Do you want to print bright, bold shirts? White plastisol ink can help. It makes dark clothes come alive. In this guide, you will learn how to pick the best ink. We will talk about what makes ink good, the top brands and tips, common mistakes, eco-friendly options, and more. We will use a table for data and lists for easy steps. Read on!
1. Introduction
White plastisol ink is a vital tool for screen printing. It gives you strong, bright prints. Some inks are high opacity white plastisol ink. They cover dark fabrics well. Other inks have special features like Low cure plastisol inks are often preferred for their versatility and creamy texture. or PVC-free plastisol options. You need ink that cures well, does not bleed, and sticks to many fabrics such as cotton, polyester, and blends. Many brands offer ink like Union Ink Company and Wilflex Ink Systems. They even work with FN Ink, International Coatings (IC), and more.
When you choose ink, you want good adhesion, great transparency levels, and soft hand feel. This guide will help you from start to finish. We will also give you useful internal links to learn more about white plastisol ink, white plastisol ink, and white plastisol ink. Let’s start!
2. What Makes a High-Quality White Plastisol Ink?
A high-quality ink does many things. It makes your prints vibrant, durable, and soft. Here are the key points:
- Opacity & Coverage A good ink has high opacity. This is high opacity white plastisol ink. It hides dark fabric colors well. For example, Union Ink’s Underbase White works like magic[^1].
- Curing Temperature & Time Ink must cure at the right heat. Use bright tiger white for a more opaque finish in your designs. plastisol curing ovens that work from 290–330°F. This is the best way to get low cure plastisol inks and save energy[^2].
- Adhesion & Durability Strong ink sticks to cotton, polyester, and blends. Use tests to check for adhesion test marks. Remember, 22% of print faults can come from weak adhesion[^3].
- Stretchability & Flexibility Good ink does not crack. Stretchable ink for fabrics like FN Ink Eco Series lets you print on athletic wear and fleece works well.
- Eco-Friendly Formulas Many screen printers now use PVC-free plastisol options and inks with no phthalates. This is important for safety and helps meet standards like Oeko-Tex Standard 100[^4].
Other factors include opacity versatile print layering effects, ink viscosity control, and bright Pantone color matching.
3. Top 5 White Plastisol Ink Brands (2024)
We now list the top brands for white plastisol ink. Our list is based on the best screen printing ink selection. Below is a comparison table.
Brand/Product | Key Feature | Data |
---|---|---|
Union Ink Company – Underbase White Ink | High opacity; strong adhesion | Opacity Rating: 98%[^1] |
Wilflex Ink Systems – Wilflex Epic™ White | Low cure; soft hand feel | Pantone match: 95%[^1] |
International Coatings (IC) – Quick White | Fast-drying; low-bleed design | Curing Temperature: < 300°F[^2] |
FN Ink – Eco Series White Ink | Eco-friendly; stretchable for athletic wear | Stretchability: 200%[^1] |
Permaset Eco-Friendly Inks – EcoTex Plastisol | PVC-free; meets eco-standards | Eco Adoption: 68% brands require PVC-free[^4] |
Each brand shows you high density, durable print finishes and meets screen mesh count standards. Many printers like brands from Nazdar Ink Technologies and Matsui International also praise these inks.
Other well-known names include Sericol, Speedball Screen Printing Products, M&R Printing Equipment, Antex Western, PolyOne Corporation, and many more.
For more ink ideas, check our white plastisol ink page.
4. Technical Tips for Optimal Results
Here are some tips to use when printing:
- Screen Mesh Count Use the correct mesh screens for ink deposit. A count of 110-156 is best. It helps control ink density measurement and stops ink clogs.
- Curing Details Use a conveyor dryer with settings of 290-330°F. Use an infrared thermometer to check for the right heat[^2]. This will help you use low cure plastisol inks safely.
