Conclusion
Properly curing ink for printing shirts is crucial to ensure your prints are durable, vibrant, and long-lasting. Whether you’re using plastisol screen printing ink, water-based ink, or silk screen printing paint, choosing the right curing method can make all the difference in the quality of your final product.
From heat guns to conveyor dryers, understanding the tools available for curing will help you select the best option for your shop. With the right techniques, you can ensure your prints look great and stand the test of time.
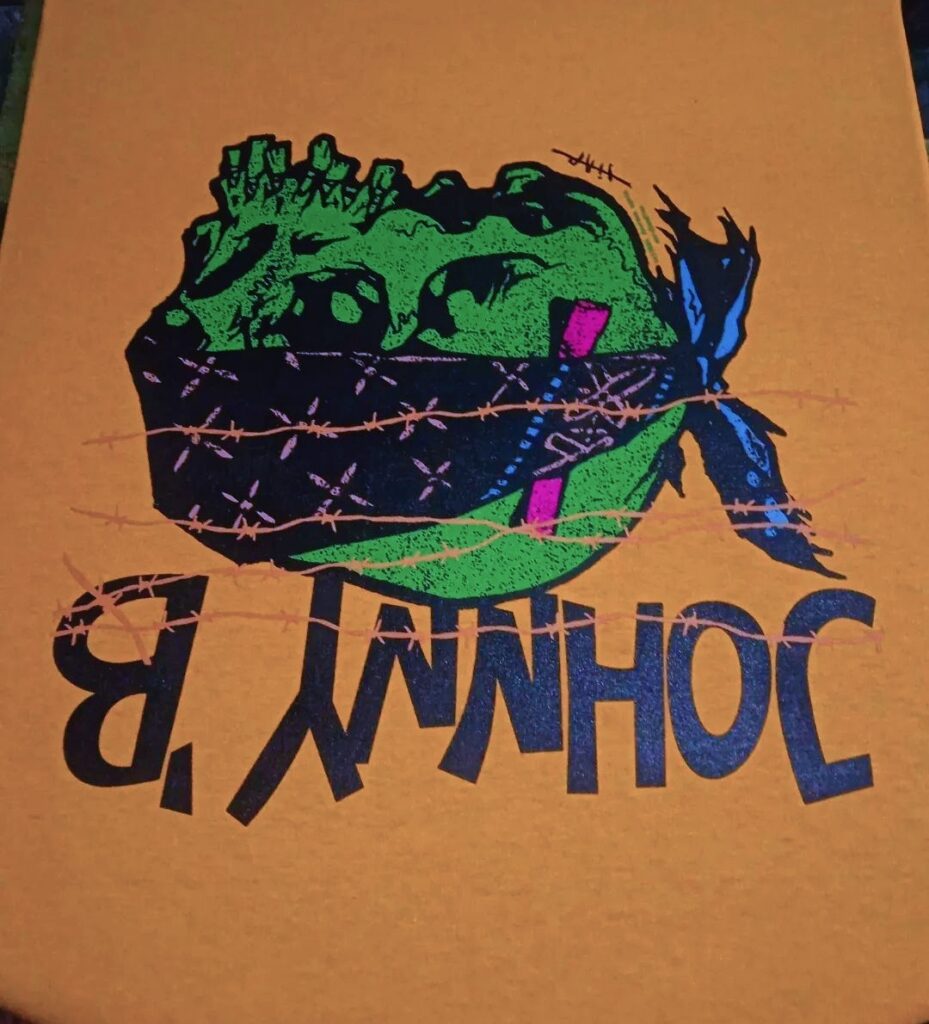
How to Cure Ink for Printing Shirts?
Curing is a crucial step in the screen printing process that determines the longevity and durability of your prints. If the ink isn’t properly cured, even the best ink for silk screen printing can crack, peel, or fade after just a few washes. This article will guide you through the different methods for curing ink for printing shirts, highlight the tools you’ll need, and offer tips for ensuring your prints last as long as possible.
Why Curing Ink for Printing Shirts is Essential
Curing is the process of applying heat to the ink so it bonds with the fabric. If done correctly, it ensures that the ink remains vibrant and durable, preventing any damage from washing, stretching, or general wear and tear. For plastisol screen printing ink in particular, curing is key to achieving a soft, flexible, and long-lasting print.
