Table of Contents
Screen printing is a widely used method for producing high-quality prints on various surfaces. Among the different inks available, black ink screen printing is a popular choice for its versatility, bold contrast, and ability to create striking designs. Whether you are a beginner or an experienced printer, understanding the techniques, benefits, and best practices for black ink screen printing can help you achieve professional results. This article explores everything you need to know about black ink screen printing, from its applications to expert tips for success.
Why Choose Black Ink for Screen Printing?
1. High Contrast and Visibility
One of the primary reasons for choosing black ink screen printing is its ability to create high-contrast prints, especially on lighter fabrics and materials. The deep, rich black ink stands out against a variety of backgrounds, making it an excellent choice for bold designs.
2. Versatility Across Materials
Black ink screen printing can be used on a wide range of materials, including cotton, polyester, paper, wood, and even glass. This versatility makes it a preferred choice for T-shirt printing, posters, packaging, and artistic prints.
3. Cost-Effectiveness
Black ink is one of the most economical inks available, making it an ideal option for bulk printing projects. Since it requires minimal layering compared to other colors, it also helps reduce ink consumption and costs.
4. Timeless and Classic Appeal
Black ink never goes out of style. It provides a classic, sophisticated look that appeals to a wide audience. Whether you are printing a simple logo or an intricate design, black ink screen printing ensures longevity and visual impact.
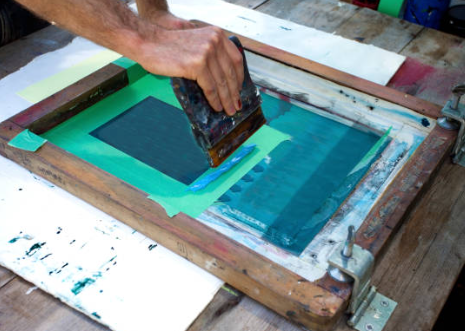
Essential Materials for Black Ink Screen Printing
To get started with black ink screen printing, you’ll need the following materials:
- Silk screen frame – A high-quality mesh screen for holding the stencil.
- Black screen printing ink – Choose between plastisol, water-based, or discharge ink based on your needs.
- Stencil or emulsion-coated screen – Used to transfer the design onto the printing surface.
- Squeegee – A tool for spreading the ink evenly over the screen.
- Heat press or curing unit – Essential for setting and curing the ink for durability.
- Printing surface – Such as T-shirts, posters, tote bags, or wood panels.
Step-by-Step Process of Black Ink Screen Printing
1. Preparing the Design
Create a high-resolution design using graphic design software like Adobe Illustrator or CorelDRAW. Ensure the design is in black and white, with clear and sharp edges for best results.
2. Creating the Stencil
Transfer the design onto a screen using photo emulsion. Coat the screen with emulsion, let it dry, then expose it to light with the design overlay. After exposure, rinse out the unexposed emulsion to reveal the stencil.
3. Setting Up the Screen
Position the screen over your printing surface and secure it in place to avoid shifting. Ensure proper alignment to achieve consistent prints.
4. Applying the Black Ink
Pour a generous amount of black ink screen printing ink at the top of the screen. Use a squeegee at a 45-degree angle to spread the ink evenly across the design in a single pass.
5. Curing the Print
Once the print is complete, cure the ink using a heat press or conveyor dryer. This step is crucial to ensure durability, wash resistance, and longevity of the print.
Types of Black Ink for Screen Printing
1. Plastisol Ink
Plastisol ink is the most commonly used ink for black ink screen printing due to its durability and vibrant finish. It does not dry unless cured, making it easy to work with.
2. Water-Based Ink
Water-based ink offers a softer feel and eco-friendly benefits. It absorbs into the fabric, making it ideal for lightweight garments and breathable prints.
3. Discharge Ink
Discharge ink removes the dye from dark-colored fabrics and replaces it with the desired black ink. This method produces soft, vintage-style prints with excellent detail.
