When it comes to printing on cotton with screen printing, choosing the right fabric screen printing ink is important. Plastisol ink is commonly used but how well does it work on cotton fabrics? This explores using plastisol ink on cotton and if there are better inks for the job.
Feasibility of Plastisol Inks for Printing on Cotton Fabrics
Plastisol inks are a staple in the screen printing industry due to their versatility, durability, and vibrant color output. These inks are composed of PVC (polyvinyl chloride) particles suspended in a plasticizer, allowing them to remain in a liquid state until heat-cured. The curing process is critical, as it transforms the ink from a semi-liquid to a solid, ensuring a durable bond with the fabric.
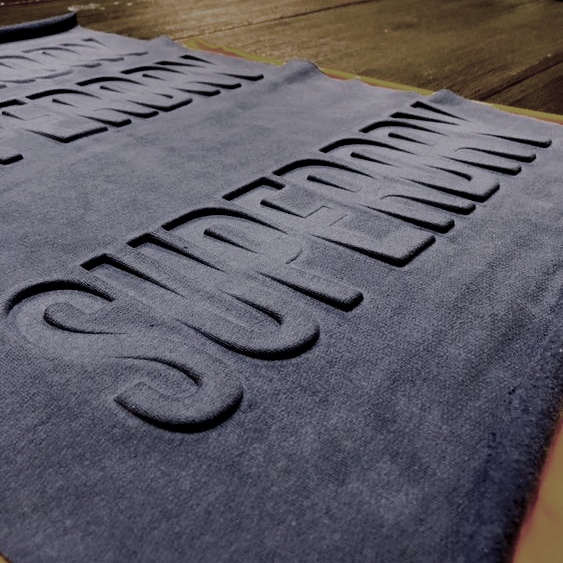
Compatibility with Cotton Fabrics
Cotton is a widely used fabric, prized for its softness, breathability, and moisture absorption. These qualities make cotton an excellent choice for various garments, including T-shirts, hoodies, and other casual wear. Fortunately, plastisol inks are well-suited for cotton fabrics. When applied and cured correctly, plastisol inks can produce vibrant, long-lasting prints on cotton, making them a feasible option for fabric screen printing ink.
The Curing Process
The curing process is essential for ensuring the durability of plastisol inks on cotton fabrics. Plastisol inks require a specific temperature, usually around 320°F (160°C), to cure properly. During curing, the ink bonds with the cotton fibers, creating a durable print that can withstand multiple washes without fading or cracking. The precision in the curing process ensures that plastisol inks remain a viable option for fabric screen printing ink, particularly when durability is a priority.
Is Plastisol Ink Printing on Cotton Fabric Recommended?
While plastisol inks are compatible with cotton fabrics, whether they are recommended depends on the specific needs and goals of the project. Several factors influence the decision to use plastisol inks on cotton, including the desired print quality, environmental considerations, and the intended use of the garment.
Durability and Longevity
One of the primary reasons plastisol inks are recommended for cotton fabrics is their durability. Plastisol inks create a thick, robust layer on the surface of the fabric, making them resistant to wear and tear. This durability is particularly beneficial for garments that will be frequently washed, such as everyday T-shirts or uniforms. The long-lasting nature of plastisol inks makes them a reliable choice for fabric screen printing ink.
