Selecting the right screen printing mesh size is a critical step in achieving optimal results in your printing projects. The mesh size directly affects the amount of ink passed through the screen, impacting the final appearance of your prints. This guide will walk you through the factors to consider when determining screen mesh size, from the type of frame to the nuances of mesh count, helping you make informed decisions for your screen printing needs.
Type of Frame
The type of frame you choose for your screen printing project plays a significant role in determining the appropriate mesh size. Frames are essential for holding the mesh taut and ensuring consistent prints. There are two primary types of frames: wood and aluminum.
Wooden Frames
Wooden frames are cost-effective and commonly used by beginners and small-scale screen printers. They offer a sturdy structure, but over time, they can warp due to exposure to water and humidity, which can affect the tension of the screen printing mesh. While wooden frames are a budget-friendly option, they may not be the best choice for precision work requiring consistent tension.
Aluminum Frames
Aluminum frames are the preferred choice for professional screen printers. They are lightweight, durable, and resistant to warping, making them ideal for maintaining consistent tension in the screen printing mesh. The stability provided by aluminum frames ensures more accurate and detailed prints, especially when working with intricate designs and fine mesh counts.
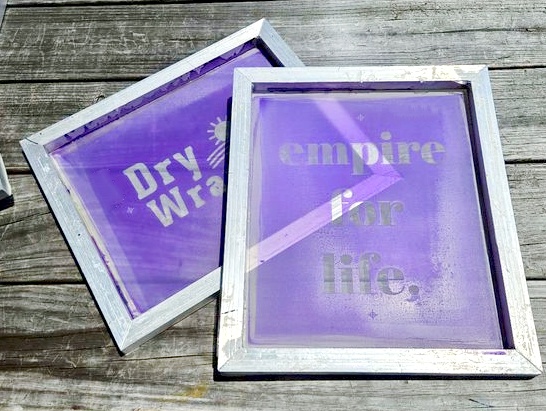
Aluminum Frame
Aluminum frames offer several advantages over wooden frames, particularly in professional settings where consistency and precision are paramount. The durability of aluminum ensures that the screen printing mesh remains taut over extended periods, reducing the likelihood of misprints or variations in print quality.
Benefits of Aluminum Frames
- Durability: Aluminum frames are resistant to warping and water damage, ensuring long-term reliability.
- Lightweight: Despite their strength, aluminum frames are lightweight, making them easier to handle and maneuver during the printing process.
- Consistent Tension: The stability of aluminum frames helps maintain consistent tension on the screen printing mesh, which is crucial for achieving uniform prints.
- Versatility: Aluminum frames can accommodate a wide range of mesh sizes, making them suitable for various printing projects, from large, bold designs to intricate, detailed prints.
Mesh Size
Mesh size refers to the number of threads per inch in the screen printing mesh. It is a crucial factor that determines how much ink passes through the screen and onto the substrate. The mesh size you choose will depend on the type of ink you’re using, the level of detail in your design, and the type of material you’re printing on.
Understanding Mesh Count
Mesh count is measured in threads per inch (TPI), with a higher count indicating a finer mesh. For example, a 110 mesh count means there are 110 threads per inch. Lower mesh counts allow more ink to pass through, making them suitable for bold designs and thicker inks like plastisol ink. Higher mesh counts are better suited for detailed designs and thinner inks.
Choosing the Right Mesh Size
The mesh size you select should be aligned with the specific requirements of your project:
- Low Mesh Count: Best for bold, simple designs that require a lot of ink coverage, such as printing on dark fabrics or using specialty inks like glitter or puff inks.
- Medium Mesh Count: Versatile and suitable for general-purpose screen printing, offering a balance between detail and ink coverage.
- High Mesh Count: Ideal for fine details, halftones, and printing on delicate materials where less ink is needed.
The Most Common Mesh Size
For many screen printing projects, a medium mesh count around 110 to 160 threads per inch is the most common choice. This range offers a good balance between detail and ink coverage, making it versatile for printing on various materials and with different types of ink, including plastisol ink.