Whether you’re using screen printing ink for fabric or silk screen printing paint, proper curing solidifies the ink into the fabric fibers, locking in the design. Without proper curing, even the best silk screen ink may lose its shine and crack over time.
Understanding “Full Cure” to Ink for Printing Shirts
A “full cure” means the ink for printing shirts has been heated to the point where it becomes permanently bonded to the fabric. The temperature required to achieve this varies depending on the type of ink used.
- Water-based inks: Typically require curing at temperatures between 300°F and 320°F.
- Plastisol screen printing ink: Generally requires curing at around 320°F, though low-cure plastisol inks can cure at temperatures as low as 260°F.
The ink must reach this temperature from the top layer down to the fabric to be considered fully cured. For screen printing plastisol int, achieving a full cure is critical to ensuring the ink doesn’t wash away or crack over time.
Tools for Curing Ink for Printing Shirts
Different tools can be used to cure ink for printing shirts, and each method has its pros and cons depending on your budget, the size of your printing operation, and the type of ink you’re using. Below are the most common methods for curing ink:
1. Heat Gun: Affordable but Limited
A heat gun is one of the most budget-friendly tools for curing ink for printing shirts. It’s ideal for small-scale operations or for curing small areas of a design, such as logos or chest prints. However, heat guns come with limitations.
The main issue with heat guns is inconsistency. It’s hard to control the temperature accurately, and uneven heat distribution can cause some areas of the print to overheat while others remain under-cured. This is especially problematic for larger designs where maintaining a consistent temperature is crucial. For plastisol screen printing ink, use a heat gun until the ink is dry to the touch. After curing, always perform a wash test to ensure the ink has fully set into the fabric.
Ink for Printing Shirts Pro Tip:
Low-cure plastisol screen printing ink can be easier to cure with a heat gun since it requires lower temperatures to reach full cure. However, always test each garment after curing to avoid any future print issues.
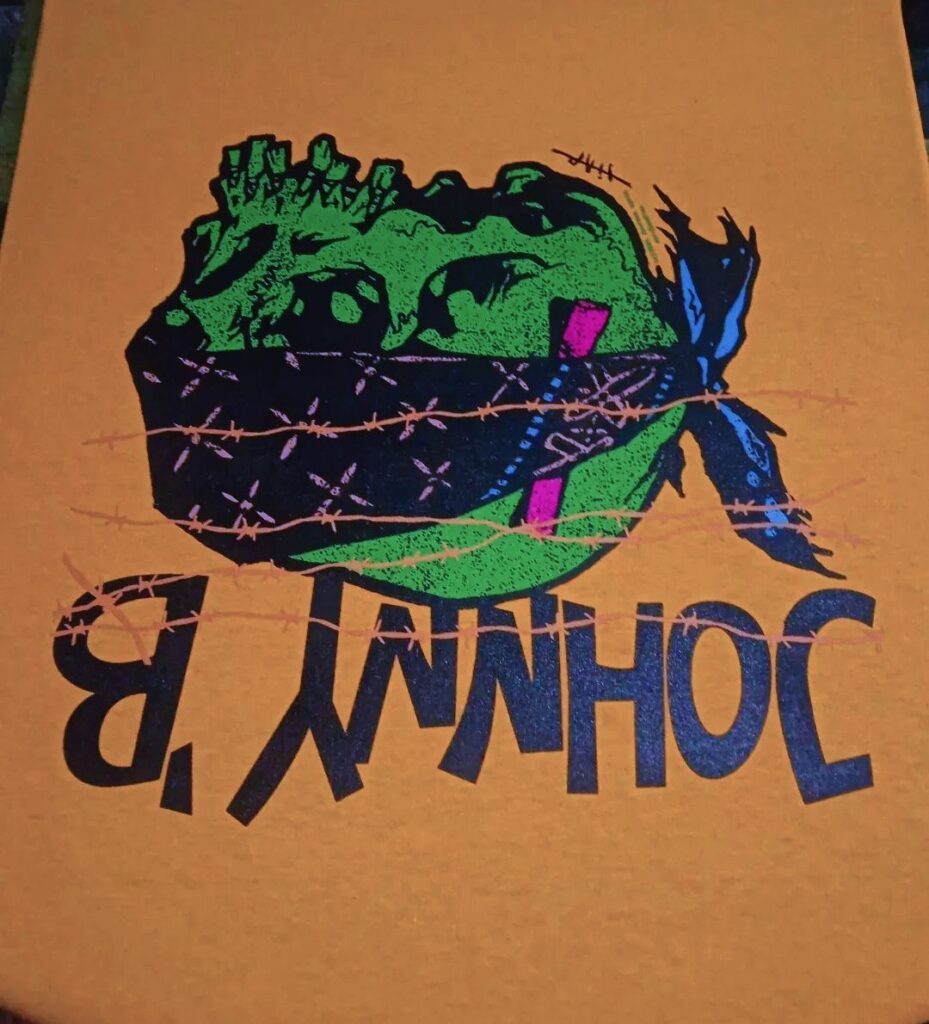
2. Flash Dryer: Ideal for Small to Medium Jobs
A flash dryer is a popular tool in the screen printing world, providing a more consistent and controlled curing process compared to a heat gun. Flash dryers are often used to quickly cure ink for printing shirts by hovering above the fabric and evenly distributing heat across the entire design.
Flash dryers are particularly effective for screen printing ink for fabric that covers a larger area. They offer better control over the curing process, helping to avoid under-curing or overheating specific parts of the design. However, flash dryers can be more expensive than heat guns, making them more suitable for medium-scale operations or shops looking to scale up their production.