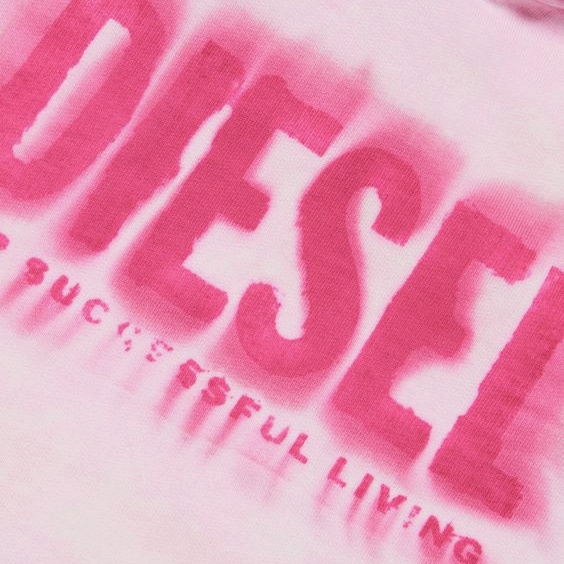
Print Quality and Aesthetics
Plastisol inks are known for their ability to produce vibrant, opaque colors, even on dark fabrics. The ink sits on top of the cotton fabric, allowing for bold and bright designs that stand out. This makes plastisol inks ideal for prints that require solid color coverage or intricate details. However, it’s important to note that the ink’s thickness can affect the feel of the fabric, a factor that may influence its recommendation for certain types of apparel.
Environmental Impact
While plastisol inks offer several advantages, their environmental impact is a consideration. Plastisol inks contain PVC and require chemical solvents for cleanup, raising environmental and health concerns. The curing process also consumes significant energy, which may not align with the goals of eco-conscious brands. For those prioritizing sustainability, alternative fabric screen printing ink options may be more appropriate.
Pros of Plastisol Ink Printing on Cotton Fabrics
Despite some concerns, plastisol inks offer numerous advantages when used on cotton fabrics. These benefits contribute to their widespread use in the screen printing industry.
High Opacity and Vibrancy
One of the most significant advantages of plastisol inks is their high opacity, which allows for vibrant and bold prints on both light and dark cotton fabrics. The ink’s opacity ensures that the fabric’s color does not show through the print, making it possible to achieve consistent and vivid colors. This characteristic is particularly important for designs that require bright and striking visuals.
Ease of Use
Plastisol inks are relatively easy to work with, making them a popular choice for both novice and experienced screen printers. The ink’s ability to stay wet on the screen allows for longer print runs without the risk of drying out, ensuring consistent results throughout the production process. This ease of use contributes to plastisol inks being a favored option for fabric screen printing ink.
Durability and Resistance
As mentioned earlier, plastisol inks are highly durable once cured. The ink forms a strong bond with the cotton fabric, making it resistant to fading, cracking, and peeling. This durability ensures that the printed design maintains its integrity over time, even after repeated washing and use. The robust nature of plastisol inks makes them ideal for garments that require long-lasting prints.
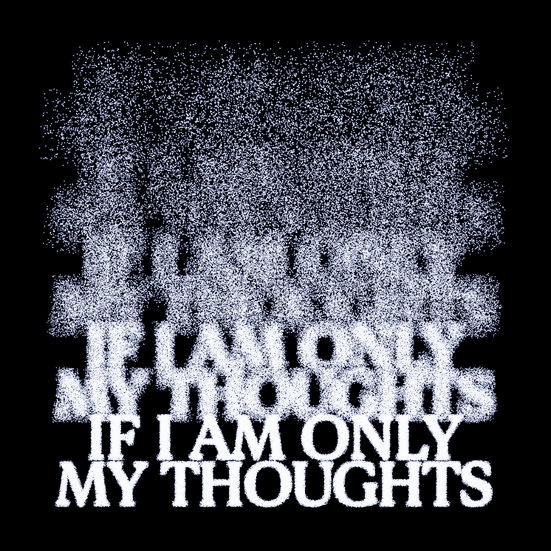
Versatility in Application
Plastisol inks are versatile and can be used on various fabrics, including cotton, polyester, and blends. This versatility allows printers to use the same ink for different garments, simplifying the printing process and reducing the need for multiple types of ink. The adaptability of plastisol inks makes them a practical choice for fabric screen printing ink.
Cons of Plastisol Ink Printing on Cotton Fabrics
While plastisol inks have many benefits, they also come with some drawbacks that may impact their suitability for certain projects.