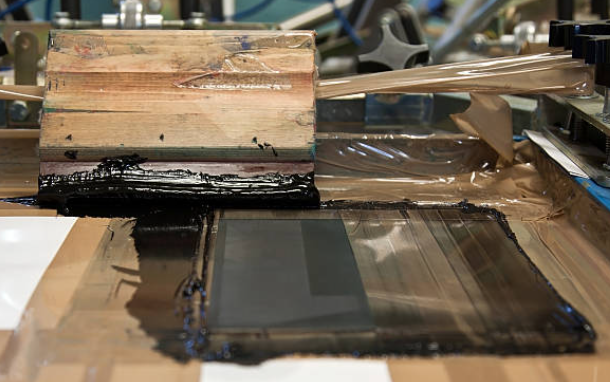
Best Practices for Achieving High-Quality Black Ink Prints
1. Choose the Right Mesh Count
The mesh count of your screen affects the ink application. A lower mesh count (80-110) allows more ink to pass through, ideal for bold prints. A higher mesh count (160-230) is better for fine details.
2. Use Proper Squeegee Pressure
Applying too much pressure can cause ink to bleed, while insufficient pressure may result in uneven prints. Use consistent, firm pressure to achieve sharp, clean lines.
3. Test Before Bulk Printing
Before running a full batch, test your prints on scrap material to ensure proper ink coverage, alignment, and curing.
4. Maintain Your Screens and Equipment
Regularly clean screens, squeegees, and printing stations to avoid ink buildup and contamination, which can affect print quality.
Common Mistakes and How to Avoid Them
1. Ink Bleeding
Ink bleeding occurs when too much ink is applied, causing edges to blur. Use a higher mesh count and controlled ink application to prevent this.
2. Incomplete Curing
If ink is not fully cured, prints may fade or wash out. Always use the recommended curing temperature (typically 320°F for plastisol ink) for the correct duration.
3. Misalignment of Prints
Ensure that the screen is firmly in place and double-check positioning before printing to avoid misaligned designs.
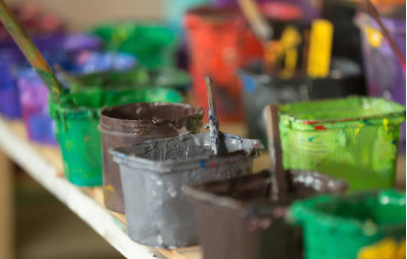
Applications of Black Ink Screen Printing
1. Apparel Printing
T-shirts, hoodies, and tote bags are the most common applications for black ink screen printing. The bold contrast of black ink creates eye-catching designs on both light and dark fabrics.
2. Poster and Art Prints
Black ink is widely used in artistic screen prints for posters and fine art. It enhances intricate designs and gives prints a timeless appeal.
3. Custom Merchandise and Branding
Businesses use black ink screen printing to create promotional merchandise, such as branded tote bags, stationery, and custom packaging.
4. Signage and Advertising
Bold black ink prints are perfect for signage and advertising materials that require high visibility and impact.
Advanced Techniques for Black Ink Screen Printing
1. Layering for Enhanced Depth
Use multiple layers of black ink to create depth and dimension in prints, particularly for textured surfaces.
2. Matte vs. Glossy Finishes
Experiment with different ink finishes to achieve the desired effect. Matte black ink provides a modern look, while glossy black ink enhances shine and contrast.
3. Combining Black Ink with Metallics
Pairing black ink with metallic inks such as gold or silver can create luxurious, high-end designs.
Conclusion
Black ink screen printing remains a staple in the printing industry for its versatility, affordability, and timeless appeal. By choosing the right materials, mastering printing techniques, and following best practices, you can produce high-quality, professional-grade prints with ease. Whether you’re creating custom apparel, art prints, or promotional merchandise, black ink screen printing offers endless creative possibilities.
Meta Description: Discover expert techniques for black ink screen printing. Learn the best inks, materials, and methods for bold, high-quality prints.