The Versatility and Appeal of Puff Plastisol Ink
Puff Plastisol Ink
Puff Plastisol Ink is a unique type of screen printing ink that expands when exposed to heat, giving a raised or “puffed” texture to printed designs. This ink is especially popular for adding dimension and depth to garments and is widely used in fashion and promotional items.As a global Screen Printing Ink Manufacturer and Factory of superior Screen Printing Ink, Ecoprinting brings an answer focused on productivity, consistency, and environmental duty.
Key Features of Puff Plastisol Ink:
- 3D Textured Finish: Creates a raised, dimensional effect on the printed surface.
- Soft and Flexible Feel: Despite the raised texture, puff ink remains soft and comfortable to wear.
- Vibrant Colors: Puff inks maintain bold and bright colors, enhancing the visual appeal of prints.
- Durable and Long-lasting: The cured prints are resistant to washing and general wear and tear, ensuring longevity.
- Easy to Use: Works similarly to regular Plastisol inks with additional heat to achieve the puff effect.
- Customizable Expansion: The puff height can be controlled by adjusting the ink layer thickness or adding puff additives.
Benefits:
- Visual and Tactile Appeal: Puff inks create prints that not only look great but also offer a unique texture that stands out.
- Versatility: Puff ink can be used for a variety of garment types, including t-shirts, hoodies, and fashion accessories.
- Compatible with Various Mesh Counts: You can use different mesh screens to achieve different levels of detail and puff effect.
Technical Details:
- Curing Temperature: Typically cured at 320°F (160°C), but curing time and temperature may vary based on the ink and garment.
- Surface Drying: Puff inks tend to air dry quickly on the surface before being cured.
- Recommended Mesh: 60 to 110 mesh count is ideal for puff inks, depending on the desired puff effect and detail.
- Squeegee Recommendations: A medium to hard squeegee is often recommended for even ink distribution.
Application and Usage:
- Fabrics: Best suited for cotton and cotton blends, though can be used on some synthetic fabrics with proper testing.
- Printing Techniques: Often printed as a final layer or combined with regular Plastisol inks to achieve contrasting textures.
- Creative Uses: Puff ink is popular for logos, bold typography, and designs requiring a unique 3D look. It’s frequently used in sports apparel, streetwear, and children’s clothing for its playful texture.
Achieving the Best Results:
- For maximum puff effect, it’s important to test your printing and curing process on the specific fabric being used. The thickness of the ink layer and the curing time directly affect the expansion of the ink, so adjustments may be necessary to perfect the design.
This ink offers a creative, eye-catching alternative to flat printing, allowing for unique design possibilities.
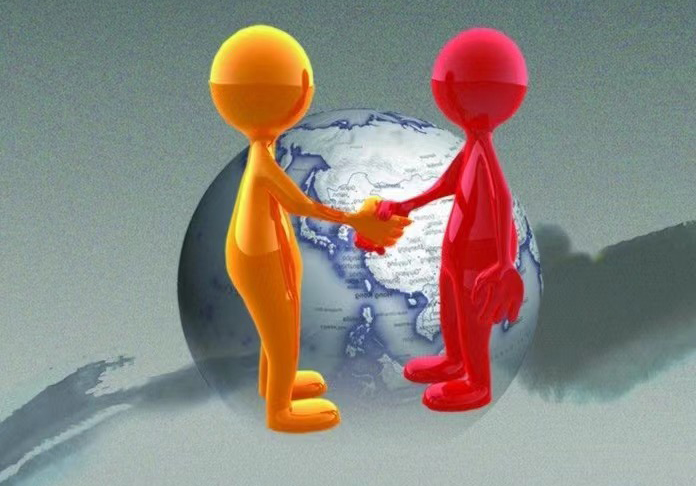
Demand communication
1. You first need to clarify your specific requirements for Plastisol Ink, including expectations in terms of color, gloss, viscosity, durability, etc.
2. Communicate with the ink supplier or custom manufacturer and elaborate on your application scenario, such as whether it is used for printing textiles, paper or other materials. Different application scenarios may require inks with different characteristics.
→Contact Us
Samples provided
1. The supplier or manufacturer will prepare some preliminary Plastisol Ink samples based on the requirements you provide.
2. You test and evaluate the samples to check color accuracy, printing effect, drying time, adhesion to the substrate, etc.
