When it comes to screen printing, plastisol ink printing remains one of the most popular methods due to its durability and versatility. However, like any printing method, it comes with its advantages and disadvantages. This article will delve into the pros and cons of plastisol printing, explore how it works, and help you decide if it’s the right choice for your project.
How Plastisol Ink Printing Works
Plastisol printing is a widely-used technique in the screen printing industry, especially for apparel. The process begins with plastisol ink, a type of ink that consists of PVC particles suspended in a plasticizer. This ink remains liquid until it is exposed to heat, typically around 320°F (160°C), at which point it solidifies and bonds with the fabric.
The process starts by creating a screen, which is essentially a stencil for your design. The screen is placed over the fabric, and plastisol ink is pushed through the screen’s open areas using a squeegee. The ink sits on top of the fabric rather than soaking into it. Once the design is printed, the fabric is exposed to heat to cure the ink, ensuring it adheres properly and becomes durable.
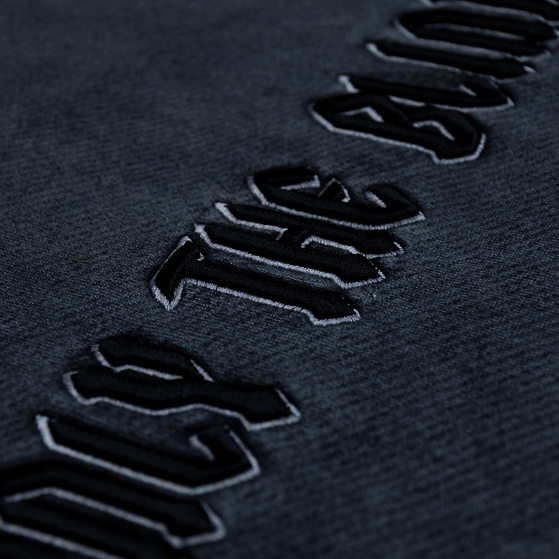
The Pros of Plastisol Ink Printing
Durability and Longevity
One of the standout advantages of plastisol ink printing is its durability. The ink creates a thick, opaque layer on top of the fabric, which is resistant to fading, cracking, and peeling over time. This makes plastisol printing ideal for products that need to withstand regular use and washing, such as T-shirts, hoodies, and sportswear.
Versatility
Plastisol ink is incredibly versatile and can be used on a wide range of fabrics, including cotton, polyester, and blends. Its ability to produce vibrant, opaque colors on both light and dark fabrics makes it a preferred choice for detailed and colorful designs. Additionally, plastisol inks can be mixed to create custom colors, and specialty inks like metallic, glitter, and puff can be used for unique effects.
Ease of Use
Plastisol ink is relatively easy to work with, even for beginners in screen printing. Unlike water-based inks, which can dry out and clog screens quickly, plastisol ink stays wet until it is heat-cured, giving printers more flexibility during the printing process. This property also makes plastisol ink well-suited for high-volume printing, as screens do not need to be cleaned as frequently.
Consistency in Results
With plastisol ink printing, achieving consistent, high-quality results is easier compared to some other printing methods. The ink’s thickness and opacity ensure that the printed design looks the same across multiple prints, making it ideal for large orders where uniformity is essential.
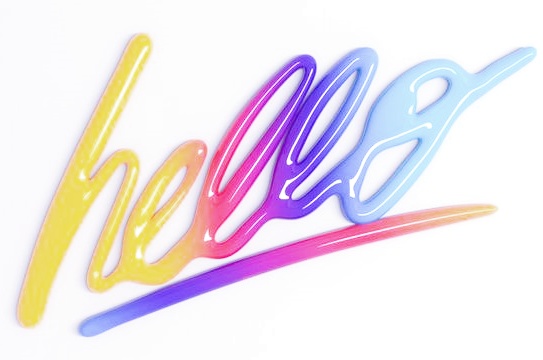
The Cons of Plastisol Ink Printing
Environmental Concerns
One of the main drawbacks of plastisol ink printing is its environmental impact. Plastisol inks are made from PVC, a type of plastic that is not biodegradable. Additionally, the inks often contain phthalates, which are harmful to the environment and human health. While phthalate-free options are available, the overall environmental footprint of plastisol ink remains a concern for eco-conscious brands and consumers.
Thick and Heavy Prints
Another disadvantage of plastisol ink printing is the thick, sometimes heavy feel of the prints on the fabric. Since the ink sits on top of the material rather than soaking in, the print can feel less breathable and more rigid compared to water-based inks. This can be a drawback, especially for fashion brands that prioritize a soft, comfortable hand-feel in their garments.
