Printing black on black may sound like a challenge, but with the right techniques, you can create stunning, subtle, and sophisticated designs. Whether you’re using black screen printing ink or exploring other methods, this guide will walk you through six effective ways to make your designs stand out on black shirts.
Puff Print
Puff print is a popular method for adding texture and dimension to a design, making it an excellent choice for printing black screen printing ink on black shirts. This technique uses puff ink, which expands when exposed to heat, creating a raised, three-dimensional effect on the fabric.
When using puff printing on a black shirt with screen printing ink black, the key is in the contrast between the raised puffed areas and the flat fabric. The subtle shadowing and texture provided by the puff print can make the design visible even though it’s black on black. The result is a sophisticated and tactile design that stands out without relying on color contrast.
To achieve the best results with puff print on a black shirt:
- Design Simplicity: Stick to simple, bold designs. Intricate details might get lost in the puffing process.
- Ink Selection: Choose a puff ink that matches the texture and finish you want for your design. Puff inks come in various finishes, from matte to glossy, and can work beautifully with black ink screen printing.
- Heat Curing: Ensure the shirt is heated at the right temperature to fully activate the puff effect without over-expanding, which could distort the design.
Puff print is a versatile technique that not only adds visual interest but also enhances the tactile experience of the garment, making it a favorite for creating unique black-on-black designs with black screen printing ink.
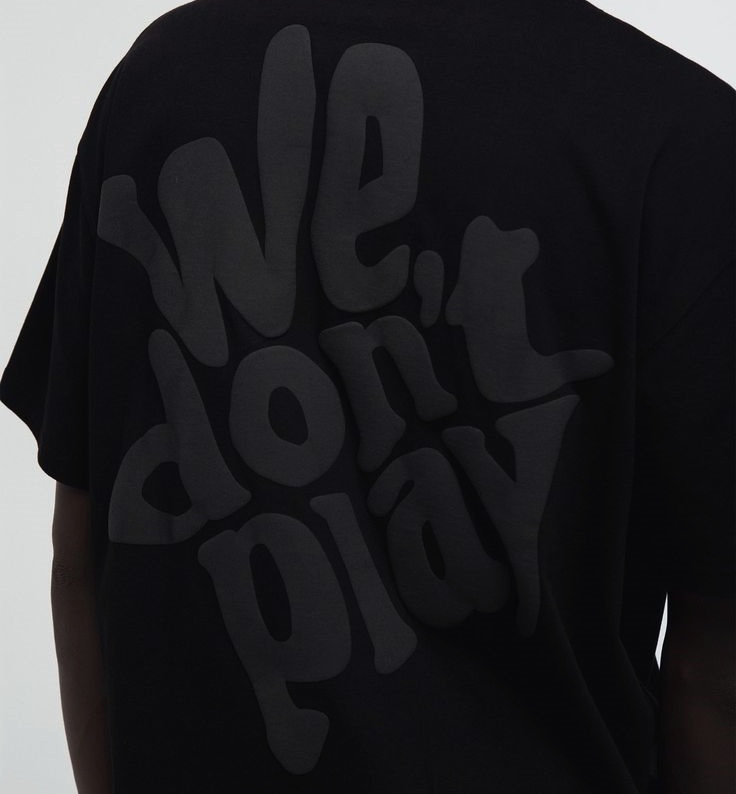
Clear Base
Using a clear base is another effective method for printing black screen printing ink on black shirts. A clear base is a transparent ink that can be mixed with a small amount of black pigment to create a subtle, glossy effect on the fabric. This method allows the design to have a slight sheen, making it visible under certain lighting conditions.
The clear base technique is particularly effective for creating tone-on-tone designs, where the design is visible due to its finish rather than its color. On black shirts, this can result in a design that is understated yet elegant, perfect for more sophisticated or minimalist branding using black screen printing ink.
Steps to achieve the clear base effect with black screen printing ink:
- Ink Preparation: Mix black screen printing ink with a clear base to achieve the desired level of transparency and sheen.
- Screen Preparation: Ensure your screen is prepared with a design that works well with the subtlety of the clear base.