3. Conveyor Dryer: Best for Large-Scale Production
If you’re working with high volumes of shirts, a conveyor dryer is the most efficient and reliable method for curing plastisol screen printing ink and other inks. Conveyor dryers provide a consistent, controlled environment for heat curing, allowing multiple garments to be cured at once as they move along a conveyor belt.
This method ensures that every part of the print reaches the proper curing temperature, making it ideal for silk screen printing paint that requires precision. Conveyor dryers are designed for high-output printing shops, and while they can be a significant investment, they dramatically increase efficiency for large-scale projects.
How to Achieve Proper Curing for Different Inks
Different inks have specific curing requirements, and understanding these will help you avoid common issues like under-cured or over-cured prints.
Curing Plastisol Screen Printing Ink
Plastisol screen printing ink is a favorite among screen printers due to its durability, opacity, and ease of use. Plastisol inks require heat to cure fully, typically at around 320°F. The ink doesn’t air-dry, so it remains wet until exposed to the proper heat, making it more forgiving during the printing process.
Once heated to the correct temperature, plastisol inks bond permanently with the fabric, creating a vibrant and durable print. However, under-curing can cause the ink to remain soft and susceptible to cracking or washing out. Always ensure that the ink has reached its full cure temperature by using a temperature gun to measure the heat during curing.
Curing Water-Based Ink
Screen printing ink for fabric that is water-based requires a different curing process than plastisol. Water-based inks dry as the water in the ink evaporates. To fully cure water-based ink, the temperature needs to be between 300°F and 320°F. However, these inks also require airflow to assist with evaporation, making proper ventilation critical.
Using a heat gun alone is often not sufficient for curing water-based ink for printing shirts. For best results, a flash dryer or conveyor dryer is recommended to ensure that the ink dries evenly across the fabric.
Testing If Your Print Is Fully Cured
After curing ink for printing shirts, it’s essential to test whether the print is fully cured to avoid potential issues later on. The most reliable way to test this is through a wash test.
Simply wash the garment as you normally would, and inspect the print after. If the print shows signs of cracking, peeling, or fading, it hasn’t fully cured. For plastisol screen printing ink, another useful test is the stretch test. After curing, stretch the fabric slightly. If the ink cracks, it needs more time under the heat source.
