Printed Lycra Spandex——Silk Screen Printing Guide
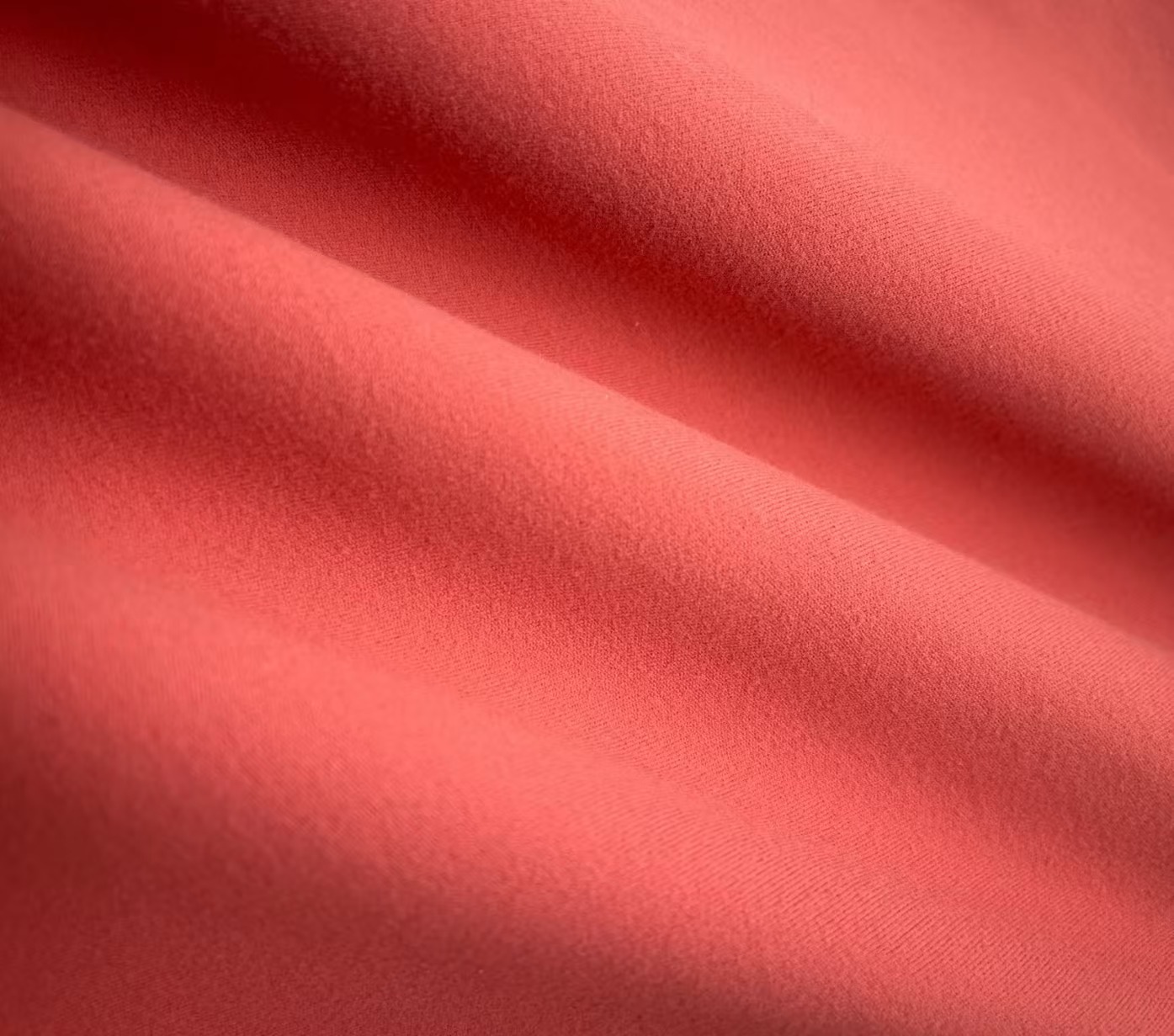
Introduction Lycra, known for its elasticity and smooth finish, is popular in sportswear, swimwear, and activewear. Its unique properties, however, can pose challenges for screen printers using Plastisol ink. This guide provides a comprehensive look at best practices for printing on Lycra with Plastisol ink, covering preparation, application techniques, common issues, and troubleshooting solutions.
