Conclusion
So, can you mix screen printing inks? Absolutely! Mixing compatible inks is a great way to create custom colors, textures, and special effects for your prints. However, it’s essential to stick to inks that are chemically compatible and to follow best practices for measuring, mixing, and testing your inks before moving into full production.
Whether you’re working with plastisol screen printing ink, water-based screen printing ink, or specialty inks like glow in the dark screen printing ink or reflective screen printing ink, mixing inks allows you to push the boundaries of creativity and achieve truly unique prints. Just remember to document your mixes for consistency and always test your designs before printing large quantities.
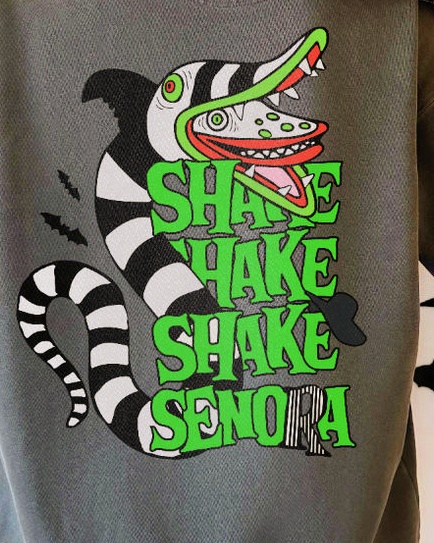
Can You Mix Screen Printing Inks
In the world of screen printing, achieving unique colors, textures, and finishes often involves experimenting with different types of screen printing inks. But one common question that printers often ask is: can you mix screen printing inks to create custom effects? The short answer is yes, but there are important factors to consider before diving into the mixing process.
In this article, we will explore the ins and outs of mixing screen printing inks, including the different types of inks available, tips for successful mixing, and potential pitfalls to avoid. Whether you’re looking to combine water-based screen printing ink, plastisol screen printing ink, or other specialty inks like puff ink for screen printing, this guide will help you navigate the process.
Understanding Different Types of Screen Printing Inks
Before you start mixing, it’s essential to understand the different types of screen printing inks and how they behave. Different inks have different properties, and mixing them without this understanding can lead to issues like poor adhesion, inconsistent colors, or prints that fade over time.
1. Plastisol Screen Printing Ink
Plastisol screen printing ink is one of the most popular inks used in the industry. It’s known for its durability, vibrant colors, and flexibility. Plastisol ink doesn’t dry unless heat cured, making it easy to use for long print runs. When mixing plastisol screen printing inks, it’s essential to stick to the same type to ensure compatibility. This means that mixing plastisol screen printing ink with other screen printing inks, like water-based screen print ink, is not recommended due to their differing chemical properties.
2. Water-Based Screen Printing Ink
Water-based screen printing ink offers a softer finish and is a more eco-friendly alternative to plastisol. While it’s possible to mix different colors of water based screen print ink, combining it with plastisol or other inks can result in adhesion problems or a reduction in durability. Water-based ink screen printing is ideal for achieving a more natural look, especially on lighter fabrics.
3. Discharge Ink Screen Printing
Discharge ink is another type of screen printing ink that removes the dye from the fabric, leaving a soft, vintage look. It can be combined with other discharge inks to create custom colors, but like other inks, it’s best to avoid mixing it with plastisol or water based screen printing ink, as they cure and interact differently with fabrics.
4. Specialty Screen Printing Inks
There are many specialty screen printing inks designed to achieve unique effects, including:
- Glow in the dark screen printing ink: Creates luminous prints that glow in the dark.
- Metallic gold screen printing ink: Adds a metallic sheen to prints, ideal for bold, eye-catching designs.
- Reflective screen printing ink: Reflects light, making designs visible in low-light conditions.
Mixing specialty screen printing inks like glow in the dark screen printing ink or reflective screen printing ink requires caution. Always conduct test prints when blending specialty inks to ensure they achieve the desired effect without compromising the ink’s unique properties.
Can You Mix Different Types of Screen Printing Inks?
While it’s tempting to mix different types of screen printing inks to create custom effects, it’s crucial to remember that not all inks are compatible with each other. Here’s a breakdown of what you can and cannot mix:
1. Mixing Plastisol Inks
Mixing different colors of plastisol screen printing ink is common practice and is an excellent way to create custom colors. Plastisol inks are highly versatile, and because they don’t dry on the screen, you can mix them to match your specific design needs. For example, you can blend screen printing ink white with a bold color to create pastels or mix metallic screen printing inks to achieve a unique shimmer.
However, mixing plastisol screen printing ink with water based ink screen printing or discharge ink screen printing is not recommended. These inks have different curing processes, and combining them can result in uneven prints or prints that don’t adhere well to the fabric.
2. Mixing Water-Based Inks
You can safely mix different colors of water-based screen printing ink to create a wide range of hues. Water-based inks dry quickly, so it’s essential to move efficiently when printing. Mixing water-based screen printing inks can yield beautiful, soft prints on fabrics, especially when used on light-colored materials like cotton. However, avoid mixing water-based screen printing inks with plastisol ink as this can cause the ink to crack or peel after washing.