Heat Sensitivity
Plastisol ink requires high heat to cure, which can be a limitation when printing on heat-sensitive fabrics. Materials like nylon or some synthetic blends may not be able to withstand the high curing temperatures without damage, limiting the types of fabrics that can be used with plastisol ink.
Limited Washability
While plastisol prints are generally durable, they can be prone to certain issues if not cured properly. For example, under-cured prints may crack or peel after washing, and over-cured prints can become brittle. Achieving the right balance during the curing process is essential to ensuring the longevity of the print.
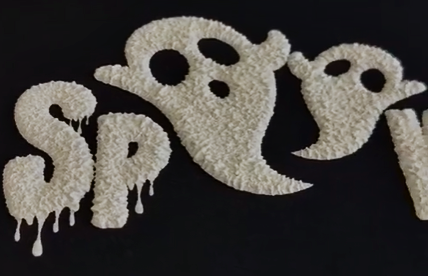
How to tell if plastisol ink printing is right for your project
Deciding whether plastisol ink printing is the best choice for your project depends on several factors. If you need a printing method that offers vibrant, opaque colors, durability, and versatility across different fabric types, plastisol ink may be the ideal option. It’s also a great choice for large orders where consistency and ease of use are important.
However, if environmental sustainability, soft hand-feel, or breathability are your primary concerns, you may want to consider alternatives to plastisol ink. Projects that involve heat-sensitive fabrics may also benefit from different printing methods.
Common Alternatives to Plastisol Ink Printing
While plastisol ink is a popular choice, several alternatives might better suit specific needs:
Water-Based Ink
Water-based inks are an eco-friendlier alternative to plastisol. They soak into the fabric, creating a soft, breathable print that feels like part of the material itself. This type of ink is ideal for fashion-forward brands that prioritize a soft hand-feel and environmental sustainability.
Discharge Ink
Discharge ink is another alternative, especially for printing on dark fabrics. Instead of adding a layer of ink on top of the fabric, discharge ink removes the dye from the fabric, leaving behind a natural color. The result is a soft, vibrant print that is as breathable as the fabric itself.
Hybrid Inks
Hybrid inks combine the best properties of plastisol and water-based inks. These inks offer the soft hand-feel and environmental benefits of water-based inks while maintaining the durability and vibrancy of plastisol. Hybrid inks are a good option for those who want the best of both worlds.
How to Get the Most Out of Your Plastisol Prints
To maximize the quality and longevity of your plastisol prints, it’s important to follow best practices during the printing process:
- Proper Curing: Ensure that the ink is cured at the correct temperature and for the appropriate amount of time. This will prevent issues like cracking, peeling, or brittleness.
- Use the Right Mesh: Selecting the right screen mesh count is crucial for achieving the desired level of detail and ink coverage. Finer details require higher mesh counts, while solid areas may benefit from lower mesh counts.
- Test Before Printing: Always conduct test prints on the same fabric you plan to use for the final product. This allows you to adjust curing times, screen tension, and ink application for optimal results.
- Proper Storage: Store plastisol ink in a cool, dry place to maintain its quality. Keeping screens clean and free of dried ink is also essential to prevent clogging and ensure smooth prints.
Why Scrappy Apparel Is the Right Choice for Your Plastisol Ink Printing Project
When it comes to plastisol ink printing, choosing a reliable partner is key to achieving high-quality results. Scrappy Apparel is a leader in the screen printing industry, offering expert services that ensure your designs are printed with precision and care. Our experienced team uses state-of-the-art equipment and techniques to produce durable, vibrant prints that stand the test of time.
Whether you’re looking for a bold, colorful design or need help choosing the right ink for your project, Scrappy Apparel has the expertise to bring your vision to life. Our commitment to quality, consistency, and customer satisfaction makes us the ideal choice for all your plastisol printing needs.
Conclusion
Plastisol ink printing offers many advantages, including durability, versatility, and vibrant color reproduction. However, it also comes with some drawbacks, such as environmental concerns and a heavier feel on the fabric. Understanding the pros and cons of plastisol printing can help you make an informed decision for your next screen printing project. By considering factors like fabric type, design complexity, and desired finish, you can choose the best ink and printing method to achieve the perfect result. Whether you opt for plastisol or explore alternatives like water-based or discharge inks, the key is to align your printing method with your specific project goals.