- Printing: Apply the ink carefully, maintaining consistency to avoid streaks or uneven coverage.
- Curing: Proper curing is crucial to ensure the design adheres well and the sheen effect is preserved.
Using a clear base offers a subtle yet stylish way to print black screen printing ink on black shirts, making it ideal for designs that are meant to be more subdued and sophisticated.
Black Screen Printing Ink
Sometimes, the simplest method is the most effective. Using black screen printing ink on a black shirt can create a striking look, especially when combined with the right techniques.
The key to using black screen printing ink on black fabric is to play with texture and finish. For example, combining a matte black screen printing ink with a glossy black shirt can create a noticeable contrast. Alternatively, you can use different layers of black screen printing ink to build up a design that is visible through texture rather than color.
To make the most of black screen printing ink on black shirts:
- Ink Selection: Choose a high-quality black screen printing ink that matches the finish you want—whether matte, glossy, or somewhere in between.
- Layering: Consider using multiple layers of black screen printing ink to create a design with depth. This can involve printing the design multiple times or using thicker layers of ink.
- Contrast Techniques: Utilize the contrast between different finishes—matte ink on a glossy shirt or vice versa—to make the design stand out.
This approach relies on subtle contrasts and the physical texture of the ink, making it perfect for creating designs that are both elegant and understated using black screen printing ink.
Smoothing Screen
A smoothing screen technique is another way to create texture and subtle contrasts when printing black screen printing ink on black shirts. This technique involves using a special screen that smooths out the ink after it has been applied, creating a more even and consistent layer.
The smoothing screen can be used to achieve a sleek, polished look, which is particularly effective for black-on-black designs. By reducing the texture of the ink, the design becomes more about the play of light on the surface, with the smoothness creating a subtle but visible effect using black screen printing ink.
Steps to use a smoothing screen effectively with black screen printing ink:
- Ink Application: Apply the black screen printing ink as usual, ensuring even coverage.
- Smoothing: Run the smoothing screen over the printed area to flatten and even out the ink. This process should be done carefully to avoid over-smoothing, which could remove too much ink.
- Curing: After smoothing, cure the ink to ensure it adheres properly and the smooth finish is maintained.
Using a smoothing screen allows for a sleek and polished look that is particularly effective for designs requiring a refined, minimalist appearance with black screen printing ink.
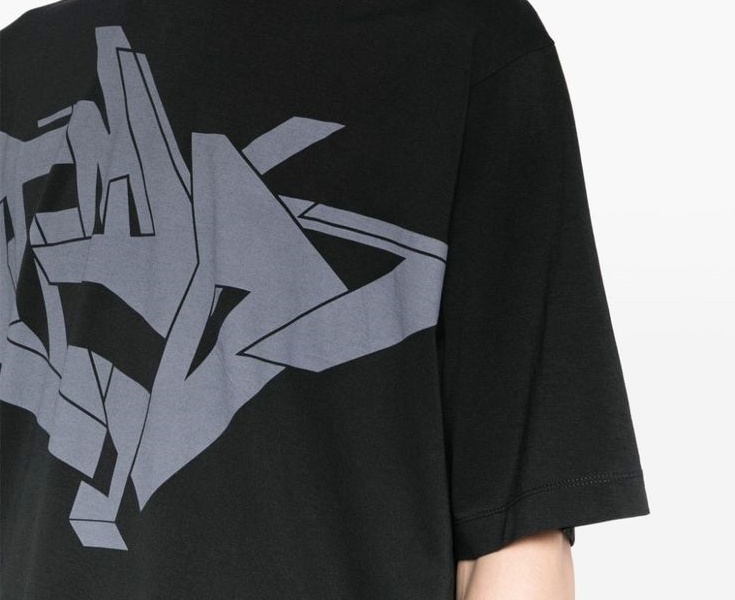
Thick Layer Printing
Thick layer printing involves applying a heavier-than-normal layer of screen printing ink black to create a design that is visible through texture rather than color. This technique is particularly effective when using black screen printing ink on black shirts.
The thickness of the ink creates a raised surface that catches the light differently from the surrounding fabric, making the design visible despite the lack of color contrast. This method can also add a tactile element to the design, making it not only visible but also felt when touched.
