Curing plastisol ink is a crucial step in screen printing, determining the durability, longevity, and overall quality of your prints. Achieving the right curing temperature ensures that the ink bonds properly to the fabric, creating a design that can withstand the test of time. In this article, we’ll explore the optimal temperature to cure plastisol ink, along with practical tips and techniques to ensure your prints are fully cured.
How to Test a Plastisol Direct Print for Proper Cure
Before diving into the specifics of curing temperatures, it’s important to understand how to test whether your plastisol ink has been properly cured. A fully cured print will be durable, resistant to washing, and maintain its vibrant colors.
Stretch Test
One of the simplest methods to test for proper curing is the stretch test. After curing, allow the print to cool down, then gently stretch the fabric. If the ink cracks, peels, or shows signs of deterioration, it may not have been cured properly. A well-cured plastisol print should stretch with the fabric without showing any damage.
Wash Test
Another effective method is the wash test. Wash the printed garment in warm water with a mild detergent, then inspect the print for any signs of fading, cracking, or peeling. If the ink remains intact and vibrant, it’s a good indication that the plastisol ink was cured at the correct temperature.
Temperature Check
For precise curing, it’s essential to use a temperature gun or a laser thermometer to monitor the heat during the curing process. Plastisol ink typically cures at a temperature of around 320°F (160°C). Ensure that the entire print reaches this temperature to achieve a full cure. Any areas that do not reach this temperature may result in an under-cured print.
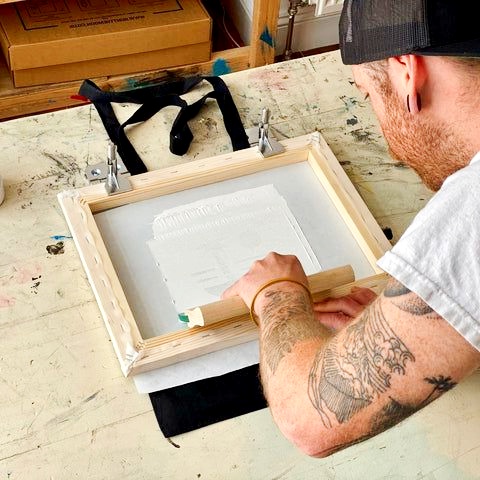
Adjusting Your Conveyor Dryer
A conveyor dryer is one of the most efficient tools for curing plastisol ink, especially for high-volume screen printing operations. To cure plastisol ink effectively, it’s important to understand how to adjust your conveyor dryer to maintain the right temperature throughout the curing process.
Temperature Settings
Set the conveyor dryer to maintain a consistent temperature of around 320°F (160°C). Depending on the thickness of the ink layer and the type of fabric, you may need to adjust the dryer’s settings to ensure that the entire print reaches the required temperature.
Belt Speed
The speed of the conveyor belt also plays a critical role in curing plastisol ink. If the belt moves too quickly, the ink may not have enough time to reach the full curing temperature, resulting in an under-cured print. Conversely, if the belt moves too slowly, the ink could overheat, potentially damaging the fabric. Adjust the belt speed to allow enough time for the ink to reach and maintain the curing temperature.
Even Heat Distribution
Ensure that the heat is evenly distributed across the entire surface of the conveyor dryer. Uneven heat can lead to inconsistent curing, with some areas of the print under-cured and others potentially over-cured. Regularly check the dryer for hot spots or cool areas and make adjustments as needed to maintain even heat distribution.
Flash or Spot Cure Drying
Flash curing, also known as spot curing, is a technique used to partially cure plastisol ink before applying additional layers or performing the final full cure. This method is particularly useful when printing multi-color designs, where you need to cure each layer of ink before applying the next.
Flash Cure Units
Flash cure units are designed to deliver quick bursts of high heat to partially cure the ink. Typically, flash curing is done at a temperature slightly lower than the full curing temperature, around 280-300°F (138-149°C). The goal is to gel the ink just enough so it can hold additional layers without smudging or blending.
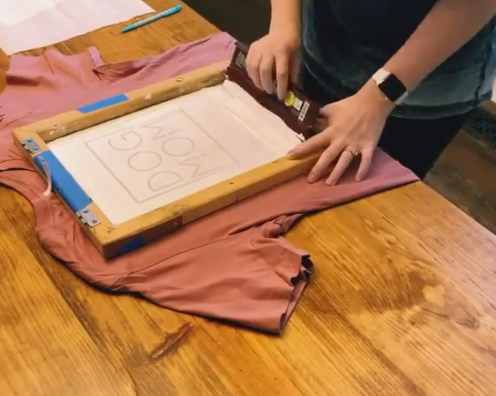
Time and Temperature
Flash curing should only take a few seconds, usually between 5-10 seconds, depending on the thickness of the ink layer and the specific requirements of your design. It’s important not to over-flash the ink, as this can cause the ink to over-cure, making it difficult for additional layers to adhere properly.
Importance of Final Cure
After all layers have been applied and flash cured, it’s crucial to perform a final full cure to ensure the entire print reaches the proper curing temperature of 320°F (160°C). This step is necessary to fuse the ink fully to the fabric, providing a durable and long-lasting print.
Important Drying/Curing Tips
Achieving the perfect cure for plastisol ink involves more than just reaching the right temperature. Here are some essential tips to ensure your prints are properly cured every time:
Monitor Ambient Conditions
Ambient conditions, such as the room temperature and humidity, can affect the curing process. High humidity can cause the ink to cure more slowly, while low humidity can speed up the process. Ensure your work environment is stable and consistent to achieve reliable curing results.
Use a Temperature Probe
For more precise temperature control, consider using a temperature probe inserted into the ink layer during curing. This method allows you to monitor the exact temperature within the ink, ensuring it reaches the full cure temperature without overheating.
Avoid Overloading the Dryer
Overloading the conveyor dryer with too many garments at once can lead to uneven curing. Ensure that each garment has enough space on the conveyor belt to receive even heat distribution. Overcrowding can cause some prints to cure unevenly, resulting in quality issues.
Preheat the Dryer
Before starting a new batch of garments, preheat the conveyor dryer to ensure it’s at the correct temperature from the first print. This step helps maintain consistent curing across all garments and prevents the first few prints from under-curing due to a cold dryer.
Regular Maintenance
Regularly inspect and maintain your curing equipment to ensure it’s functioning properly. Clean the heating elements, check for any signs of wear, and calibrate the temperature settings as needed. Well-maintained equipment is essential for achieving consistent and reliable curing results.
Conclusion
Curing plastisol ink is a critical step in the screen printing process that ensures your designs are durable, vibrant, and long-lasting. The optimal temperature to cure plastisol ink is around 320°F (160°C), and achieving this temperature consistently is key to producing high-quality prints. By following the tips and techniques outlined in this article, you can ensure that your plastisol ink is fully cured and your prints stand the test of time.
Whether you’re using a conveyor dryer, flash curing, or other methods, understanding the importance of temperature control and curing time will help you achieve the best possible results in your screen printing projects.