Selecting the right mesh printing screen is essential for achieving high-quality results in screen printing. The mesh count, size, and other factors can significantly impact the outcome of your prints, especially when using plastisol ink or other types of screen printing ink. This guide will help you understand the basics of mesh selection and how to make the best choice for your specific needs.
Mesh Printing Screen Count Basics
The mesh count refers to the number of threads per inch in a screen printing mesh. This count directly affects the detail and ink deposit in your prints. A higher mesh count means finer threads and smaller openings, allowing less ink to pass through, while a lower mesh count has thicker threads and larger openings, permitting more ink to pass.
Low Mesh Counts
Low mesh counts, typically ranging from 25 to 85 threads per inch, are ideal for printing bold designs that require a significant amount of ink, such as those involving plastisol ink. These screens are commonly used for printing on dark fabrics, where a thick ink layer is necessary to achieve opacity. Low mesh counts are also suitable for specialty inks like glitter or puff inks, where a substantial ink deposit is required.
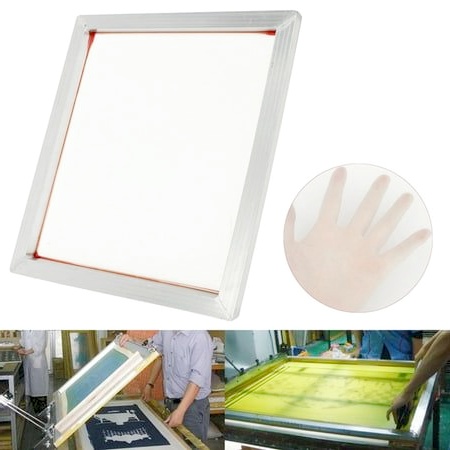
Medium Mesh Counts
Medium mesh counts, usually between 86 and 196 threads per inch, are versatile and widely used in screen printing. They provide a balance between ink deposit and detail, making them suitable for a variety of applications. For example, they work well with screen printing ink plastisol on light-colored fabrics, where moderate ink coverage and detail are both essential.
High Mesh Counts
High mesh counts, ranging from 200 to 355 threads per inch, are used for printing fine details, halftones, and intricate designs. These screens allow for a thinner layer of ink, making them ideal for delicate prints where precision is critical. High mesh counts are often chosen for printing on light fabrics with water-based inks or when using plastisol ink for detailed designs.
Knowing the Mesh Size to Use
Choosing the correct mesh size for your project involves understanding how the mesh count interacts with the type of ink, the detail of the design, and the fabric being printed.
Ink Type and Mesh Size
The type of ink you use plays a significant role in determining the appropriate mesh size. Plastisol ink, known for its thick consistency, typically requires a lower mesh count to allow sufficient ink flow. A mesh count around 110 is commonly used for printing designs with plastisol ink, ensuring a robust ink deposit that adheres well to the fabric.
For thinner inks, like water-based or discharge inks, a higher mesh count is necessary to control the ink flow and prevent oversaturation. Mesh counts in the range of 230 to 305 are ideal for these types of inks, ensuring that the print retains fine details and a smooth finish.
Design Complexity
The complexity of your design also influences the choice of mesh size. Intricate designs with fine lines and small details require a high mesh count to ensure that the print is sharp and clear. For such designs, a mesh count of 230 or higher is recommended. On the other hand, simpler designs with bold lines can be effectively printed with a lower mesh count, allowing for more ink to pass through the screen.
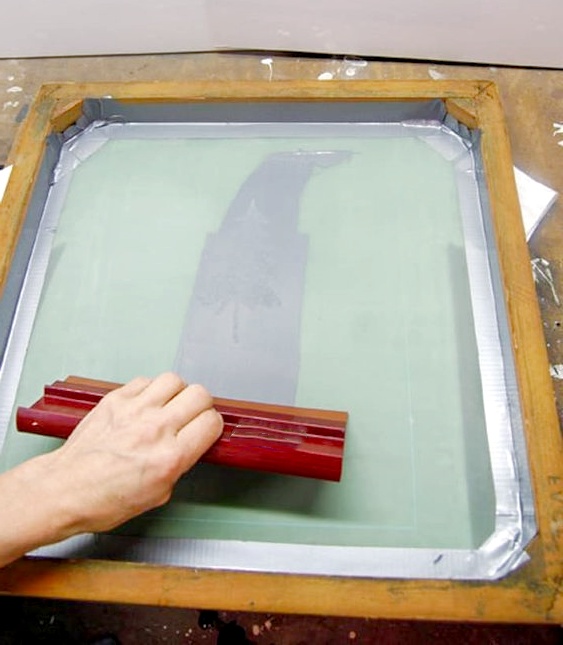
Fabric Considerations
The type of fabric you’re printing on can affect your choice of mesh size. Coarse fabrics, like burlap or canvas, benefit from a lower mesh count, which allows more ink to penetrate the material. Softer fabrics, such as cotton or polyester, typically require a higher mesh count to avoid oversaturation and maintain the fabric’s texture.
Other Considerations When Choosing a Mesh Printing Screen Count
While mesh count is crucial, other factors also play a role in selecting the right mesh for your screen printing project. These include the material of the mesh, thread diameter, and tension.
Mesh Material
Most screen printing meshes are made from polyester due to its durability and resistance to chemicals. Polyester mesh is suitable for most applications and offers a good balance between strength and flexibility. However, some specialized projects may require alternative materials like nylon or stainless steel. Nylon mesh is more flexible but less durable, making it ideal for certain applications. Stainless steel mesh, though more expensive, provides excellent strength and is often used in high-precision printing.
Thread Diameter
The diameter of the threads used in the mesh affects both the durability of the screen and the amount of ink that can pass through. Thicker threads result in a more durable screen but reduce the amount of ink flow, which can be beneficial for controlling ink deposits. Thinner threads allow more ink to pass through but may reduce the screen’s lifespan.
Mesh Tension
The tension of the mesh on the frame is another critical factor in screen printing. Proper tension ensures that the screen remains stable during printing, resulting in a crisp and clear image. Over-tensioning, however, can damage the screen or cause warping, so it’s essential to maintain an optimal balance.
Regularly checking and adjusting the tension of your mesh printing screen is crucial to achieving consistent, high-quality prints. Tools like tension meters can help ensure that your screens are properly tensioned for each project.
Conclusion
Choosing the right mesh printing screen is a fundamental step in achieving high-quality screen prints. By understanding mesh count basics, knowing how to match mesh size with your ink and design, and considering factors like fabric type and mesh material, you can ensure that your prints come out perfectly every time. Whether you’re working with plastisol ink, screen printing ink plastisol, or another type of ink, selecting the appropriate mesh printing screen will significantly impact the success of your screen printing projects.