Top 5 Plastisol Ink Additives for Screen Printing Applications
Introduction
Plastisol inks are a staple in the screen printing industry, known for their versatility and durability. However, to achieve specific effects, improve performance, or adapt to different substrates, plastisol ink additives are often necessary. These additives can modify the ink’s properties, allowing printers to customize their prints according to the project’s needs. In this article, we’ll explore the top six plastisol ink additives used in screen printing applications, detailing how each one can enhance your printing process.
Plastisol Ink Additives for Application in Screen Printing
Plastisol ink additives are specially formulated chemicals added to plastisol inks to change their behavior and characteristics. Whether you need to adjust the ink’s viscosity, improve its adhesion to different substrates, or create special effects, there is likely an additive designed for that purpose. Understanding these additives and how to use them can significantly expand your printing capabilities and improve the quality of your prints.
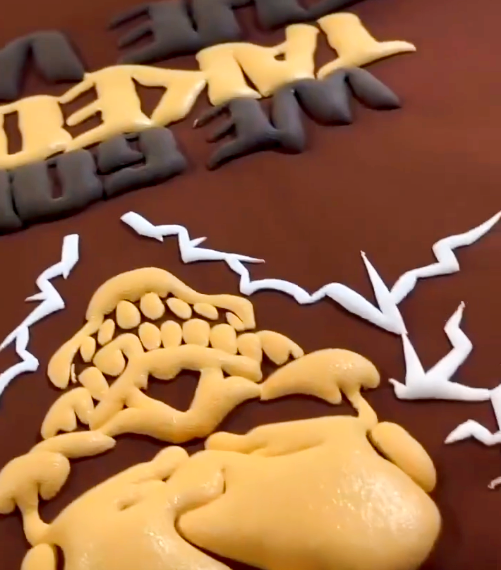
Soft-hand Extenders
What Are They?
Soft-hand extenders are plastisol ink additives designed to create a softer feel, or “hand,” on the finished print. These additives reduce the ink’s opacity and thickness, resulting in a more lightweight and flexible print that is less noticeable to the touch.
When to Use?
Soft-hand extenders are ideal for designs that require a more natural feel, such as on garments where comfort is a priority. They are particularly useful when printing large, solid areas where a heavy ink deposit would result in a stiff, uncomfortable print.
Application Tips:
- Start with a small amount and gradually increase until the desired softness is achieved.
- Be mindful that using too much extender can reduce the ink’s opacity, potentially requiring additional layers or a base coat to maintain vibrancy.
Foil-Release Additives
What Are They?
Foil-release additives are used to make plastisol ink suitable for foil printing applications. These additives improve the adhesion of the foil to the ink while allowing for easy removal of excess foil, leaving behind a clean, metallic finish.
When to Use?
Use foil-release additives when you want to add shiny, metallic elements to your prints. This technique is popular for creating eye-catching designs on fashion apparel, promotional items, and accessories.
Application Tips:
- Ensure the base plastisol ink is compatible with foil applications.
- Apply the foil-release additive according to the manufacturer’s instructions, as overuse can affect the foil’s adhesion and durability.
Viscosity Reducers
What Are They?
Viscosity reducers are plastisol ink additives that thin the ink, making it easier to print through finer mesh screens. This adjustment can also enhance the ink’s flow properties, reducing the effort needed to push the ink through the screen and improving the overall print quality.
When to Use?
Viscosity reducers are beneficial when working with high-detail designs that require fine lines and intricate patterns. They are also useful in situations where the ink has thickened over time, restoring it to its optimal consistency.
Application Tips:
- Add viscosity reducers gradually to avoid over-thinning the ink.
- Mix thoroughly to ensure an even consistency throughout the ink.