→Contact Us
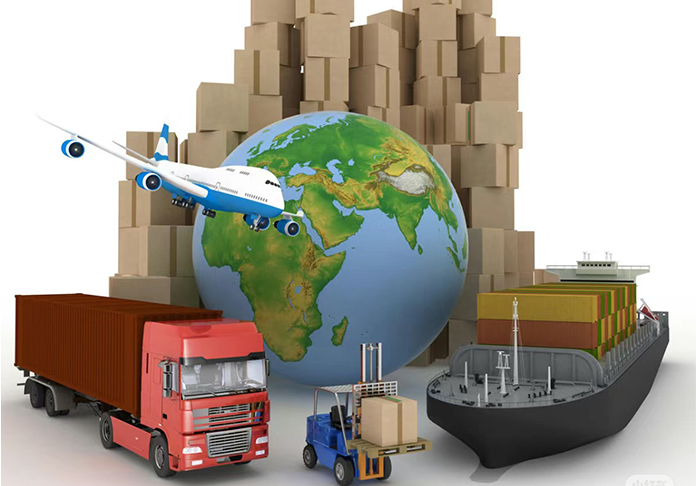
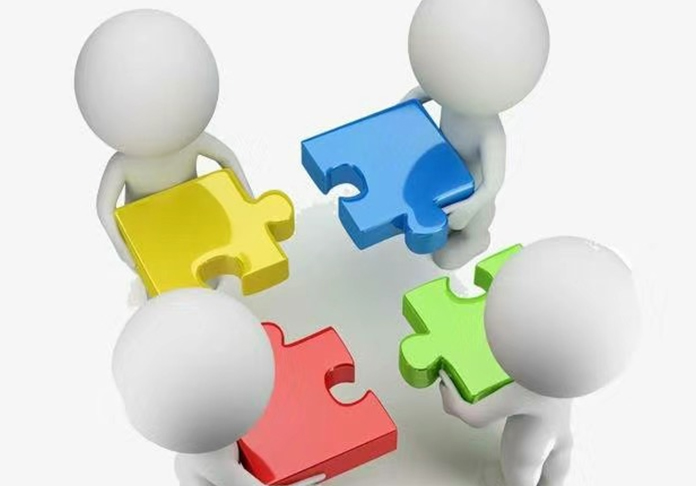
Adjust and Confirm
1. If you are not satisfied with the sample, please communicate with the supplier in time and put forward specific suggestions for adjustment.
2. The supplier will adjust the ink formula according to your feedback and provide samples for your confirmation again.
3. After repeated adjustments and confirmations, you will be completely satisfied with the performance and quality of Plastisol Ink.
→Contact Us
Signing a contract
1. Once the final ink formula and quality standards are determined, both parties need to sign a custom contract.
2. The contract should clearly state the ink specifications, quantity, price, delivery time, quality assurance and other terms.