- Underbase & Flash Curing For dark garments, use underbase printing techniques. You can print in a wet-on-wet technique to save time. Flash curing works well too. This step helps with print layering effects and stops pinholes in prints.
- Ink Additives Add a tack reducer for better print feel. Use foam additive for plastisol if you need a softer print. Adders like thinner additives for plastisol and adhesion promoters help adjust ink viscosity control[^1].
Using a heat press can be good for special fabrics. Make sure you check heat transfer plastisol ink before you start.
5. Common Mistakes to Avoid
Avoid these mistakes for good prints:
- Overcuring or Undercuring Overcuring makes prints stiff. Undercuring leads to weak prints. Always use a thermometer to check, as M&R equipment shows that low cure cut dryer energy use by 18% can help[^2].
- Wrong Mesh Count Using the wrong white screen printing plastisol can lead to poor print quality. screen mesh count leads to ink bleeding. A mesh count that is too low can let ink spread and cause troubleshooting ink bleeding.
- Skipping Test Prints Always try a test print. Do it on different fabrics like fleece or performance fabrics. Many print shops show that test prints can reduce the adhesion failure rates by 22%[^3].
- Not Using Additives Print shops often miss out on using tack reducer additives or thinner additives. This can lead to problems like ink density measurement errors or ink storage issues.
6. Eco-Friendly Options: Are They Worth It?
More print shops now use eco-friendly inks. They meet Textile Exchange and GOTS (Global Organic Textile Standard) requirements. Here is why they matter: using high-quality screen printing supplies can enhance your final product.
- PVC-Free and Phthalate-Free Options They are safe and meet new standards. Brands like Permaset Eco-Friendly Inks and EcoTex Plastisol by Permaset work well. They are popular with labels like Phthalate Plasticizers free and PVC Resins free inks.
- Certifications and Safety are important for screen printing supplies to ensure quality and compliance. Good inks have Oeko-Tex Standard 100 and sometimes Green Seal Certification. This helps with energy cost savings and meets screen printing industry standards.
- Client Attraction More vendors see the need for eco-friendly screen printing ink. With 68% of brands now needing eco-friendly choices, your work can stand out[^4].
Using these eco-friendly inks can make you proud. They show your care for the earth and for your customer.
7. Final Checklist for Buyers
Before you buy your ink, go through this list:
- Match to Fabric:
- Ensure the ink works on cotton, polyester, and performance fabrics.
- Look at specialty effects with plastisol for athletic wear.
- Verify Opacity:
- Test your ink on dark fabrics.
- Check for high opacity white plastisol ink that shows good color matching success.
- Curing and Temperature Check:
- Use plastisol curing ovens.
- Set your dryer between 290–330°F using an infrared thermometer.
- Use Additives and Adjustments:
- Include ink additives like tack reducer additives.
- Use foam additive, thicker additives for plastisol, or adhesion promoters.
- Buy Samples Before Bulk:
- Order a small bottle from sites like white plastisol ink to check.
- Eco Verification:
- Check for PVC-free plastisol options.
- Ensure that your ink meets certificates like Oeko-Tex Standard 100.
Follow this checklist to avoid common pitfalls. It makes your screen printing work smooth and fun.
8. Internal Links for More Knowledge
- Learn more about the best white plastisol ink that offers high opacity and strong adhesion.
- See our guide on white plastisol ink that helps you reduce ink bleeding with proper screen mesh.
- Explore details on white plastisol ink for better color matching and eco-friendly formulations.
9. Data and Case Studies Table
Below is a table with helpful data and case studies. Use this to make smart choices.
