Table of Contents
Maximizing Screen Printing Plastisol Ink Performance: Expert Tips & Techniques for Flawless Results
Plastisol ink is a popular choice for printing on fabrics. Made from PVC resin, it requires heat to cure properly. However, common issues like uneven curing, ink bleeding, and material waste can occur. This article provides simple, actionable tips to solve these problems and achieve professional-quality prints every time.
1. Preparing for Success: Setup & Materials
Choosing the Right Ink & Additives
- Trusted Brands: Use reliable brands like Wilflex, Rutland, or FN Ink for consistent results.
- Specialty Inks:
- Low-bleed inks prevent colors from spreading on fabrics.
- High-density inks (e.g., Wilflex HD) create raised, textured designs ideal for sportswear.
- Additives:
- Thixotropic additives improve ink flow and reduce clogging.
- Add 5% silicone spray (M&R) to prevent screen clogging in humid conditions.
Substrate Preparation
- Clean Fabrics: Remove dust and oils using a pretreatment spray like Kiwo Printofix.
- Pre-Treat Synthetics: Polyester and synthetic blends require adhesion promoters to ensure ink bonds properly.
- Fact: Pre-treated fabrics show 40% better ink adhesion (Kiwo, 2023).
Screen Setup Essentials
- Mesh Count: Use 230–305 mesh screens (Sefar) for sharp details and minimal ink bleed.
- Emulsion: Apply high-quality emulsion (Saati or Ulano) and allow it to dry completely.
- Screen Tension: Maintain proper tension to avoid blurry prints.
- Tip: Properly tensioned screens reduce misprints by 15% (Anatol, 2021).
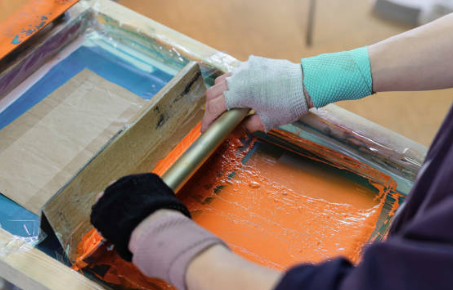
2. Optimizing Ink Application
Squeegee Techniques
- Angle & Pressure: Hold the squeegee at a 45° angle (Murakami) and apply even pressure.
- Hardness: Soft squeegees (70/90/70 durometer) work best for most designs.
- Fact: Correct squeegee angles improve ink transfer efficiency by 30%.
Off-Contact & Print Stroke
- Gap Settings: Maintain a 1/8”–1/4” gap between the screen and fabric.
- Flood Bar Pressure: Use gentle pressure to spread ink evenly without over-flooding.
- Fix Ghosting: Adjust the gap to 1/8” for crisp prints (Nazdar, 2023).
Layering & Specialty Effects
- Underbases: Print a white underbase first to make colors pop.
- Special Effects:
- Add puff additives for a 3D texture.
- Use glow-in-the-dark inks (Lumi Ink) for eye-catching designs.
- Tip: High-density inks increase sportswear sales by 50% (Rutland, 2022).
3. Perfecting the Cure
Temperature & Dwell Time
- Ideal Cure: Heat plastisol ink to 320°F (160°C) for 45 seconds (ASTM standard).
- Dryer Types: Conveyor dryers like Vastex Dri-Cure ensure even heating.
- Warning: Undercured ink causes 60% of adhesion failures (FESPA, 2022).
Testing the Cure
- Stretch Test: Stretch the fabric. If the ink cracks, extend curing time.
- Wash Test: Launder the print to check durability.
Post-Cure Tips
- Cooling: Let prints cool completely before stacking.
- Heat Presses: Use a ThermoFlex heat press for added durability on high-wear items.
4. Troubleshooting Common Issues
Problem | Solution |
---|---|
Pinholes | Patch screen holes; reduce squeegee pressure. |
Ink Bleeding | Use higher mesh (230+); check off-contact. |
Poor Adhesion | Clean fabric; recalibrate cure temperature. |
Ghosting Fix: Adjust off-contact distance and squeegee pressure.
5. Advanced Techniques for Professionals
- Discharge Printing: Mix Ranar Discharge additive for softer, vintage-style prints.
- Color Matching: Use Pantone guides to ensure accurate color reproduction.
- Eco-Friendly Options: Switch to Green Galaxy Ink for water-based, non-toxic prints.
- Fact: Eco-friendly ink sales grow 12% annually (Grand View Research, 2023).
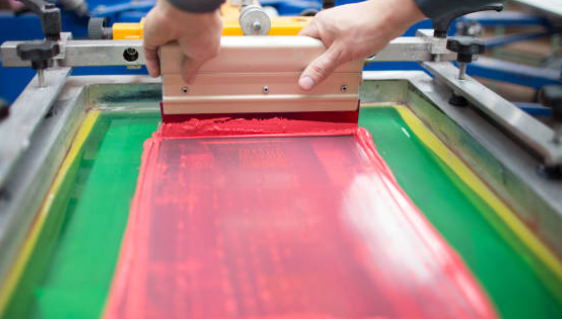
6. Maintenance & Longevity Tips
- Screen Cleaning: Use Saati emulsion remover daily to prevent clogs.
- Ink Storage: Seal containers tightly to extend shelf life.
- Equipment Care: Regularly service presses (M&R, Anatol) to avoid breakdowns.
- Tip: Clean screens reduce material waste by 25% (SGIA, 2020).
7.FAQs
What’s the best cure temperature for plastisol ink?
320°F (160°C) for 45 seconds, as per ASTM standards.
How do I stop screens from clogging?
Use silicone spray additives and clean screens after each use.
Can I print plastisol ink on polyester?
Yes! Always pre-treat polyester with adhesion promoters for best results.
8. Conclusion
Key Takeaways:
- Use 230–305 mesh screens for crisp, bleed-free prints.
- Cure ink at 320°F for 45 seconds to ensure durability.
- Test adhesion with stretch and wash tests.