Polyester Screen Printing Ink——Silk Screen Printing Guide
Polyester is a synthetic fabric known for its durability, wrinkle resistance, and smooth texture. However, it also has characteristics that can complicate screen printing, including,Low Dye Stability: The fabric dyes can migrate, especially when exposed to high heat.Low Ink Absorption: Polyester does not absorb ink as well as natural fibers, leading to potential adhesion issues.High Heat Sensitivity: Polyester can shrink or melt at high temperatures, impacting the curing process for inks.
How To Achieve The Best Results When Use Polyester Screen Printing Ink
Screen Printing on polyester comes with unique challenges due to the material’s synthetic fibers, which have a higher risk of issues like dye migration and inadequate ink adhesion.
Preparation
- Material preparation:Ensure that all materials, including fabrics, inks, scrapers, screens, curing equipment, etc., are neatly arranged in the work area for easy operation. Pay particular attention to your cotton ink selection.
- Fabric placement:Stretch the cotton fabric flat to ensure there are no wrinkles and secure it to the printing table to ensure an even printing effect when applying ink and cotton.
- Screen preparation:Make sure the screen is clean and free of any old residual ink. Choose the appropriate number of grids according to the design and printing effect requirements to ensure high accuracy and clarity.
Polyester Screen Printing Ink Operation Process
Base Layer Printing for Polyester Screen Printing Ink (Step 1)
Ink Preparation: Select a transparent Plastisol ink specifically designed for polyester screen printing. Pour an appropriate amount of ink into the ink reservoir of the screen, adjusting for the polyester fabric type and size of the design area. This ensures optimal adhesion to polyester fabric, which can otherwise be challenging due to its low ink absorption properties.
Screen Printing Process: Using a rubber squeegee, apply the transparent ink evenly onto the polyester fabric. Move the squeegee at a 45-degree angle to ensure the ink penetrates the screen and covers the design area completely. For best results, ensure even pressure to achieve consistent coverage on polyester fabric.
Base Coat Curing: After printing, the polyester fabric should be placed in a drying device (such as a conveyor dryer or drying box) for preliminary curing. The temperature is generally set to 160°C, with a curing time typically ranging from 60 to 90 seconds, depending on the ink thickness. This step ensures the base layer dries thoroughly, which is essential for a stable foundation layer on polyester.
Anti-Sublimation Printing For Polyester Fabric (Step 2)
Polyester Screen Printing Ink Preparation: Use HF-8502 anti-sublimation ink, stirring it thoroughly to prevent dye migration that is common in polyester screen printing. Anti-sublimation inks are crucial for polyester fabric, as they effectively prevent color bleeding from the fabric to the design, resulting in a high-quality print.
Polyester Screen Printing Process: Pour the anti-sublimation ink into the ink reservoir of the screen and use a rubber squeegee to apply it over the polyester fabric in high-density. This ink layer acts as a color-blocking barrier, protecting the design from unwanted color shifts that can occur on polyester fabrics.
Final Curing: Once the print is complete, cure the polyester fabric in a drying device. The optimal temperature is set at 170°C, with a curing time between 90 and 120 seconds. This process ensures the anti-sublimation layer sets fully, which is essential for polyester screen printing.
White Color Printing On Polyester Fabric (Step 3)
Polyester Screen Printing Ink Preparation: Choose a high-quality white Plastisol ink, as it is one of the best screen printing ink choices for polyester. Pour an adequate amount into the screen’s ink reservoir, matching the polyester fabric type and design size. For best results, select a Plastisol ink specifically formulated for polyester screen printing, as it enhances adhesion and minimizes dye migration risks.
Screen Printing Process: With a rubber squeegee, evenly apply the white ink onto the polyester fabric. Move the squeegee at a 45-degree angle to ensure the ink penetrates the screen and fully covers the required design areas, providing excellent contrast on polyester surfaces.
Final Curing: After the design is applied, place the polyester fabric in a drying device for final curing. Maintain the temperature at 160°C for 90 to 120 seconds to ensure the ink completely sets, yielding a vibrant and durable finish. Using the best screen printing ink for polyester ensures longevity and vibrant results.
Key Tips for Polyester Screen Printing Ink
- For achieving the best results on polyester fabric, it’s essential to use specialized screen printing inks like low-bleed or anti-sublimation Plastisol inks that are ideal for polyester. Polyester screen printing ink designed specifically for this fabric type will provide excellent adhesion, vibrant color, and resistance to dye migration, ensuring your design remains sharp and true to color.
