Introduction
Dye migration is a common challenge in screen printing, particularly when working with synthetic fabrics and dark-colored garments. This phenomenon can ruin the vibrancy and clarity of your prints, leading to dissatisfied customers and wasted materials. Understanding what color migration is and how to control it is crucial for achieving high-quality, durable prints. In this article, we’ll explore the nature of dye migration, what causes it, and the best practices for preventing it in your screen printing projects.
What is Dye Migration?
Color migration occurs when the dye from a garment’s fabric moves into the printed ink layer, altering the appearance and color of the print. This issue is most commonly seen with polyester or polyester-blend fabrics, which are often dyed with disperse dyes. When exposed to heat, such as during the curing process, these dyes can sublimate and migrate into the plastisol ink, causing the print to become discolored or blurry.
What is Dye Migration Like?
Dye migration typically manifests as a change in the color of the printed design, often resulting in a duller or altered hue. For example, a white print on a red polyester shirt might turn pink as the red dye seeps into the white ink. This can happen immediately during the curing process or gradually over time, leading to customer complaints and returns. The severity of color migration can vary based on factors such as fabric type, dye stability, and the curing temperature used.
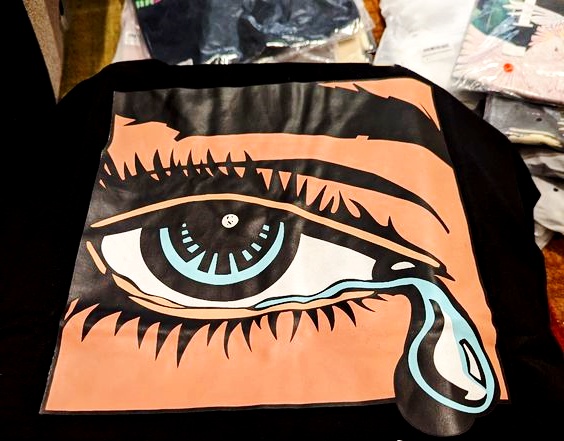
How Do You Control It?
Controlling dye migration requires a multi-faceted approach, involving careful selection of materials, proper printing techniques, and appropriate curing methods. Here are some strategies to help you minimize or prevent dye migration in your screen printing projects:
- Choose Low-Bleed Inks: One of the most effective ways to control color migration is by using low-bleed plastisol inks specifically formulated to resist dye migration. These inks contain additives that help block the dye from migrating into the print, ensuring the design remains vibrant and true to color.
- Use an Underbase: Printing an underbase layer, typically with a low-bleed or dye-blocking white ink, can create a barrier between the fabric and the top colors. This underbase helps to prevent the fabric’s dye from reaching the top layer of ink, reducing the risk of color distortion.
- Lower Curing Temperatures: Since color migration is often triggered by heat, lowering the curing temperature can help minimize the risk. Many manufacturers offer low-cure plastisol inks that cure at lower temperatures, reducing the chances of dye migration.
- Test Fabrics Before Printing: Before committing to a large print run, it’s essential to test your fabrics to see how they react to your inks and curing process. This step can help you identify potential color migration issues early and adjust your approach accordingly.
- Use Dye-Blocking Additives: If you’re working with challenging fabrics or experiencing persistent dye migration issues, consider using dye-blocking additives. These additives can be mixed into your plastisol ink to enhance its resistance to dye migration.
- Proper Ink Application: Applying the right amount of ink is crucial. Too much ink can increase the risk of dye migration, as the thicker ink layer provides more opportunity for the dye to move. On the other hand, too little ink might not provide adequate coverage to block the dye.
- Choose the Right Fabrics: Whenever possible, choose fabrics that are less prone to dye migration. Natural fibers like cotton or fabric blends with a lower polyester content are generally less likely to experience dye migration than 100% polyester garments.
Additional Tips to Prevent Dye Migration
While the above methods are the most common and effective, there are additional practices you can adopt to further reduce the risk of color migration:
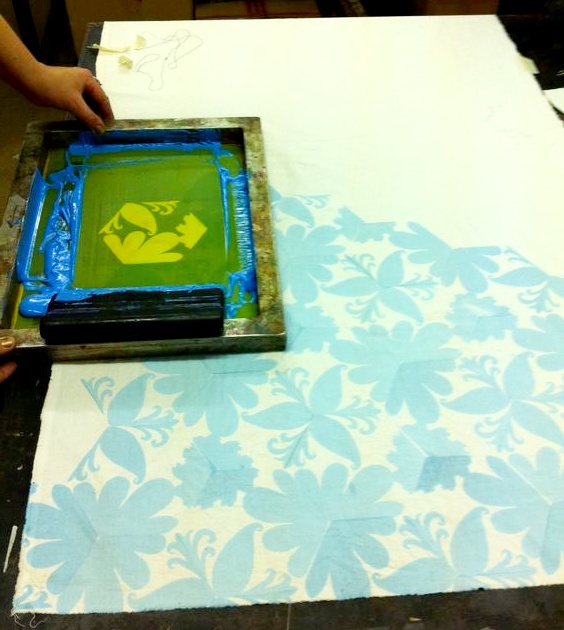
- Control the Environment: Humidity and temperature in your printing environment can affect how inks cure and how dyes behave. Maintaining a stable, controlled environment can help mitigate the factors that contribute to dye migration.
- Use Barrier Films: In extreme cases, where dye migration is particularly problematic, you can use a barrier film between the fabric and the ink. This film acts as a physical barrier, preventing the dye from reaching the ink.
- Monitor Curing Times: Over-curing can exacerbate dye migration by increasing the time the ink is exposed to heat. Be sure to monitor and adjust your curing times to ensure the ink is properly cured without being overheated.
- Educate Your Team: Ensuring that everyone involved in the printing process understands the risks of dye migration and how to prevent it is crucial. Regular training and updates on best practices can help maintain the quality of your prints.
Conclusion
Color migration is a challenging issue in screen printing, but with the right techniques and materials, it can be controlled effectively. By choosing low-bleed inks, using an underbase, lowering curing temperatures, and testing your fabrics, you can significantly reduce the risk of dye migration and ensure your prints remain vibrant and durable. Stay vigilant and proactive in your approach, and you’ll be able to deliver high-quality products that meet your customers’ expectations.