Flash Additives
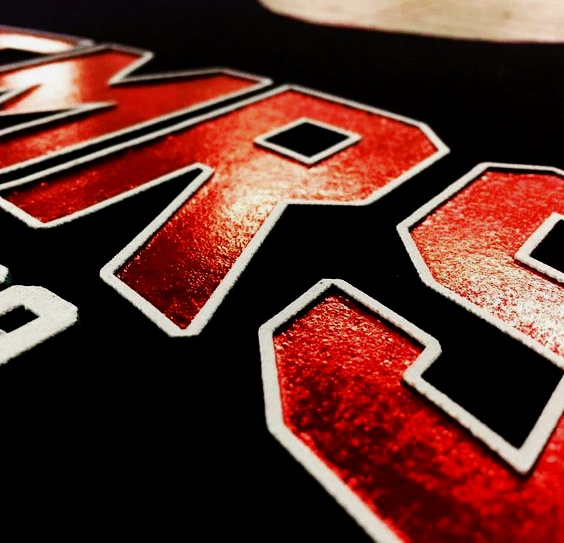
What Are They?
Flash additives, also known as flash-cure additives, are designed to reduce the curing time of plastisol inks during the flash-drying process. These additives enable the ink to dry more quickly, allowing for faster production times without compromising print quality.
When to Use?
Flash additives are particularly useful in high-volume production environments where speed is essential. They are also beneficial when printing multi-color designs that require intermediate drying between colors to prevent smudging or bleeding.
Application Tips:
- Follow the manufacturer’s recommended dosage to avoid over-drying, which can affect the ink’s adhesion and durability.
- Test the ink after adding flash additives to ensure it still meets your curing requirements.
High-Elongation Additives
What Are They?
High-elongation additives are plastisol ink additives that enhance the ink’s flexibility and stretchability. These additives are essential when printing on stretchy fabrics such as spandex, nylon, or other athletic materials where the print must move with the fabric without cracking or peeling.
When to Use?
Use high-elongation additives when printing on garments that require significant stretch, such as activewear, swimwear, or performance fabrics. These additives help ensure the print maintains its integrity even under stress.
Application Tips:
- Use the recommended amount of high-elongation additive to balance flexibility and print durability.
- Test the print’s stretchability before production to ensure the desired performance on the final product.
Nylon-Catalyst Additives
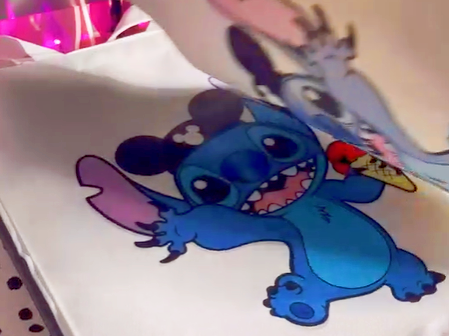
What Are They?
Nylon-catalyst additives are specifically designed to improve the adhesion of plastisol inks to nylon and other synthetic fabrics that are challenging to print on. These additives work by chemically bonding the ink to the fabric, ensuring a durable, long-lasting print.
When to Use?
Use nylon-catalyst additives when printing on nylon jackets, bags, or other synthetic materials that typically resist ink adhesion. These additives are crucial for producing prints that can withstand washing and wear without deteriorating.
Application Tips:
- Mix the nylon-catalyst additive into the plastisol ink just before printing, as it can shorten the ink’s shelf life.
- Ensure proper curing to activate the chemical bond between the ink and the fabric.
Conclusion
Plastisol ink additives are invaluable tools for screen printers, offering a range of options to enhance ink performance and expand creative possibilities. From achieving a soft-hand feel to ensuring proper adhesion on challenging fabrics, these additives can make a significant difference in the quality and versatility of your prints. By understanding the purpose and application of each additive, you can take full advantage of their benefits and produce superior results in your screen printing projects.
Whether you’re looking to improve print durability, speed up production, or create unique finishes, the right plastisol ink additives can help you achieve your goals. Keep experimenting with these additives to discover new ways to enhance your printing capabilities and stay ahead in the competitive screen printing industry.