Screen Printed Lycra Fabric: Lycra Ink Silk Screen Printing Guide
Due to the fiber characteristics and high elasticity of Lycra, when using Plastisol ink for screen printing, some special process and technical points need to be paid attention to to ensure the durability of the pattern and the elasticity of the fabric. The following are detailed steps and precautions on how to perform Plastisol screen printing on Lycra fabric:
Lycra Ink Screen Printing Operation Process
Step 1: Preparation
- Suitable plastisol ink: It is recommended to choose plastisol ink with low staining or anti-staining migration properties to prevent the dye penetration of Lycra from affecting the printing color.
- Conduct small batch tests: Before formal printing, conduct a small-scale test on Lycra samples to check the nozzle suction and tensile properties to ensure that the nozzle will not crack when the steel is stretched.
- Set the correct curing temperature: Lycra is heat-sensitive and should avoid excessive temperatures. It is recommended to keep the curing temperature around 280°F (138°C) to protect the elasticity of the fabric.
Step 2: Printing process
- Apply ink evenly: Apply the ink evenly with a scraper, and the ink concentration is too high to ensure the softness and elasticity of the print and the fabric.
- Multi-layer (optional):When adding color or layers, ensure that each layer is flash-dried thoroughly to maintain the hierarchy and stability between layers.
Step 3: Curing process
- Low temperature curing:Add Adjust the temperature to 280°F (138°C) in the drying tunnel to ensure that the ink is fully cured while protecting the elasticity of the fabric. The time is controlled within the appropriate range to prevent the Lycra fabric from shrinking or elastic deformation.
- Real-time temperature monitoring:Use a temperature gun to monitor the actual temperature to ensure consistent throughout the curing process.
Step 4: Quality Check and Post-Processing
- Check the quality of the print:After curing, check the print to ensure that there are no cracks, dye migration or model blurring.
- Extension test:Stretch the print on Lycra to test the rated force and elasticity of the ink to ensure that the print can stretch with the matching elasticity.
- Clean the screen and tools:After completion, clean the screen, scraper and other tools in time to prevent the emulsion residue from drying.
Common problems and solutions (brief)
- Dye migration:Use anti-migration emulsion, reduce flash-off time, and avoid dye-to-dye mixing.
- Pattern cracking:Use elastic additives and control ink thickness to increase pattern flexibility.
- Loss of elasticity:Ensure minimum curing to avoid excessive temperature damage to Lycra elasticity.
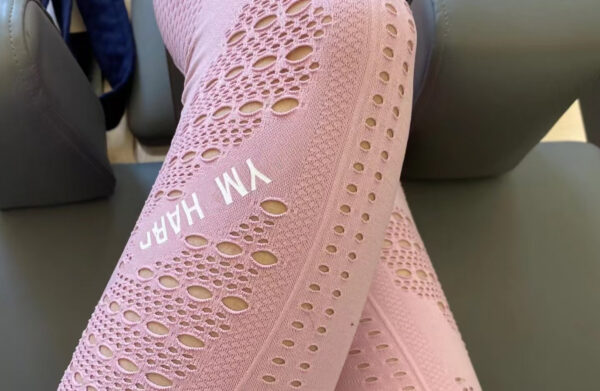
Common Issues in Silk Screen Printing on Lycra
Screen printing on Lycra, a stretchy and often slick fabric, presents unique challenges due to its elasticity and fabric properties. Here are some common issues faced when using silk screen printing on
Ink Cracking and Peeling:
- Issue: Lycra’s stretchiness can lead to ink cracking or peeling, especially if the ink isn’t designed for flexible fabrics.
Dye Migration:
- Issue: Dye migration occurs when the fabric’s dyes bleed through the ink, resulting in color distortion, especially on darker or vibrant Lycra fabrics.
Adhesion Problems:
- Issue: Inks may not adhere well to Lycra due to its smooth, synthetic surface.
Inconsistent Ink Coverage:
- Issue: Achieving consistent ink coverage on Lycra can be tricky, as the fabric’s stretch can lead to uneven prints.