Heavy Hand Feel
One of the main criticisms of plastisol inks is the “heavy hand” feel they create on the fabric. Since the ink sits on top of the cotton fibers rather than being absorbed, it can result in a thick, plastic-like texture. This can make the garment feel less breathable and less comfortable, especially in areas with large printed designs. For those seeking a softer feel, other fabric screen printing ink options may be more appropriate.
Environmental and Health Concerns
The environmental impact of plastisol inks is a significant consideration. The PVC content in plastisol inks and the use of chemical solvents during cleanup contribute to pollution and health risks. Additionally, the curing process requires a substantial amount of energy, further adding to the environmental footprint. These factors may discourage the use of plastisol inks for eco-friendly brands or projects.
Limited Breathability
The thick layer of plastisol ink on the fabric can reduce the breathability of the garment. This is particularly noticeable on large prints where the ink covers a significant portion of the cotton fabric. Reduced breathability can make the garment feel hotter and less comfortable, which may be a disadvantage for certain types of apparel, such as sportswear or summer clothing.
Potential for Cracking
While plastisol inks are generally durable, improper curing or excessive ink application can lead to cracking over time. This is more likely to occur on garments that are frequently stretched or subjected to heavy wear. Cracking not only affects the appearance of the print but can also reduce the garment’s overall longevity.
Better Printing Techniques for Cotton Fabrics
Given the pros and cons of plastisol inks, it’s worth exploring alternative printing techniques that may be better suited for cotton fabrics. Several options can provide high-quality results while addressing some of the concerns associated with plastisol inks.
Water-Based Inks
Water-based inks are an excellent alternative to plastisol inks, particularly for cotton fabrics. Unlike plastisol inks, water-based inks soak into the cotton fibers, resulting in a soft, breathable print that feels more natural to the touch. This makes water-based inks a popular choice for fashion and retail brands that prioritize comfort and sustainability.
Advantages of Water-Based Inks:
- Eco-Friendly: Water-based inks contain fewer harmful chemicals and emit fewer volatile organic compounds (VOCs) than plastisol inks. They are also easier to clean up, requiring only water instead of harsh solvents.
- Soft Hand Feel: The ink absorbs into the fabric, creating a print that is soft and breathable. This is particularly important for garments like T-shirts and hoodies, where comfort is key.
- Fine Detail: Water-based inks can produce fine details and sharp lines, making them ideal for intricate designs.
Disadvantages of Water-Based Inks:
- Opacity Challenges: Water-based inks are less opaque than plastisol inks, which can make achieving vibrant colors on dark fabrics more difficult. Multiple layers or an underbase may be needed to achieve the desired result.
- Longer Curing Time: Water-based inks take longer to dry and cure compared to plastisol inks, which can slow down production.
Discharge Printing
Discharge printing is another technique that works well on cotton fabrics. This method involves using a discharge ink to remove the dye from the fabric in the areas where the design will be printed. The result is a soft, natural-looking print that feels almost indistinguishable from the rest of the fabric.
Advantages of Discharge Printing:
- Soft Feel: Discharge printing results in a print that is virtually indistinguishable from the surrounding fabric, making it incredibly soft and comfortable to wear.
- Vibrant Colors: Discharge inks can produce vibrant colors on dark fabrics without the need for multiple layers or an underbase.
- Eco-Friendly: Discharge inks are water-based and contain fewer harmful chemicals than plastisol inks, making them a more environmentally friendly option.
Disadvantages of Discharge Printing:
- Fabric Compatibility: Discharge printing works best on 100% cotton fabrics. Blends or synthetic fibers may not discharge as effectively, resulting in inconsistent results.
- Limited Color Options: While discharge printing can produce vibrant colors, the color palette is more limited compared to plastisol or water-based inks.
Direct-to-Garment (DTG) Printing
Direct-to-garment (DTG) printing is a digital printing technique that works exceptionally well on cotton fabrics. DTG printers use water-based inks to print directly