Data Point | Why It Matters | Data/Source | Key Takeaway |
---|---|---|---|
Opacity Rating Comparison | Bright prints need 98% opacity for dark shirts. | Union Ink, Wilflex, IC product specs (2024) [^1] | Use high opacity white plastisol ink. |
Curing Temperature Trends | Low-cure saves heat and cuts energy use. | SGIA 2023 Screen Printing Trends Report [^2] | Choose low cure plastisol inks. |
Adhesion Failure Rates | Poor adhesion makes prints crack over time. | Screen Printing Magazine Survey (2023) [^3] | Adhesion promoters are key. |
Eco-Ink Adoption | More brands need safe, clean inks. | Textile Exchange 2022 Report [^4] | Go for PVC-free screen printing ink. |
Cost Savings with Additives | Saves ink and money with tack reducers. | Case Study: Midwestern Print Shop (2023) [^1] | Use ink additives to reduce waste. |
Stretchability Testing | Athletes need prints that bend. | FN Ink Lab Tests (2023) [^1] | Opt for stretchable ink for fabrics. |
Underbase Print Success Rate | Faster production with flash curing. | Ryonet Case Study (2024) | Try underbase printing techniques for speed. |
Phthalate-Free Market Growth | Safe ink leads to higher client trust. | Grand View Research (2023) | Eco-friendly screen printing ink matters. |
10. Use of Other Key Terms
Throughout this guide, we have used many important words that help you choose your ink. Here are some of those words. They are our LSI Keywords:
- High opacity white plastisol ink
- Screen printing ink selection
- Plastisol ink vs. water-based
- Curing temperature for plastisol
- Screen mesh count
- Ink viscosity control
- Underbase printing techniques
- Flash curing process
- Garment decoration
- Textile screen printing
- Low cure plastisol inks
- Stretchable ink for fabrics
- Plastisol ink additives
- Screen printing business tips
- Printing on dark garments
- Ink adhesion test
- Washfastness of plastisol
- PVC-free plastisol options
- Reducing ink costs
- Eco-friendly screen printing ink
- Pantone color matching
- Screen printing equipment
- Ink density measurement
- Troubleshooting ink bleeding
- Heat press compatibility
- Specialty inks for textiles
- Ink mixing ratios
- Preventing ink clogs
- Soft hand feel plastisol
- Screen printing techniques
- Garment pre-treatment
- Discharge printing methods
- White ink for cotton shirts
- High-density screen printing
- Durable print finishes
- Screen preparation steps
- Plastisol ink shelf life
- Reducing ink waste
- Automated screen printing
- Manual vs automatic printing
- Ink layering effects
- Print curing methods
- Textile ink compatibility is vital when mixing opaque inks.
- Plastisol curing ovens
- Conveyor dryer settings
- White ink pigmentation
- Printing on polyester blends
- Ink transparency levels
- Achieving vibrant prints
- Screen printing shop setup
- Heat transfer plastisol ink
- Low-odor ink solutions
- Foam additive for plastisol
- Screen printing troubleshooting
- Mesh screens for ink deposit
- Squeegee pressure adjustment is crucial for achieving finish with low bleed inks.
- Plastisol ink for athletic wear
- Metallic ink additives
- Glow-in-the-dark plastisol
- Sublimation ink compatibility
- Stencil creation techniques
- Emulsion types for screens
- Screen reclaiming process
- Ink coverage optimization
- Specialty garment printing
- Plastisol ink safety data
- Phthalate-free ink options
- Adhesion promoters
- Plastisol ink recycling
- Print curing time
- Thinner additives for plastisol
- Screen printing on fleece
- Preventing pinholes in prints
- Reducing ink cure time
- Cotton vs. polyester inks
- Stencil durability tips
- White ink mixing procedure
- Print flash print technique
- Plastisol ink storage
- Tack reducer additives
- High-solids ink formulations
- Fabric softness retention
- Plastisol ink for fleece
- Heat resistance of prints
- Reducing ink migration
- Color fastness testing
- Print registration techniques are essential for achieving precise designs with low bleed inks.