To achieve effective thick layer printing with black screen printing ink:
- Ink Preparation: Use a thick, high-quality screen printing ink black that is capable of being applied in a heavy layer without cracking.
- Screen Setup: Use a screen with a high mesh count to control the amount of ink applied to the shirt.
- Printing: Apply the black screen printing ink in multiple passes to build up the thickness, ensuring that each layer is even and consistent.
- Curing: Proper curing is essential to prevent cracking and ensure that the thick layers of black screen printing ink adhere well to the fabric.
Thick layer printing is an excellent way to create bold, textured designs that stand out on black shirts, even when using black screen printing ink.
Use an Underbase
Using an underbase is a classic screen printing technique that can be particularly effective when printing black screen printing ink on black shirts. An underbase is a layer of ink, typically white or gray, that is printed beneath the top layer of black screen printing ink. This underbase creates a foundation that enhances the visibility of the top layer of ink.
When printing black screen printing ink on a black shirt, using a subtle gray or even a clear underbase can create a slight contrast, making the top layer of black screen printing ink more visible. This technique allows for a more pronounced design while still maintaining the overall black-on-black aesthetic.
Steps to use an underbase effectively with black screen printing ink:
- Underbase Selection: Choose an underbase ink that provides the right amount of contrast without overpowering the black-on-black effect.
- Layering: Print the underbase layer first, ensuring even coverage. Once cured, print the top layer of black screen printing ink over the underbase.
- Curing: Proper curing of both the underbase and the top layer is essential to ensure the durability of the design.
Using an underbase can significantly enhance the visibility of black screen printing ink on black shirts, making it an effective technique for more detailed or intricate designs.
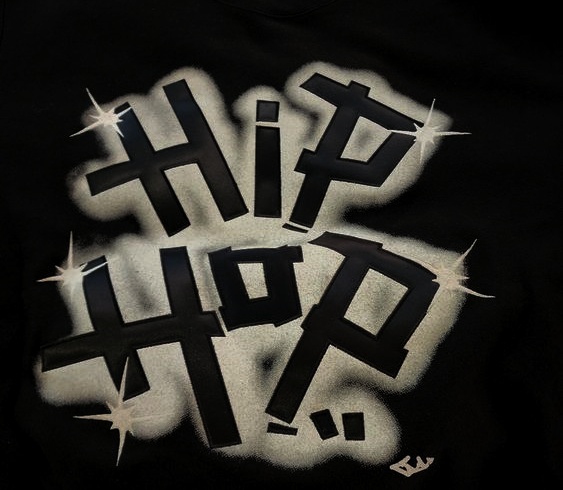
Compare and Contrast
When considering the various techniques for printing black screen printing ink on black shirts, it’s important to compare and contrast the options to determine which best suits your design needs. Each method offers unique advantages, depending on the desired effect and the specific characteristics of the shirt and ink used.
- Puff Print vs. Thick Layer Printing: Puff print adds dimension through expansion and is ideal for more playful, textured designs, while thick layer printing relies on the physical buildup of black screen printing ink to create texture and visibility.
- Clear Base vs. Use of Underbase: A clear base offers a subtle, tone-on-tone effect, perfect for minimalist designs, whereas an underbase allows for more pronounced contrast, making the design stand out more distinctly using black screen printing ink.
- Smoothing Screen vs. Standard Black Ink: The smoothing screen technique creates a polished, sleek finish, while standard black screen printing ink can vary in texture depending on the layering and ink type used.
Understanding the differences between these techniques allows for more informed decisions when choosing the best method for your black-on-black printing projects with screen printing ink black.
Conclusion
Printing black screen printing ink on a black shirt may seem challenging, but with the right techniques, it’s possible to create stunning, sophisticated designs that stand out. Whether you choose puff print, clear base, thick layer printing, or another method, each technique offers unique benefits that can enhance the overall aesthetic and tactile appeal of your designs.
By experimenting with these six methods, you can discover the perfect approach for your specific needs, allowing you to create high-quality, eye-catching black-on-black apparel that resonates with your audience using screen printing ink black.