→Contact Us
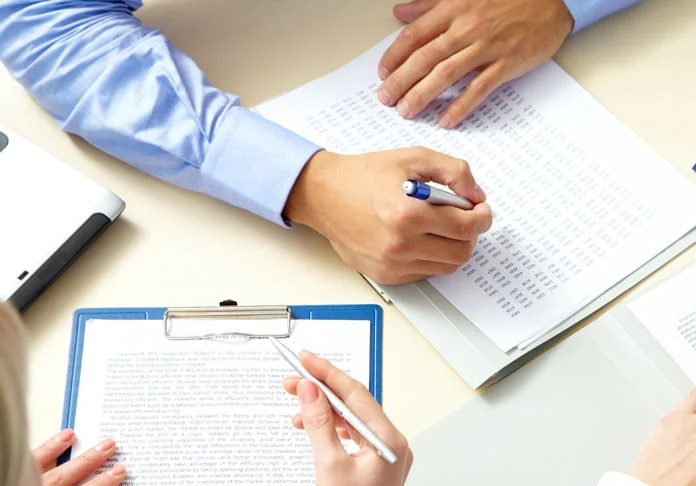
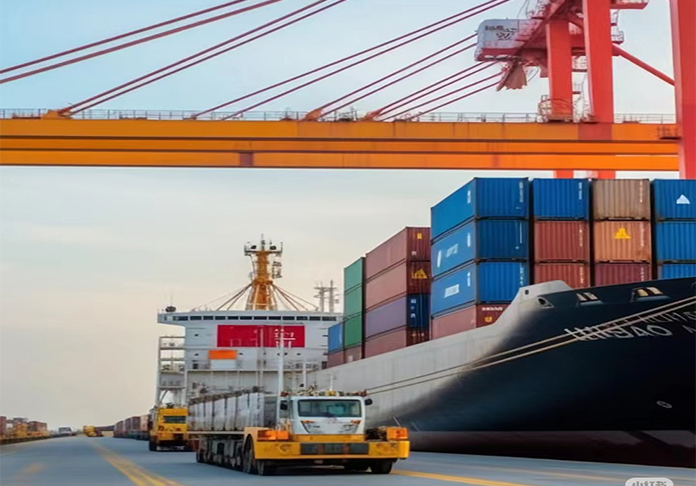
Production & Delivery
1. The supplier produces Plastisol Ink in accordance with the contract requirements.
2. During the production process, quality inspections may be carried out to ensure that the ink meets the standards agreed by both parties.
3. The customized Plastisol Ink will be delivered to you on time, and relevant quality inspection reports and instructions for use will be provided.
→Contact Us
After-sales service
1. If you encounter any problems during use, you can always contact the supplier for technical support.
2. The supplier may make further optimizations and improvements based on your feedback to improve the quality and performance of the product.
→Contact Us
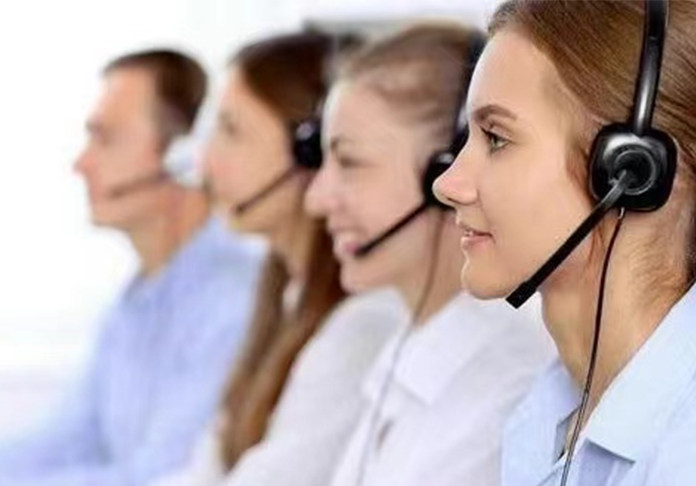
Plastisol Ink Production Process
Plastisol Ink After-Sales Support
Our after-sales support is one of the cornerstones of our business model. We are fully committed to providing first-class after-sales service to ensure your satisfaction.
Through our comprehensive after-sales support, we aim to sell you our products and build a lasting relationship based on trust and satisfaction. We are here to support you and ensure you get the most out of your investment in our Plastisol Inks.
Technical consultation and guidance
If you encounter any problems when using Plastisol Ink, such as poor printing results, abnormal ink performance, etc., the supplier's technical team can provide you with professional consultation and guidance.
Training
For customers who use Plastisol Ink for the first time, the supplier may provide training on how to use it. The training content includes the correct method of mixing ink, operating skills of printing equipment, and precautions for printing process.
Product optimization and improvement
According to customer feedback and market demand, suppliers will continue to optimize and improve Plastisol Ink, for example, improving the environmental performance of ink, enhancing color stability, and improving the rheology of ink.
Customer complaint handling
If a customer is not satisfied with Plastisol Ink's after-sales service or has other complaints about the product, the supplier will have a dedicated customer service team to handle it.
Frequently Asked Questions about Plastisol Inks
Plastisol Ink is suitable for a variety of fabrics, including 100% cotton, cotton/poly blends, polyester, dark and light colored fabrics, denim, etc. However, please note that it may not be suitable for some special fabrics, such as plastic, metal, glass, etc. and waterproof nylon fabrics. The reason why it can be used on these common fabrics is that these fabrics can withstand high temperatures of 150°C to 180°C and are breathable, allowing the ink to penetrate. For example, on pure cotton fabrics, Plastisol Ink can produce clear, bright and long-lasting prints; on polyester-cotton blends, it can also adhere and color well.
