What is Plastisol in Screen Printing?
Plastisol is a type of ink used in screen printing that is widely favored for its durability, vibrancy, and versatility. It’s made primarily from PVC (polyvinyl chloride) resin, which is suspended in a plasticizer to create a thick, creamy consistency. Unlike water-based inks, plastisol ink doesn’t dry out unless heated to a specific temperature, which gives printers more time to work with it. It’s particularly popular in the textile printing industry, but also finds applications in other industries requiring high-quality prints.
In plastisol screen printing, the ink is applied to a screen mesh through a stencil and then transferred onto fabric or another substrate. The screen printing process allows for high levels of detail, making plastisol an excellent choice for creating bold designs on t-shirts, hats, and various apparel.
One of the key features of plastisol ink is its ability to produce bright, opaque colors on dark fabrics. This is particularly important when printing on materials like black t-shirts or other dark textiles, where water-based inks might struggle to stand out.
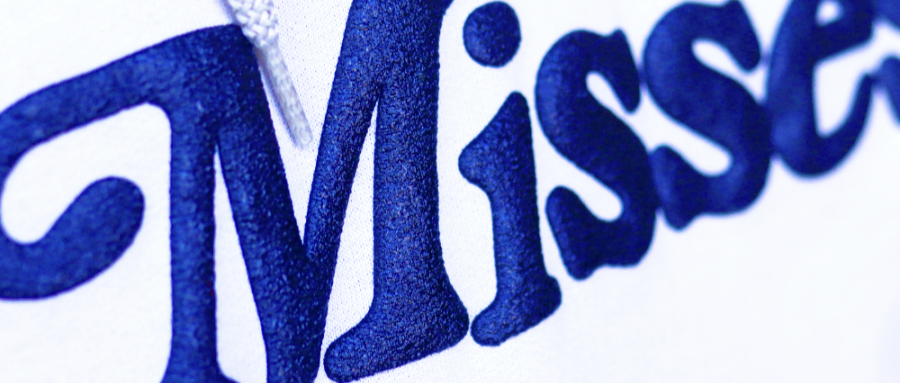
Is Plastisol Printing Good?
When considering whether plastisol screen printing is a good option, several factors come into play.
Pros of Plastisol Printing:
- Durability: Plastisol prints are known for their durability and can withstand repeated washing without fading. This makes it ideal for garments that will be worn frequently.
- Vibrancy: Plastisol inks offer intense, vibrant colors that can pop, even on dark fabrics. The thick consistency helps achieve a solid, full coverage.
- Versatility: Plastisol can be used on a variety of materials beyond just fabric, such as plastic, metal, and paper.
- Ease of Use: Unlike water-based inks that can dry out quickly, plastisol ink stays wet on the screen for a longer time. This gives screen printers the flexibility to work at a comfortable pace, especially during large print runs.
Does Plastisol Ink Dry Out?
One of the most significant benefits of plastisol ink is that it doesn’t dry out unless heated. This characteristic makes it ideal for screen printers who may be working on a large batch of prints or need time to make adjustments to their design. Since plastisol is essentially a plastic-based ink, it remains in its liquid state indefinitely unless exposed to heat. This is a stark contrast to water-based inks, which begin to dry and clog the screen during the printing process if not used promptly.
However, while plastisol ink won’t dry out on the screen, it can still dry on the printing surface, which means the design needs to be cured properly to set the ink permanently. This process usually involves passing the printed garment through a plastisol screen printing machine with a conveyor dryer or using a flash dryer to heat the ink to the necessary temperature.
How Long Can Plastisol Ink Stay on a Screen?
Plastisol ink can stay on a screen for a relatively long time without drying out. As long as the ink is not exposed to excessive heat or direct sunlight, you can leave it on the screen for hours or even days. This is one of the reasons plastisol screen printing is preferred in large runs or when printing multiple colors. Screen printers don’t have to rush to clean the screens after each print job, unlike water-based inks, which dry quickly and require fast action.
If the ink is left on the screen for an extended period, it’s important to clean the screen before it becomes too thick to work with. If you’re using plastisol ink in a high-volume production setting, it’s common to store excess ink in sealed containers to avoid any contamination or drying.
What Surfaces Can Plastisol Ink Print On?
Plastisol ink is known for its versatility and can be used to print on a wide range of surfaces. It’s especially popular for printing on fabric, but it can also be used on other materials, such as:
- Textiles/Fabric: Plastisol is commonly used for t-shirt printing, as well as other clothing items like hoodies, hats, and bags. The ink adheres well to cotton, polyester, and cotton-blend fabrics, offering vibrant colors and a durable finish.
- Plastic: Many promotional items like pens, plastic cups, and signage are made from plastic materials that are compatible with plastisol ink. This makes it ideal for creating custom items in addition to apparel.
- Paper/Cardboard: Plastisol can also be used for printing on paper products, although it is more commonly used on fabric and plastic.
- Metal: Items like metal signs or promotional items can be printed with plastisol ink, offering long-lasting prints and vibrant colors.
The primary limitation to plastisol screen printing is that it requires heat for curing. As a result, it may not be suitable for materials that cannot withstand high temperatures, such as certain types of delicate fabric or heat-sensitive plastic.
What Happens if You Over-Cure Plastisol Ink?
Curing plastisol ink is an essential part of the printing process. It involves exposing the printed garment to a heat source (typically a plastisol screen printing machine with a conveyor dryer) to fully set the ink. If the ink isn’t cured enough, it will remain soft and prone to washing off over time. However, over-curing plastisol ink can cause issues as well.
Over-curing the ink can lead to:
- Brittleness: When plastisol ink is over-cured, it can become brittle and may crack or peel off the fabric over time. This is particularly an issue for designs that are meant to be soft to the touch.
- Shiny Finish: Over-cured plastisol prints may develop a glossy, shiny finish that some customers may not find appealing. This is because the plastic in the ink has hardened too much.
- Loss of Vibrancy: Excessive heat can also dull the colors of the print, causing the vibrant appearance to fade.
It’s crucial to monitor the curing process closely to ensure the ink is properly set without being overexposed to heat.

How Long Does Plastisol Ink Last?
The longevity of plastisol ink is one of its strongest selling points. If properly cured and applied to a suitable surface, plastisol prints can last for many years without significant fading or wear. In fact, some high-quality plastisol prints on apparel can endure dozens of washings while maintaining their vibrancy and opacity.
That said, the lifespan of a plastisol print can be affected by factors such as the type of fabric, the curing temperature, and the washing conditions. To maximize the lifespan of plastisol prints, it’s recommended to wash printed garments inside out and use cold water for washing.
Conclusion
Plastisol screen printing remains one of the most popular and reliable methods for creating vibrant, durable prints on a wide variety of surfaces. Whether you’re looking for plastisol screen printing near me or considering purchasing a plastisol screen printing machine or kit, this printing method offers incredible versatility and long-lasting results.
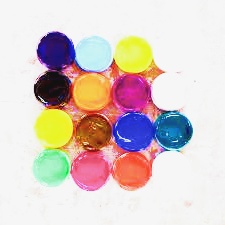
While plastisol ink has some environmental drawbacks, its ease of use, durability, and ability to produce high-quality designs make it a top choice for screen printing professionals and hobbyists alike. If you’re considering adding plastisol screen printing to your business or starting a DIY project, this ink type is sure to deliver results that will stand the test of time. Just remember to cure your prints correctly, and always consider the fabric or material you’re working with to ensure the best possible outcome.