Quality Inspection and Closing
- Quality Check:After taking the fabric out of the drying equipment, check the printing quality of the pattern to confirm whether there are any problems such as missing printing, fading, or uneven color.
- Modification:If there are a few areas that do not achieve the desired effect, they can be appropriately repaired locally and dried again.
- Storage:When finished, place the printed fabric in a cool and ventilated place to ensure the best effect after the pattern is completely dry.
High-Density Printing Process
- Thick plate printing is characterized by a specific thickness of the printed material, which can be pre-adjusted to a specific three-dimensional effect.
Precautions
- Test Print:Always do a test print on scrap fabric to adjust color and technique when working with ink and cotton.
- Accurate registration:Ensure precise registration when printing multi-color designs.
- Store:Store finished products properly to prevent cotton ink from smudging or fading.
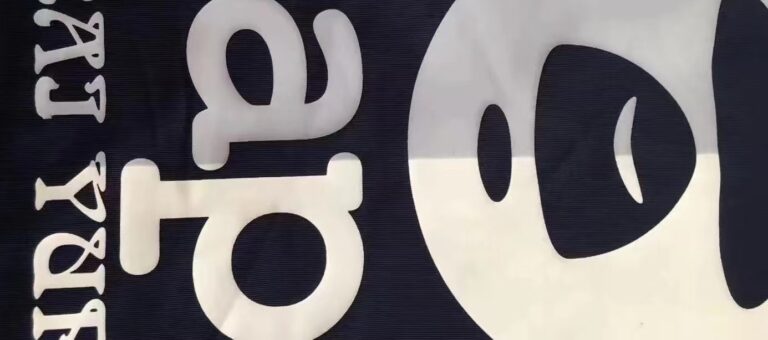
Polyester Screen Printing Ink
Silk screen printing on polyester presents its own set of challenges due to the unique characteristics of the fabric. Here are some common issues encountered when printing on polyester, along with possible solutions:
1. Dye Migration
- Problem: Polyester fabrics can release dyes when exposed to high temperatures during the curing process, leading to color changes or bleeding into the printed ink.
Polyester Screen Printing Ink Adhesion Issues
- Problem: Inks may not adhere well to polyester surfaces, especially if the fabric has a low surface energy.
Temperature Sensitivity
- Problem: Polyester is sensitive to high temperatures, which can lead to scorching, melting, or shrinking of the fabric during the curing process.
Print Durability and Flexibility
- Problem: Printed designs can crack or peel due to the inherent flexibility of polyester and the rigidity of some inks.
Inconsistent Ink Coverage
- Problem: The smooth, shiny surface of polyester can cause issues with ink coverage, leading to patchy or uneven prints.
Ghosting:
- Problem: Ghosting occurs when the dye from the fabric bleeds into the print, creating a blurry effect around the edges.
Static and Lint Issues
- Problem: Polyester fabrics can attract lint and static, which may interfere with the printing process and lead to imperfections.
Fading and Wash Fastness
- Problem: Some inks may fade quickly when printed on polyester, especially if they are not specifically formulated for this type of fabric.
Difficulty with Fine Details
- Problem: The slick surface of polyester can make it challenging to print intricate designs with fine details.
By understanding these common issues and implementing the suggested solutions, you can improve the quality and durability of screen prints on polyester fabrics.
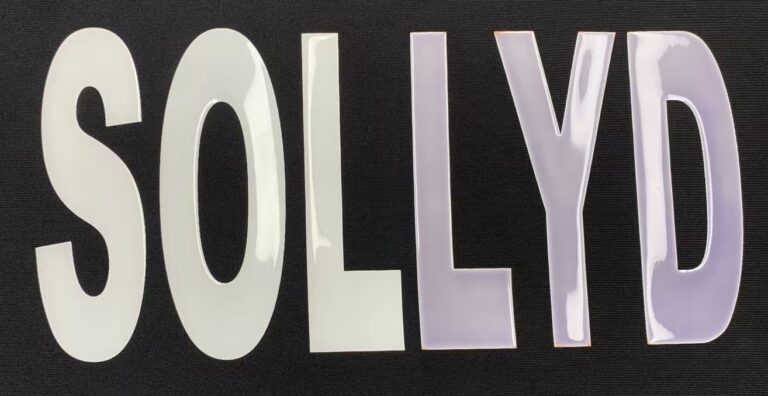
Optimized Guide for Polyester Fabric Screen Printing with Polyester Screen Printing Ink
Screen printing on polyester fabric can present challenges like dye migration, adhesion issues, and durability concerns. By following these optimized techniques, you can achieve vibrant, high-quality results using the best screen printing ink for polyester—Plastisol ink specifically formulated for polyester screen printing. Here’s a comprehensive approach to overcoming common issues and achieving lasting prints on polyester fabric.