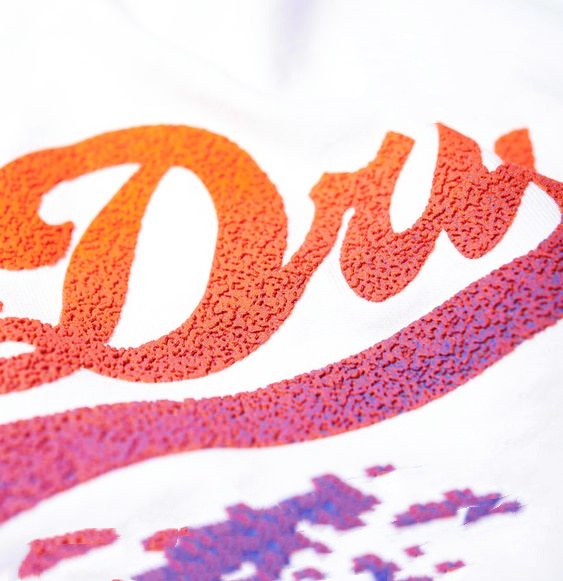
3. Mixing Puff Ink
Puff ink for screen printing expands when heated, creating a raised, 3D effect. It’s possible to mix puff ink screen printing with other plastisol screen printing inks to add texture and volume to your design. However, mixing it with water based screen printing ink or other specialty inks can compromise the puff effect. Always test your mixes before going into full production to ensure the desired results.
Benefits of Mixing Screen Printing Inks
Mixing screen printing inks opens up a world of creative possibilities. Here are a few reasons why printers choose to blend different ink types and colors:
1. Custom Colors
Mixing different screen printing inks allows you to create custom colors that perfectly match your design. This is especially useful for branding projects where color consistency is essential.
2. Unique Textures
Blending specialty inks, such as puff ink screen printing with standard plastisol screen printing ink, can add texture and dimension to your prints, making your designs stand out.
3. Special Effects
By mixing reflective screen printing ink, metallic gold screen printing ink, or glow in the dark screen printing ink with other inks, you can achieve eye-catching effects that enhance the visual appeal of your prints.
Challenges of Mixing Screen Printing Inks
While mixing screen printing inks has its advantages, there are also challenges and risks involved:
1. Incompatibility
Mixing incompatible inks, such as water based screen printing ink with plastisol screen printing ink, can lead to issues like poor adhesion, cracking, or peeling. Always ensure that the inks you are blending are compatible before proceeding.
2. Uneven Curing
Different inks have different curing temperatures and times. Mixing inks with varying curing requirements can result in uneven prints or prints that don’t cure properly, leading to durability issues.
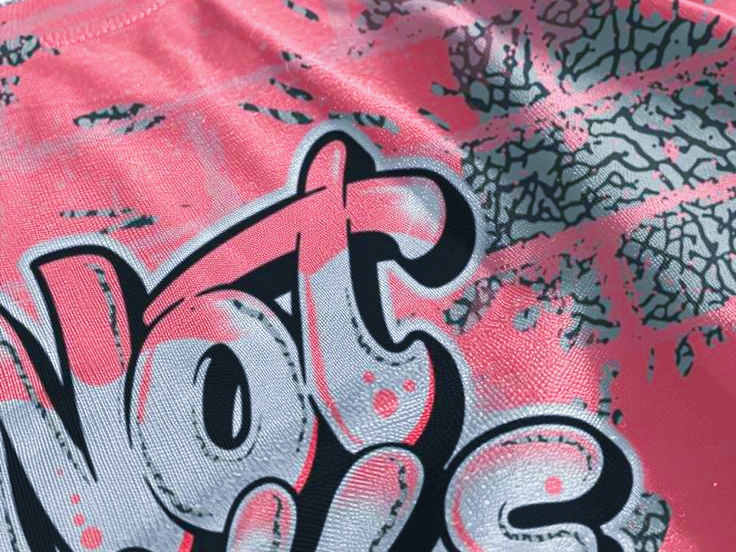
3. Color Consistency
Achieving consistent colors can be difficult when mixing different types of screen printing inks. Even slight variations in mixing can result in noticeable differences in color from one print run to the next. It’s crucial to measure and document your ink mixes for consistent results.
Best Practices for Mixing Screen Printing Inks
To get the best results when mixing screen printing inks, follow these best practices:
1. Stick to Compatible Inks
Only mix inks that are chemically compatible. For example, blend plastisol screen printing ink with other plastisol inks, or mix water-based screen printing ink with other water-based inks. Avoid combining incompatible inks like plastisol and discharge ink screen printing or water based screen print ink to prevent curing and adhesion problems.
2. Measure Your Mixes
When creating custom colors, use precise measurements to ensure consistency. Document your ink ratios so that you can recreate the exact same color in future print runs.
3. Conduct Test Prints
Before running a full production with your mixed screen printing inks, always conduct test prints. This will help you identify any issues with color consistency, adhesion, or curing and allow you to make adjustments before proceeding.