Ghosting or Smudging:
- Issue: When printing on Lycra, ghosting (a shadow effect) or smudging can occur, especially on complex designs.
Heat Sensitivity:
- Issue: Lycra is highly heat-sensitive, which can lead to fabric shrinkage, damage, or distortion when exposed to high curing temperatures.
Ink Bleeding on Dark Fabrics:
- Issue: Dark or heavily dyed Lycra fabrics can cause ink to bleed, impacting the final print color.
These issues highlight the need for choosing the right ink formulations, optimizing curing settings, and making adjustments for cotton’s specific characteristics to achieve consistent, high-quality results in screen printing.
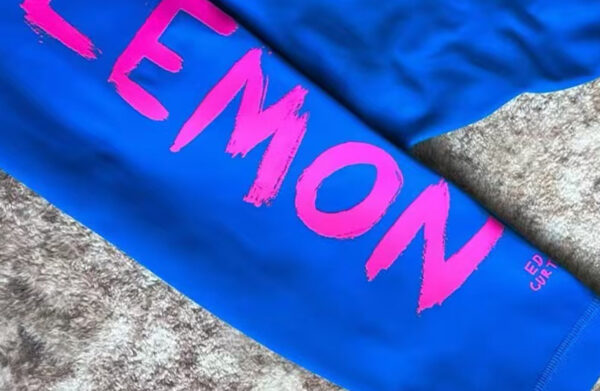
Solutions to Lycra Printing Problems
Here’s a breakdown of effective solutions for each common issue encountered when screen printing on Lycra:
- Use Stretch-Enhanced Inks: Select plastisol inks formulated specifically for stretchable fabrics, or add a stretch additive to your regular plastisol ink. These inks maintain flexibility, allowing them to expand and contract with the Lycra fabric without cracking or peeling.
- Print with a Thinner Ink Layer: Applying too much ink can exacerbate cracking. Use a higher mesh screen count to deposit a thinner, more even layer of ink that remains durable when stretched.
- Apply a Dye-Blocking Underbase: Printing a migration-blocking underbase, typically a white or gray layer, acts as a barrier to prevent the fabric dye from bleeding into the ink.
- Lower Cure Temperature: Dye migration increases with heat, so using low-cure inks can help reduce this effect. Aim for curing temperatures that don’t exceed the dye’s activation temperature, which will help stabilize the color and prevent migration.
- Pre-Treat the Fabric: Apply a fabric primer or adhesion enhancer on the Lycra before printing. This extra step can help the ink bond effectively, especially on slick, synthetic surfaces.
- Low-Cure Inks: Lycra is sensitive to heat, so use low-cure plastisol inks that adhere well to synthetics. These inks cure at lower temperatures, minimizing the risk of adhesion problems and fabric damage.
- Use High Mesh Count Screens: A higher mesh count (e.g., 160–200) helps control the amount of ink deposited, resulting in smoother and more consistent prints.
- Maintain Fabric Tension: Lycra’s stretchiness can cause distortions in the design. Use a frame or stretcher to keep the fabric taut during printing to ensure even ink distribution.
- Flash Dry Between Colors: For multi-color prints, briefly flash dry each color before applying the next. This minimizes smearing and ensures cleaner layers.
- Use a Release Agent: Release agents help inks separate cleanly from screens, reducing the likelihood of ghosting. This can be especially helpful on detailed designs or multi-layer prints.
- Switch to Low-Cure Inks: Low-cure inks designed for Lycra and synthetic fabrics allow you to cure prints at a lower temperature, reducing the risk of shrinking or distorting the fabric.
- Consider Forced-Air or Infrared Drying: If using a conveyor dryer, opt for one with a forced-air setting to keep the curing temperature consistent but low. Infrared dryers can also reduce the need for direct heat on the fabric, minimizing distortion.
- Use an Opaque White Underbase: A white or light underbase layer prevents darker dyes from affecting the final print color, allowing the top color layer to appear as intended.
- Test Ink Compatibility: Check the compatibility of your ink with darker fabrics. Some plastisol inks contain anti-bleed properties that make them suitable for dark or vibrant Lycra fabrics.