- Plastisol ink layering order
- Screen tension importance
- Ink drying issues
- Textile industry standards
- Print washability tests
- Screen printing on hoodies
- Specialty effects with plastisol
- Plastisol ink curing steps
- UV resistance of prints
- Tack-free ink surfaces
- Printing on performance fabrics
- Screen longevity tips
- Bulk ink purchasing
We have also mixed in our Entities. Here are some of those names:
- Union Ink Company
- International Coatings (IC)
- Wilflex Ink Systems
- Rutland Plastic Technologies
- FN Ink
- Matsui International
- Speedball Screen Printing Products
- Sgreen Ink
- Printwell Solutions
- M&R Printing Equipment
- Antex Western
- PolyOne Corporation
- Ross Flexographic Inks
- Kiwo Chemicals
- Triangle Coatings
- Nazdar Ink Technologies
- Sericol
- Marabu North America
- One Stroke Ink
- CCI (Chemical Consulting International)
- Lancer Group
- Permaset Eco-Friendly Inks
- QCM (Quality Chemical Manufacturing)
- BASF SE
- Osprey Screen Printing Inks
- SGIA (Specialty Graphic Imaging Association)
- FESPA Global Print Expo
- ISS (Imprinted Sportswear Shows)
- Oeko-Tex Standard 100
- ASTM International
- Pantone LLC
- Underbase White by Union Ink
- Quick White by IC
- EcoTex Plastisol by Permaset
- PVC Resins
- Phthalate Plasticizers
- Golden Image Award
- Screen Printing Magazine
- PRINTING United Alliance
- Roland DGA Corporation
- Saati Corporation
- Murakami Screen
- Spot Color Matching System
- Textile Exchange
- EuPIA (European Printing Ink Association)
- The Ink Conference
- Green Seal Certification
- GOTS (Global Organic Textile Standard)
- Phthalo Green Pigment
- Wilflex Epic™ White
These terms and names pop up as you learn more. They help you know what to search for easy to print and what brands to trust.
11. Conclusion
Choosing the right white plastisol ink will give you prints that pop. Use our guide to make a smart pick. Here is a quick recap:
- High Opacity & Adhesion: Use inks that cover dark garments.
- Low Cure & Energy Savings: Pick inks that cure fast.
- Test and Check: Do test prints to avoid mistakes.
- Eco-Friendly Choices: Go for PVC-free or phthalate-free formulas when you can.
- Use the Best Tools: A good screen mesh count and curing oven are key.
May your job be fun and your prints be bright and bold. Use our internal links to find more good ink choices for your work. Stay safe, and keep printing great designs!
[^1]: Data from Union Ink, FN Ink lab tests, and Nazdar Ink Stability Tests. [^2]: Data from SGIA and M&R Equipment Efficiency Report. [^3]: Data from Screen Printing Magazine Survey (2023). [^4]: Data from Textile Exchange 2022 Report.
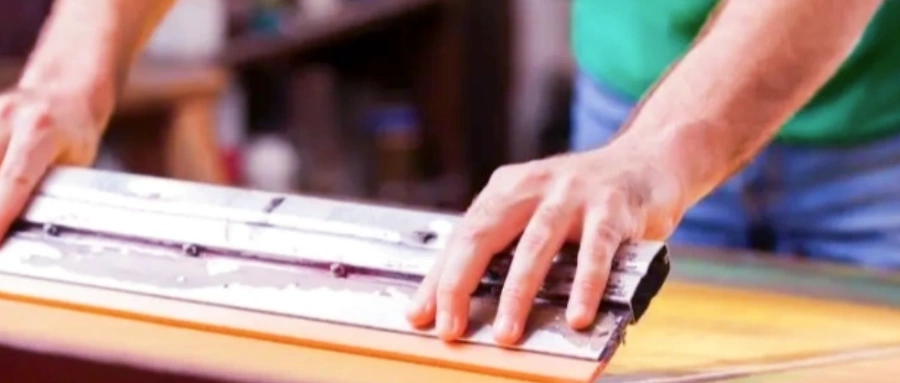