Table of Contents
How to Get Bright, Long-Lasting Prints with Plastisol Ink
Plastisol ink is a popular choice in screen printing for its durability and vibrant colors, especially when using plastisol inks for screen printing. is a thick, colorful ink used to print designs on T-shirts and other fabrics. Unlike other inks, it doesn’t dry until you heat it. This makes it easy to print, but you need to follow specific steps to ensure your prints stay bright and don’t crack or peel. Let’s break down everything you need to know!
What You Need to Start
1. Choose the Best Plastisol Inks Not all inks are the same. Wilflex is great for bright colors, while Union Ink works well for mixing custom shades. If you’re printing on stretchy fabrics like spandex, try FN Ink, which stays flexible. Special inks like Metallic plastisol is a type of screen printing ink that adds a shiny finish to garments. add shine, and high-opacity white is a must for dark shirts to make colors pop.
2. Consider using white ink for better visibility on dark fabrics. Gather Your Tools You’ll need various ink types to achieve the desired effect. screens (also called “mesh screens”) to hold the ink. Use 110-160 mesh screens for simple designs or dark fabrics—they let more ink through for bold colors. For small details, switch to 230+ mesh screens are ideal for printing fine details with screen printing ink.. A squeegee (a rubber tool) pushes ink through the screen. Soft rubber squeegees (60 duro) work best for thick inks, while hard rubber (75 duro) is better for fine lines.
Don’t forget a flash cure unit to dry ink between layers and a conveyor dryer (like ones from M&R or Vastex) to fully cure the ink. If you’re working in a small space, a heat press Conveyor dryers give more even results with plastisol inks for screen printing.

Preparing Your Screen
1. Pick the Right Screen Mesh The screen’s mesh count decides how much ink gets through, particularly with pigment inks. For dark shirts, start with a white ink for the best contrast. 110 mesh screen to lay down a thick white underbase. On light fabrics, use 160 mesh for softer prints. Need tiny details? 230+ mesh screens Keep lines sharp when using screen printing plastisol ink.
2. Coat the Screen Properly Use emulsion (like Saati or Ulano brands) to block parts of the screen you don’t want ink to pass through. Coat the screen 1-2 times to cover all holes. Let it dry in a dark room before exposing it to light.
Printing Tips for Vibrant Colors
1. Start with a White Underbase Dark fabrics can make colors look dull. Fix this by printing a layer of white plastisol ink first. Flash-cure it for 10 seconds (just enough to dry the surface), then add colors on top. This makes reds, yellows, and blues stand out.
2. Mix Colors While Wet Printing colors one after another before they dry (called “wet-on-wet”) helps blends look smooth, especially with opaque inks. Use a A hard squeegee is recommended for achieving a smooth application of plastisol screen printing ink. to push inks together without muddying the colors.
3. Master the Squeegee Hold the squeegee at a low cure angle for better control. 45-degree angle and press firmly. Move quickly for thin layers of screen printing ink or slowly for thicker ink to achieve the desired opacity. Adjust pressure based on the design—heavy pressure for bold graphics, light pressure for details.
Curing Plastisol Ink Correctly
Curing is the most important step. If the ink isn’t heated enough, it will peel. Too much heat can burn the fabric. Here’s how to do it right: use a water base ink for a softer hand on your garment.
- Set the Temperature: Heat your dryer to 320°F (160°C) is the recommended temperature for curing plastisol screen printing ink..
- Time It: Let the ink cure for 60-90 seconds. Studies show this makes prints survive over 50 washes.
- Check the Temperature for the ink type used in the process.Use a hard squeegee for screen printing to achieve a more opaque finish. donut probe (a small thermometer) to ensure the ink itself reaches 320°F—not just the air around it.
Pro TipConveyor dryers (like those used in screen printing) ensure that the ink cures properly. M&R models) work best, but if you’re using a heat press, press the design for 15-20 seconds and check for even heating.
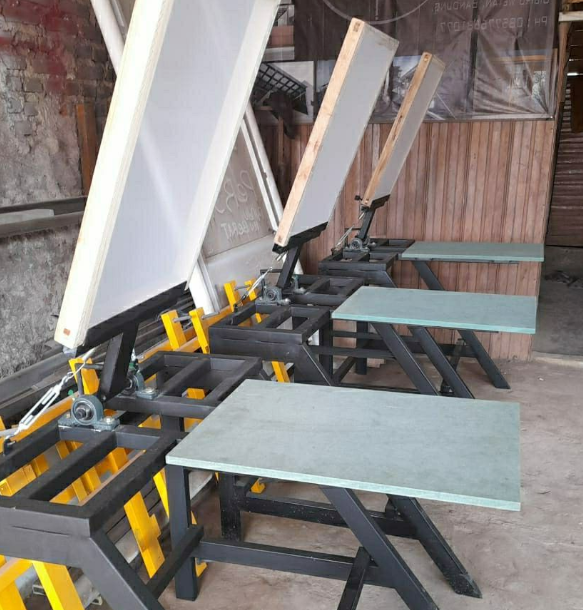
Making Prints Last Longer
1. Add Special Mixes to the Ink
- Low-bleed base is essential when using water base inks to prevent color bleeding on garments.: Stops dyes from polyester fabrics (like performance tees) from bleeding into the ink. Mix 10-15% into your plastisol.
- Stretch additive: Add 5% of products like Wilflex StayFlex to keep prints flexible on activewear.
- UV protectant: Prevents colors from fading in sunlight.
2. Handle Prints After Curing Wait 24 hours Before washing newly printed shirts, ensure the ink type is suitable for longevity. Stacking hot shirts can cause sticking—let them cool first!
Fixing Common Problems
- Cracking: Caused by undercuring. Re-cure at 320°F for 60 seconds.
- Fading Colors: Use UV-resistant additives and avoid leaving shirts in direct sunlight.
- Peeling Ink: Clean fabrics before printing. For polyester, pretreat with a spray to help ink stick.
Plastisol vs. Water-Based Ink
Plastisol is better for bold, bright designs and works on most fabrics. Water-based ink is known for its environmental benefits and soft hand feel on garments. feels softer but needs more skill to use. Plastisol costs less ($0.08 per print vs. $0.12 for water-based) and is easier for beginners.
FAQs
Can plastisol air-dry?
No! Use the right ink color for your project. You must heat it to 320°F.
Is plastisol safe?
It contains PVC. For eco-friendly options, try Green Galaxy inks.
It contains PVC. For eco-friendly options, try Green Galaxy inks.
Use a white underbase on dark shirt
Final Tips
- Test settings on one garment before printing a batch to ensure the best results.
- Use a timer to avoid undercuring.
- Clean screens immediately after use to prevent dried ink from clogging them.