There may be many reasons why Plastisol Ink has poor fastness during operation. First, it may be that the ink is not properly selected, has poor compatibility with the printing material, or the ink has expired and has become ineffective. For example, ink that is not suitable for a specific fabric material is used, or ink that has been stored for too long and has degraded performance is used. Secondly, the ink layer is too thin and the adhesive is damaged, which can also lead to poor fastness. This may be due to improper adjustment of the viscosity of the ink during printing, or errors in the operation process. In addition, insufficient heating and slow printing drying speed will also affect the fastness. If the heat and air supply are insufficient, the ink cannot be fully cured and it is difficult to achieve the desired fastness. In addition, when overprinting, the lower layer of ink is not completely dry and is covered by the new ink layer, forming a false dry, which will also affect the fastness. In addition, dirt on the surface of the printing material, too thick a printing ink layer, too much ink, too high a viscosity, which causes the ink to become brittle after a long drying period, and the tension of the printing material surface is lower than the tension of the ink, etc., may all lead to poor fastness of Plastisol Ink.
The storage of Plastisol Ink requires the following conditions. Generally speaking, it should be placed in a cool, dry place away from direct sunlight and high temperature environments. The storage temperature should not be too high or too low to prevent changes in the ink’s performance. During storage, ensure that the container is well sealed to prevent the ink from coming into contact with the air, and to prevent moisture and impurities in the air from entering the ink and affecting its quality. For example, if the ink is exposed to the air for a long time, the solvent in it may evaporate, causing the ink to thicken or even dry, affecting the use effect. At the same time, the ink should be used according to its shelf life. Expired ink may have problems such as performance degradation and poor curing.
The printing process of Plastisol Ink is relatively complicated. First of all, the selection of screen is very important. Generally, 100-120 mesh thick plate is selected. Use a screen printing hard square knife to scrape at 75 degrees, and use transparent ink to prime 1-2 times. When printing for the first time, scrape 4-6 times with force. For color ink, print 2-3 times (or directly print color ink 3-4 times without primer). After printing, heat treatment is carried out, and it is baked at 150-180 degrees for 1-3 minutes. During the printing process, the ink layer needs to be blown to dry with a hot air gun before each reprint to prevent it from sticking to the screen. For example, when printing a pattern with a three-dimensional effect, it is necessary to control the thickness of the ink and the strength of the scraping to achieve the ideal three-dimensional effect.
Plastisol Ink has many effects and characteristics. First, it is paste-like and thixotropic. It is thicker when left standing, and becomes thinner when stirred. The temperature affects the viscosity. In summer, the viscosity is low and the ink is thinner, while in winter, it is the opposite. Second, it can print a variety of special effects, such as pulping, pulping and hot stamping, toothbrush particles, rounded corners, right angles, brown color, gel, sticky beads, hot stamping, stone, non-slip, bark, etc. It is suitable for manual printing and mechanical printing of textile fabrics, leather, denim, shoes, etc. Third, it will not dry at room temperature. It needs to be heated to 150°C – 180°C and baked for 1 – 3 minutes to completely solidify the ink. After plasticization, the adhesion firmness is above level 5 for wet washing and above level 4 for dry rubbing. Fourth, it can be combined with various textile decorative auxiliary materials such as glass beads, plastic beads, plastic sheets, metal glitter sheets, light reflective materials, etc. for special effect printing, which is low cost and completely environmentally friendly. For example, in clothing printing, Plastisol Ink can be used to print patterns with three-dimensional effects and rich colors, increasing the beauty and uniqueness of clothing.
Cause analysis:
One of the main reasons is that the thermosetting ink is not fully baked. If the baking temperature is not high enough or the baking time is insufficient, the ink cannot be fully cured, which will cause the slurry layer to lack elasticity and even appear powdery.
The quality problem of the ink itself may also cause this situation. For example, the improper proportion of resin components in the ink and the failure of additives may affect the curing effect and elasticity of the ink.
During use, if the ink is over-diluted, the slurry layer may also lose elasticity and appear powdery. Excessive dilution will destroy the composition ratio of the ink and reduce its performance.
Solution:
Ensure the correct baking temperature and time. According to the instructions for use of the ink, adjust the temperature and time of the baking equipment so that the ink can be fully cured. Generally speaking, increasing the baking temperature or extending the baking time can improve this situation.
Check the quality of the ink. If you suspect that there is a problem with the quality of the ink, you can contact the supplier for testing or replacement.
Avoid over-diluting the ink. When using diluent, strictly follow the proportion to ensure the performance of the ink.
Cause analysis:
One of the common reasons is that the ink layer is heated to a temperature of more than 230℃. Excessive temperature will change the composition of the ink and produce gas, which will cause the ink layer to bubble.
