Screen printing is a popular method for creating vibrant designs on textiles. While plastisol inks have traditionally dominated the market, water-based screen print ink is gaining popularity for its eco-friendly nature, soft finish, and unique properties. In this article, we’ll explore why water-based inks are a great choice for screen printing, how to use them, and their benefits and drawbacks.
Why Should You Use Water-Based Screen Print Ink?
Water-based screen print ink is made with water as the primary solvent instead of harmful chemicals, making it a safer, more eco-friendly option. Below are some key reasons to choose water-based inks:
1. Eco-Friendly
Water-based inks are free from harmful chemicals like PVC and phthalates found in plastisol inks. This makes them a better choice for environmentally conscious printers.
2. Soft, Breathable Finish
Water-based inks soak into the fabric rather than sitting on top, giving the print a soft, breathable feel. This makes them especially popular for high-quality T-shirt printing.
3. Vibrant Prints
Water-based inks can produce vibrant, detailed designs, especially on light-colored fabrics like cotton. They are great for intricate designs requiring fine details.
Is Water-Based Screen Print Ink Good for Screen Printing?
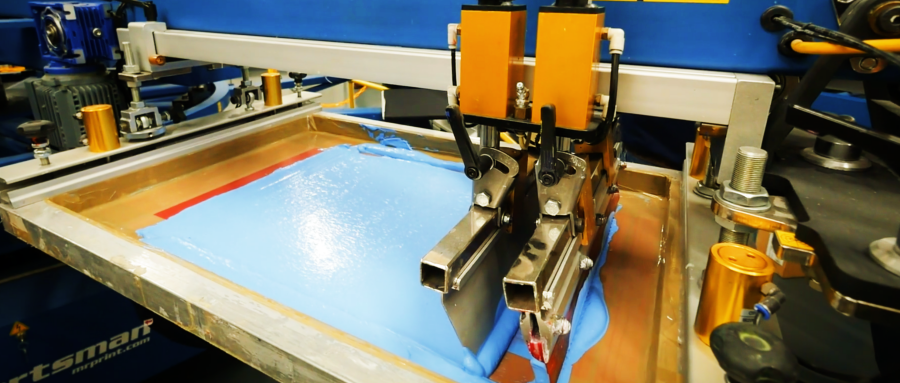
Water-based screen print ink offers several advantages but also comes with some challenges.
Pros:
- Soft Finish: Water-based prints are soft to the touch and comfortable to wear.
- Eco-Friendly: They are more environmentally friendly than plastisol inks.
- Detail-Oriented: They are great for producing fine details and sharp lines in designs.
Cons:
- Longer Drying Times: Water-based inks take longer to dry compared to plastisol inks.
- Requires Proper Curing: You need a heat source like a flash dryer or conveyor dryer to properly cure the ink.
- Limited on Dark Fabrics: They work best on light fabrics; dark fabrics often require an underbase.
Despite these challenges, water-based ink is ideal for eco-conscious printers seeking vibrant and soft prints, especially on light fabrics.