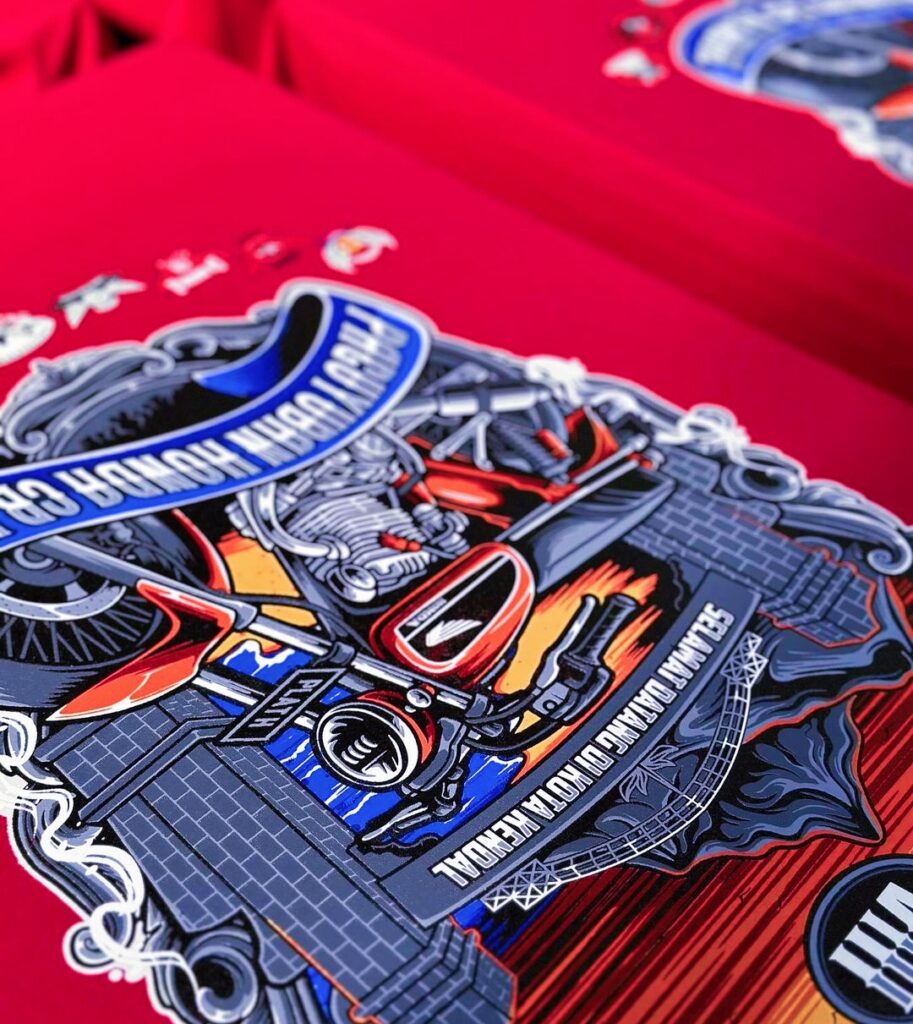
Common Issues with Curing and How to Avoid Them
Curing ink for printing shirts isn’t without its challenges. Here are a few common problems and how to avoid them:
- Under-Curing: This occurs when the ink doesn’t reach the necessary temperature to bond with the fabric. It’s often caused by using a heat gun that doesn’t provide consistent heat. The solution is to use a flash or conveyor dryer, which can more evenly distribute heat.
- Over-Curing: Over-curing happens when the ink is exposed to too much heat, which can lead to discoloration, especially with metallic inks like Gold Silkscreen Ink. Be mindful of the heat settings on your curing equipment and always measure the ink’s temperature as it cures.
- Inconsistent Heat: Some areas of the print might cure fully while others don’t. This can be avoided by ensuring that the curing device is properly calibrated and that the garment is positioned evenly under the heat source.
Curing Inks on Different Fabric Types
Different fabrics require different curing approaches. For example, plastisol screen printing ink is ideal for natural fabrics like cotton, which can withstand the higher curing temperatures. However, synthetic fabrics like polyester are more heat-sensitive and can scorch if exposed to too much heat.
For heat-sensitive fabrics, consider using low-cure plastisol inks that cure at lower temperatures, reducing the risk of damage while still ensuring the ink bonds securely to the fabric.