Adding solvent diluents to the ink may also cause bubbling. Solvent diluents may react with the components in the ink to produce bubbles.
Adding other water-based substances to the ink may also cause bubbling. Water-based substances are incompatible with oil-based inks and are prone to chemical reactions to produce bubbles.
Solution:
Control the baking temperature. Make sure that the heating temperature of the ink layer is within the appropriate range, generally not exceeding 230℃. A thermometer or temperature control equipment can be used to monitor and adjust the baking temperature.
Use a special diluent for thermosetting inks instead. Avoid using solvent diluents and choose a special diluent suitable for thermosetting inks to reduce the risk of bubbling.
Do not add water-based substances. When using thermosetting inks, make sure that water-based substances are not mixed in to avoid adverse reactions.
Cause analysis:
The surface of the slurry layer is not completely dry, which is one of the main reasons. If the baking time is insufficient or the temperature is not high enough, the surface of the slurry layer may not be completely dry, and anti-sticking may occur.
Adding too much diluent may also cause surface anti-sticking. Too much diluent will slow down the drying speed of the ink and increase the possibility of surface anti-sticking.
Slurry that is too thin may also cause surface anti-sticking. Too thin slurry will affect the curing effect of the ink and make the surface prone to anti-sticking.
Solution:
Appropriately increase the baking temperature or extend the baking time on the original basis to ensure that the surface of the slurry layer is completely dry. You can judge whether it is dry by observing the color change of the ink layer and touching the dryness of the surface.
Control the amount of diluent. According to the instructions for use of the ink, reasonably control the amount of diluent added, generally not more than 8%.
The thickening powder specially used for heat-curing ink can be used to increase the consistency of the ink. Properly increasing the consistency of the ink can improve its curing effect and reduce the situation of surface anti-sticking.
Plastisol Ink Cleaning and Maintenance
The following are the cleaning and maintenance methods for Plastisol Ink:
1. Cleaning
Printing equipment cleaning
After each use of Plastisol Ink, the printing equipment should be cleaned immediately to prevent the ink from drying on the equipment and affecting the next use. For screen printing machines, special screen cleaning agents or thinners can be used to clean the ink from the screen, scraper, ink pad and other parts.
When cleaning the screen, you can first use a soft brush to gently brush off most of the ink on the screen, then spray it with a cleaning agent, and finally rinse it with clean water and dry it. Be careful not to scratch the screen with a hard brush or sharp objects to avoid damaging the mesh.
The scraper and ink pad can be wiped with a wet cloth dipped in a cleaning agent to remove the remaining ink. For some difficult-to-clean parts, tools such as toothpicks or fine needles can be used to assist in cleaning.
Cleaning the workplace
Clean up the ink stains around the workplace in a timely manner to prevent the ink from polluting the environment. You can use a rag or mop dipped in a cleaning agent to wipe and mop the floor.
Ink dripping on the ground should be cleaned as soon as possible to avoid it being difficult to remove after drying. You can sprinkle some sawdust or sand first, absorb the ink and then clean it.
2. Maintenance
Ink storage
Plastisol Ink should be stored in a cool, dry, well-ventilated place, away from direct sunlight and high temperature environment. The storage temperature is generally between 5℃ and 30℃.
The ink container should be well sealed to prevent air from entering and causing the ink to dry or deteriorate. During storage, the state of the ink should be checked regularly, and any abnormalities should be handled in time.
Equipment maintenance
Perform regular maintenance on printing equipment to ensure the normal operation of the equipment. For example, check the wear of the scraper and replace the severely worn scraper in time; check the tension of the screen and adjust it in time if it is loose.
Lubricate the transmission parts, guide rails, etc. of the equipment to reduce wear and extend the service life of the equipment.
Safety precautions
During cleaning and maintenance, appropriate protective equipment such as gloves, masks, goggles, etc. should be worn to avoid ink contact with the skin and respiratory tract.
Cleaning agents and diluents are generally volatile and flammable, and should be kept away from fire and heat sources and used in a well-ventilated environment.
Related products
-
Specialty Inks
Glow In The Dark Orange Plastisol Ink
-
Specialty Inks
Fluorescent Screen Printing Plastisol Ink
-
Specialty Inks
Foil Plastisol Ink
-
Specialty Inks
Anti-Migation Plastisol ink