Conclusion
Using white plastisol ink effectively requires a good understanding of its properties and the challenges that can arise during the printing process. By adhering to best practices, selecting high-quality inks, and being mindful of curing conditions, you can achieve stunning results in your screen printing projects. Remember, the key to vibrant, lasting prints lies in your approach to using white plastisol screen printing ink. Embrace these strategies, and watch your custom apparel shine!
Why Does My White Plastisol Ink Look Yellow?
When working with white plastisol ink, many printers encounter a common issue: the ink can sometimes appear yellowish instead of the vibrant white they expect. Understanding the reasons behind this phenomenon and how to achieve the best results is crucial for anyone in the screen printing industry. This comprehensive guide will delve into the factors affecting the appearance of white plastisol ink, the best practices for using it, and tips for selecting the ideal ink for your projects.
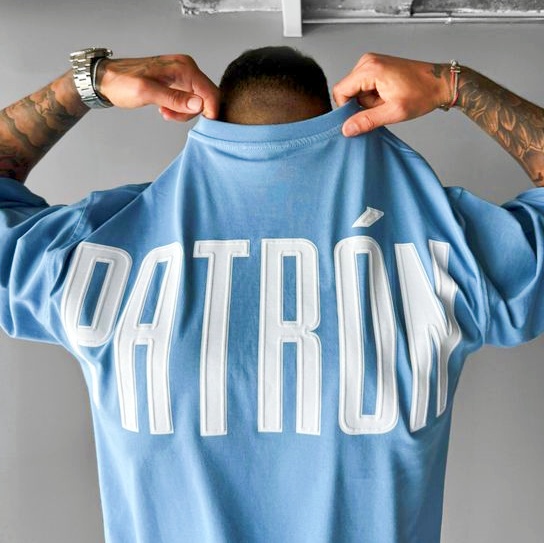
The Science Behind Plastisol Ink
Plastisol ink is a popular choice in screen printing due to its versatility and ease of use. Composed primarily of PVC particles suspended in a plasticizer, it remains stable until heated, at which point it fuses with the fabric. However, several variables can influence the final appearance of white plastisol screen printing ink, leading to issues like yellowing.
Factors Contributing to Yellowing
- Heat Exposure
When white plastisol ink is subjected to excessive heat during the curing process, it can undergo a chemical reaction that alters its color. Ensure that your curing temperature is appropriate for the ink and substrate. - Quality of Ink
Not all white plastisol inks are created equal. Low-quality inks may have a tendency to yellow more quickly than their higher-quality counterparts. Investing in the best white plastisol ink will often yield better results. - Environmental Conditions
Humidity and temperature fluctuations can impact the ink’s appearance. Store your inks in a cool, dry place to maintain their integrity. - Ink Thickness
A white plastisol ink too thick may not cure properly, leading to a yellowish tint. Ensure your ink consistency is appropriate for your application. - Substrate Interaction
Some fabrics can react with the ink, causing discoloration. For instance, using low bleed white plastisol ink can help mitigate the risk of dye migration from the fabric to the ink.
Best Practices for Using White Plastisol Ink

To achieve vibrant, true-to-color results with white plastisol ink, consider the following best practices:
1. Use an Underbase
When printing colors on dark garments, it’s essential to use a white underbase. This serves as a primer that enhances color vibrancy and opacity. For example, when printing a design in golden yellow on a navy blue shirt, the white underbase allows the yellow to pop. This method ensures a two-color print: white and yellow.
2. Print-Flash-Print Technique
For single-color designs printed on dark fabrics, employing a print-flash-print technique can significantly enhance the vibrancy of white plastisol screen printing ink. This method involves printing two passes of white ink, allowing for a brighter final result.
3. Choose the Right Ink
Selecting the best white plastisol ink for screen printing is crucial. Look for options like poly white plastisol ink designed specifically for synthetic fabrics, as these often offer better adhesion and opacity.
4. Monitor Curing Conditions
Pay close attention to the curing process. Overheating can lead to undesirable color changes. Follow the manufacturer’s recommendations for curing times and temperatures.
Common Challenges with White Plastisol Ink
Despite best efforts, printers may still face challenges with white plastisol ink. Here are some common issues and solutions:
Dye Migration
Dye migration occurs when the dyes from synthetic fabrics, especially polyester, seep into the ink during curing, causing discoloration. To combat this, using low bleed white plastisol ink can minimize migration risks. Additionally, lowering curing temperatures can help.
Inconsistent Coverage
When printing over seams, zippers, or pockets, achieving even coverage can be challenging. The fabric’s varying thickness can lead to inconsistencies in the print. Always strive for a flat surface when screen printing to avoid these issues.
Thick Ink Problems
If you find that your white plastisol ink too thick, it may not spread evenly during printing. Thinner ink can often produce a smoother finish and better coverage. Consider adding a compatible thinner to adjust the ink’s viscosity.