Learn all about screen cure methods, including curing screen prints, heat press tips, and the ideal temperatures for success.
What Temperature Do You Heat Press Screen Prints?
When using a heat press to cure screen prints, temperature is a critical factor. The right heat setting ensures that the ink bonds permanently to the fabric, resulting in a durable and vibrant design. Generally, the ideal temperature for heat-pressing screen prints is between 320°F and 330°F. This range provides enough heat to cure most plastisol inks effectively while avoiding damage to the fabric.
Consistency in temperature is key. Uneven heating can result in improperly cured prints that may crack, fade, or peel after washing. Using a reliable heat press with a built-in temperature gauge ensures precise heat distribution across the platen. Remember, the temperature can vary slightly depending on the type of ink and fabric, so always refer to the ink manufacturer’s guidelines for the best results. A thorough understanding of the screen cure process is crucial for optimal outcomes.
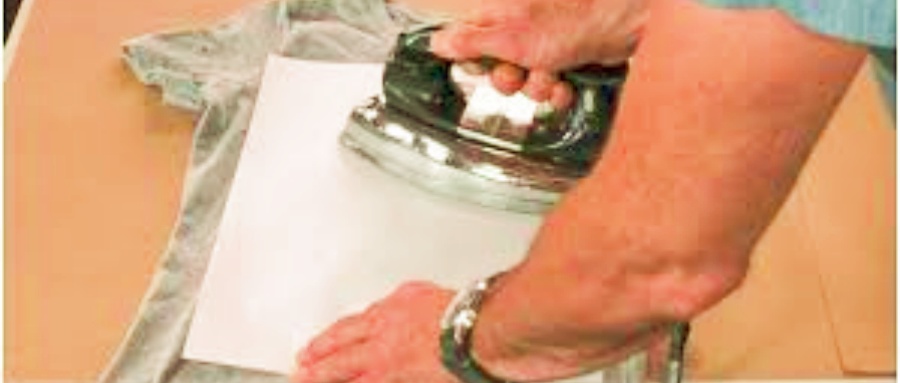
How Long Does It Take to Cure Screen Print?
Curing screen prints is a time-sensitive process. The curing duration largely depends on the type of ink you’re using and the equipment available. Plastisol ink, the most commonly used in screen printing, typically requires 10 to 60 seconds under a heat press or conveyor dryer to cure properly.
For a perfect cure, the ink’s internal temperature must reach 320°F, not just the surface of the print. To achieve this, many professionals use an infrared thermometer or heat gun to ensure the ink has reached the desired curing temperature.
Factors such as ink thickness, fabric type, and equipment efficiency can impact curing times. Thicker layers of ink or specialty fabrics may require additional time or adjustments to temperature. Regular testing ensures that the curing process is optimized for each project. Mastering screen cure techniques is a game-changer for ensuring print durability.
Can You Over Cure Screen Printing Ink?
Yes, over-curing screen printing ink is possible, and it can lead to undesirable results. Over-curing occurs when ink is exposed to excessive heat for too long, causing the print to become brittle and prone to cracking. In severe cases, over-curing can scorch the fabric, leaving permanent damage.
To avoid over-curing, it’s essential to follow these best practices:
- Monitor Time and Temperature: Use timers and thermometers to ensure that the curing process stays within the recommended parameters.
- Avoid Repeated Heating: Once the ink is fully cured, additional heating isn’t necessary and can degrade the print quality.
- Conduct Regular Tests: Perform wash tests to check the durability of cured prints, ensuring that they maintain their integrity over time.
A balanced approach to screen cure processes prevents over-curing and delivers high-quality results.
How to Cure with a Heat Press?
Curing screen prints with a heat press is a practical and efficient method, especially for small-scale production or DIY projects. Here’s a step-by-step guide to help you master the process:
- Set the Heat Press Temperature: Adjust the heat press to the recommended curing temperature for your ink, typically 320°F to 330°F.
- Position the Garment: Place the printed garment on the heat press platen. Ensure the design is flat and free from wrinkles.
- Cover the Print: Use a silicone sheet, parchment paper, or Teflon sheet to protect the print and fabric from direct heat.
- Apply Pressure and Heat: Close the heat press and apply medium pressure for about 10 to 60 seconds, depending on the ink type and thickness.
- Check for Proper Cure: Use a heat gun or infrared thermometer to confirm that the ink has reached its curing temperature throughout. Conduct a stretch test to ensure the print remains intact.
By following these steps, you can achieve professional-quality results with a heat press. The screen cure process with a heat press is not only efficient but also versatile for various projects.
Can You Use a Heat Press to Cure Screen Printing?
Absolutely! A heat press is a versatile tool that can effectively cure screen prints, provided the correct settings are used. While conveyor dryers are often the go-to equipment for large-scale screen printing operations, a heat press offers a viable alternative for small-scale or budget-conscious setups.
Advantages of using a heat press for curing include:
- Precision: Heat presses allow for precise control over temperature and pressure, ensuring consistent results.
- Cost-Effectiveness: Heat presses are more affordable than conveyor dryers, making them ideal for startups or hobbyists.
- Space-Saving: A heat press takes up less space, making it suitable for home-based or limited-space operations.
However, it’s essential to understand that heat presses may not be as fast or efficient for high-volume production. For consistent results, always use tools like thermometers and timers to monitor the curing process. Understanding the nuances of screen cure methods will improve overall print quality.