Why 110-160 Mesh is Popular
- Versatility: Suitable for a wide range of designs, from text to simple graphics, and works well with most inks.
- Ink Coverage: Provides adequate ink coverage without sacrificing too much detail, making it ideal for general-purpose printing.
- Ease of Use: Medium mesh sizes are forgiving and easier to work with, making them a good choice for beginners and experienced printers alike.
Low Mesh Count
Low mesh count screens, typically ranging from 25 to 85 threads per inch, are used when printing with thicker inks or when a lot of ink coverage is needed. These screens are ideal for specialty printing, such as applying glitter, metallic, or puff inks, where the goal is to create bold, eye-catching designs.
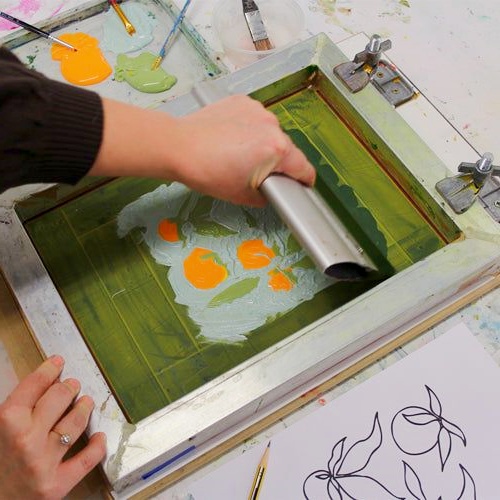
When to Use Low Mesh Count
- Thick Inks: When using inks like plastisol ink, which has a thicker consistency, a low mesh count screen allows for better ink flow and coverage.
- Bold Designs: For large, simple designs that don’t require fine detail, low mesh count screens are ideal as they allow more ink to pass through.
- Special Effects: Low mesh count screens are perfect for creating special effects, such as raised textures or glitter prints, by allowing the thick, textured inks to lay down heavily on the substrate.
High Mesh Count
High mesh count screens, typically ranging from 200 to 400 threads per inch, are used for printing fine details and intricate designs. These screens are better suited for printing with thin inks, where precision and clarity are essential.
When to Use High Mesh Count
- Fine Details: High mesh count screens are necessary for designs that require a high level of detail, such as intricate patterns, small text, or halftone prints.
- Thinner Inks: When using thin inks, such as water-based inks, a high mesh count screen helps control the amount of ink deposited, ensuring sharp, clean lines.
- Delicate Materials: High mesh count screens are also suitable for printing on delicate materials, where minimal ink deposition is required to avoid saturating the fabric.
Exposure Records
Keeping accurate exposure records is essential for achieving consistent results in screen printing. Exposure records help you track the correct exposure times for different mesh sizes and designs, ensuring that each screen is exposed correctly.
Importance of Exposure Records
- Consistency: By maintaining detailed records, you can replicate successful prints and avoid trial-and-error in future projects.
- Quality Control: Accurate exposure records help prevent issues like under-exposure or over-exposure, which can lead to poor print quality.
- Efficiency: With exposure records, you can quickly set up screens for new projects, knowing the exact exposure times needed for each mesh size and design.
How to Maintain Exposure Records
- Log Details: Record the mesh size, exposure time, type of emulsion used, and any other relevant details for each screen you expose.
- Review and Adjust: Regularly review your exposure records and make adjustments as needed based on the results of your prints.
- Store Securely: Keep your exposure records in a safe, accessible place, whether digitally or in a physical logbook, so you can reference them easily for future projects.
Conclusion
Determining the right screen printing mesh size is crucial for achieving the best results in your printing projects. By considering factors like the type of frame, mesh count, and the specifics of your design, you can select the perfect mesh size to ensure your prints come out just as you envision them. Whether you’re working with thick plastisol ink for bold designs or using a high mesh count for intricate details, understanding the role of mesh size will help you achieve professional-quality results every time.