1. Preventing Dye Migration
Use Anti-Migration Plastisol Ink: The HF-8502 anti-migration Plastisol ink is specifically designed to prevent dye migration in polyester fabrics. This ink effectively blocks dye from shifting during high-temperature curing, helping maintain color vibrancy and pattern clarity on polyester fabric.
Print an Isolation Underbase: For darker or high-risk polyester fabrics, start with a white underbase layer before applying other colors. This underbase isolates the design, blocking dye migration and preserving the final colors.
Improving Ink Adhesion
Choose Specialized Ink: Use polyester screen printing ink specifically formulated for polyester fabric, which provides superior adhesion to synthetic surfaces. These inks are optimized to bond effectively with the smooth, non-porous polyester material.
Surface Treatment: Before printing, treat the polyester fabric with a heat press or spray-on adhesion promoter to enhance the surface energy. This step significantly improves ink adherence, especially for the best screen printing ink for polyester applications.
Controlling Curing Temperature
Use Low-Temperature Curing Ink: Opt for low-temperature curing Plastisol ink to prevent the polyester fabric from melting or shrinking due to excessive heat. Low-temperature curing ensures a strong bond without risking fabric distortion.
Monitor the Curing Process: Ensure appropriate curing temperature and duration, generally setting the heat to 160°C (320°F) for 1-2 minutes. This careful control ensures that the polyester screen printing ink fully cures without damaging the polyester fabric
Enhancing Durability and Flexibility
Select Elastic Inks: Use high-flexibility Plastisol ink, which stretches with the polyester fabric and minimizes cracking or peeling over time. The best screen printing ink for polyester is not only adhesive but also flexible, which extends the print’s durability.
Thorough Curing: Ensure inks are fully cured at the appropriate temperature. Full curing increases the print’s resilience against wear and tear, ensuring long-lasting results on polyester fabric.
Improving Ink Coverage
Choose High-Coverage Ink: High-opacity Plastisol inks are ideal for achieving uniform, saturated colors on polyester fabric. These inks provide superior coverage even on darker materials.
Multiple Prints for Detailed Designs: For intricate designs, consider multiple passes to ensure full coverage with no gaps in the print. Layering enhances the overall appearance and ensures that fine details stand out on polyester.
Avoiding Ghosting:
Ensure Complete Curing: During curing, verify that the ink fully dries at the correct temperature and time. This step prevents ghosting or shadow effects caused by incomplete curing, which can occur frequently on polyester fabric.
Apply Underbase Ink: For designs on polyester, consider using an underbase ink layer to isolate colors and prevent dye interference from the fabric itself.
Addressing Static and Lint Issues
Use Anti-Static Tools: Employ anti-static equipment during printing to reduce static interference, which can disrupt print quality on polyester fabric.
Clean the Fabric: Ensure that the polyester fabric is free from dust and lint prior to printing. Using tape to remove any surface particles will improve the ink’s adhesion and overall print quality
Improving Wash Durability
Select Wash-Resistant Ink: Choose high-durability, wash-resistant Plastisol ink designed for polyester. This ink retains color and pattern quality even after multiple washes, making it the best screen printing ink for polyester garments.
Provide Washing Instructions: Advise customers to wash printed polyester garments inside out, in cold water, with mild detergent. Following these guidelines helps maintain the print’s longevity and appearance.
Enhancing Detail Clarity
Use High-Mesh Screens: Opt for screens with a mesh count of 160 or higher, paired with high-viscosity Plastisol ink. This setup helps achieve detailed, crisp prints on polyester fabric.
Adjust Squeegee Pressure: Test and adjust squeegee pressure during printing to improve detail clarity. Proper pressure helps ensure that fine lines and intricate elements remain sharp on the polyester material.
By implementing these techniques with the right polyester screen printing ink, you can effectively overcome the challenges of screen printing on polyester fabric. Choosing the best screen printing ink for polyester ensures vivid, durable, and professional-quality results.