What Temperature Do You Cure Screen Printing?
The ideal curing temperature for screen printing depends on the type of ink being used. Plastisol ink, the most popular choice for screen printers, requires a curing temperature of 320°F. At this temperature, the ink undergoes a chemical process that ensures it adheres permanently to the fabric.
For water-based and discharge inks, curing temperatures can vary, typically ranging from 280°F to 320°F. These inks often require additional airflow or ventilation during curing to facilitate the evaporation of water content.
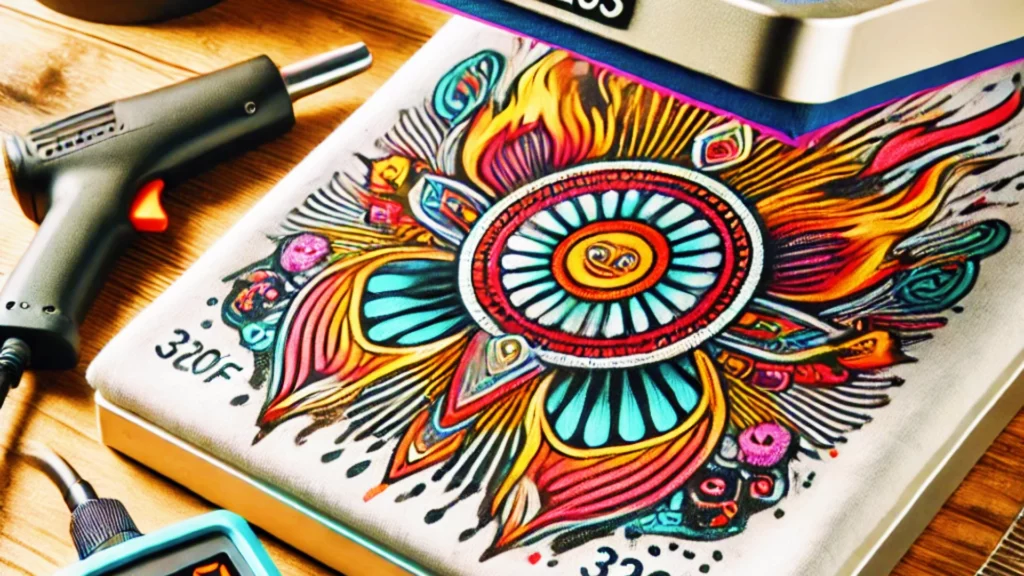
Here are some tips for maintaining the right curing temperature:
- Use Quality Equipment: Invest in a heat press or conveyor dryer with accurate temperature controls.
- Preheat the Equipment: Allow the heat press or dryer to reach the desired temperature before starting the curing process.
- Monitor Constantly: Use a heat gun or infrared thermometer to ensure consistent heat distribution across the print area.
By adhering to the recommended curing temperatures, you can achieve durable prints that stand up to wear and washing. The screen cure process ensures lasting results when followed correctly.
Conclusion
Mastering the screen cure process is essential for producing high-quality screen prints that last. Whether you’re using a heat press or a conveyor dryer, understanding the importance of temperature, time, and technique ensures consistent results. With careful attention to curing conditions and regular testing, you can achieve vibrant, durable designs that elevate your screen printing projects. Don’t forget to optimize your screen cure process based on the type of ink and fabric for the best outcomes.
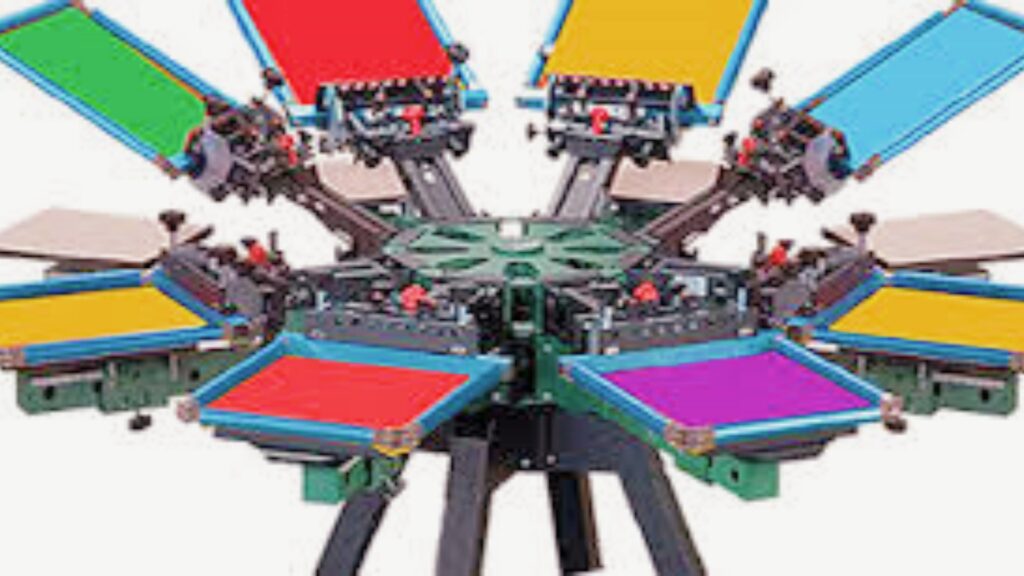