How to Screen Print Water-Based Ink on T-Shirts
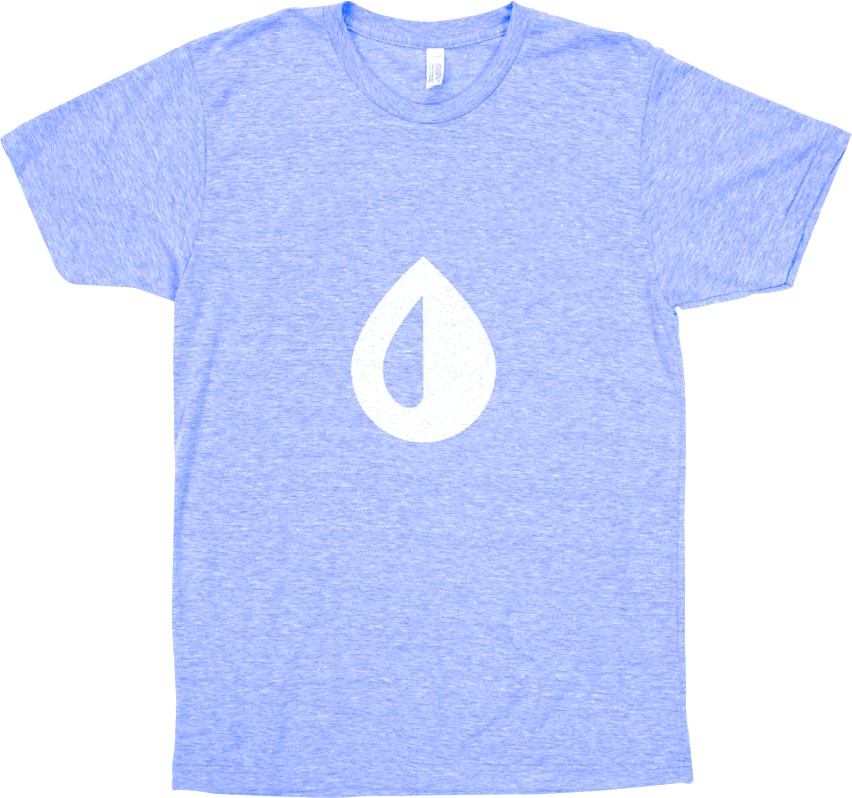
Using water-based ink for T-shirt printing is a slightly different process than using plastisol inks. Here’s how to get started:
1. Prepare the Screen
Make sure your screen is clean and coated with emulsion suitable for water-based ink.
2. Mix the Ink
Water-based inks tend to be thinner, so you might need to mix in a thickening agent if necessary.
3. Print the Design
Load the ink onto the screen, then use a squeegee to press it through onto the T-shirt.
4. Cure the Ink
Curing water-based ink properly is crucial. Use a conveyor dryer, flash dryer, or heat press to cure the ink at 320-330°F (160-165°C) to ensure a durable print.
Different Ways to Cure Water-Based Screen Print Ink
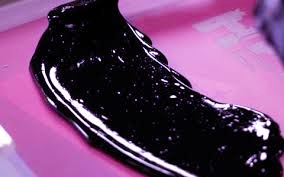
Curing water-based ink is essential to ensure its longevity. There are several ways to cure the ink:
- Conveyor Dryer: Best for larger print runs, it ensures even curing.
- Flash Dryer: Quick and effective for smaller batches.
- Heat Press: A good option for smaller projects or DIY printing.
What Are the Disadvantages of Water-Based Screen Print Ink?
While water-based inks have many benefits, they also have some downsides:
- Longer Drying Time: Water-based inks take longer to dry than plastisol.
- Requires Proper Curing: Inadequate curing can result in fading or cracking.
- Not Ideal for Dark Fabrics: Water-based inks are not as effective on dark-colored fabrics unless an underbase is used.
How Long Does Water-Based Screen Print Ink Last?
Properly cured water-based screen print ink is durable and can last for years. On cotton fabrics, the print can last as long as plastisol prints, provided you follow proper care instructions like washing in cold water and avoiding high heat in the dryer.
How to Make Water-Based Screen Print Ink?
You can make your own water-based ink at home. Here’s a simple guide:
Materials:
- Water-based pigment or colorant
- Water-based binder
- Distilled water
- Thickener (optional)
Instructions:
- Mix Binder and Pigment: Combine the water-based binder with your chosen pigment.
- Add Water: Gradually add distilled water to achieve your desired consistency.
- Add Thickener (Optional): Add thickener for a more viscous ink.
- Test: Test the ink on fabric to ensure the consistency and color meet your needs.
Conclusion
Water-based screen print ink offers an eco-friendly, soft, and vibrant alternative to traditional plastisol inks. While it has some challenges, such as slower drying times and the need for proper curing, it can produce high-quality prints when used correctly. Whether you’re an eco-conscious printer or looking for a softer, more breathable print, water-based ink is a great option. By understanding how to use and cure water-based ink, you can create durable, eye-catching prints that stand the test of time.