensuring your brand resonates with environmentally conscious consumers.
Compression Gear
Leggings
Belts
Totes
Awnings
Backpacks
Socks
Upholstery
Tarpaulins
Backpacks
Gloves
Jerseys
Webbing
...
More options
to Screen Printing Ink Plastisol
Solutions
At EcoPrintInk, we understand that different industries have unique needs, which is why we offer a range of specialized screen printing ink plastisols solutions to meet those needs. In addition to our core applications, our screen printing inks plastisols are perfect for a variety of other products, ensuring that your designs are both durable and environmentally friendly. We also offer solutions for bags and accessories, home textile solutions, industrial fabric ink solutions and more.
Get More Information About Screen Printing Plastisol Ink?
We will send you industry information from time to time.