How to Cure Plastisol Ink?Curing plastisol ink is an essential step in the screen printing process, ensuring that your designs are vibrant, durable, and long-lasting. Without proper curing plastisol ink can remain soft, sticky, and prone to washing out. In this article, we’ll explore what it means for plastisol ink to be fully cured and detail three reliable methods to achieve a complete cure.
What does Cure Mean
When we talk about curing plastisol ink, achieving a “full cure” is critical. But what exactly does this term mean?
A full cure for plastisol ink occurs when the ink reaches the correct temperature for a sufficient amount of time. Typically, plastisol ink must be heated to around 320°F (160°C) to properly cure. This process causes the PVC (polyvinyl chloride) particles within the ink to fuse together, resulting in a solid, durable print that won’t crack or peel.
A well-cured plastisol print will withstand multiple washes, maintain its vibrant colors, and resist fading or damage over time. However, if the ink doesn’t reach the proper curing temperature or isn’t cured for long enough, the print may appear fine initially but will degrade quickly once the garment is worn and washed.
Ensuring a full cure requires careful attention to temperature and time, and there are several methods you can use to achieve this.
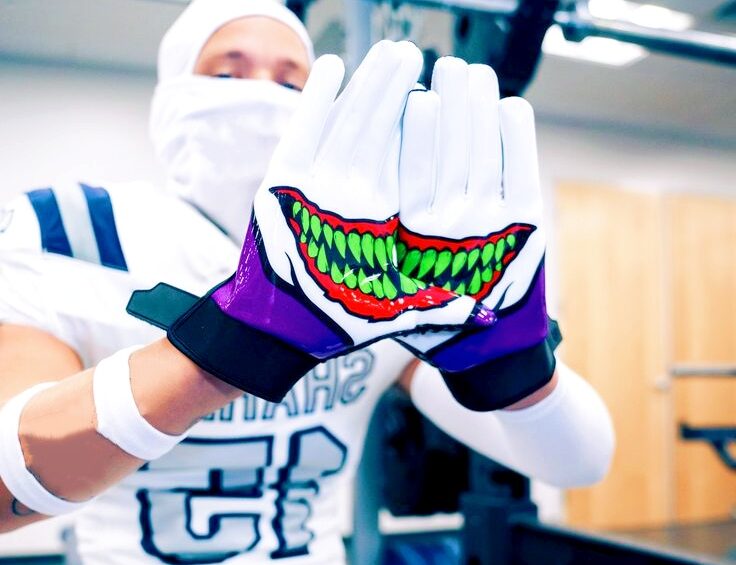
Curing Via Heat Gun
Using a heat gun is one of the most accessible methods for curing plastisol ink, especially for small projects or individual prints. Heat guns are handheld devices that blow hot air onto the ink, raising the temperature to the necessary level for curing.
Steps to Cure Plastisol Ink with a Heat Gun:
- Preheat the Gun: Turn on the heat gun and allow it to reach the desired temperature. Most heat guns have adjustable settings, so make sure it’s set to a high enough heat to cure plastisol ink.
- Test the Temperature: Before applying heat to your print, test the temperature with a laser thermometer to ensure it’s at least 320°F (160°C). This step is crucial to avoid under-curing or damaging the fabric.
- Even Heat Application: Hold the heat gun about 2-3 inches away from the print and move it in a steady, circular motion. This ensures even heating across the entire design. Avoid staying in one spot too long, as this can scorch the fabric or cause the ink to overheat.
- Monitor the Curing Process: Use the laser thermometer to continuously monitor the ink’s temperature. The ink should maintain the curing temperature for at least 15-30 seconds to ensure it fully cures.
- Check for Full Cure: Once cured, allow the print to cool slightly, then perform a stretch test. Gently stretch the fabric—if the print cracks or peels, it may need additional curing time.
Pros and Cons of Using a Heat Gun:
- Pros: Portable, cost-effective, and ideal for small runs or touch-ups.
- Cons: Less precise temperature control, and uneven curing is more likely if not done carefully.
Curing Via Heat Press
A heat press is another effective method for curing plastisol ink, providing consistent and even pressure and heat across the entire print. This method is especially useful for larger production runs, as it allows for uniform curing and reduces the risk of under-curing.
Steps to Cure Plastisol Ink with a Heat Press:
- Set the Heat Press Temperature: Preheat the heat press to 320°F (160°C), the standard curing temperature for plastisol ink. Ensure the heat press is calibrated accurately to avoid under or over-curing.
- Position the Garment: Place the garment on the heat press with the printed side facing up. If the design is particularly large, you may need to cure it in sections.
- Apply Pressure: Lower the heat press onto the garment, applying even pressure across the entire design. The amount of pressure required will depend on the fabric type and the complexity of the design, but a medium pressure setting is typically sufficient.
- Curing Time: Keep the heat press closed for about 15-30 seconds. This duration allows the ink to reach the full curing temperature and ensures the design is fully bonded to the fabric.
- Release and Cool: After curing, lift the heat press and allow the garment to cool before handling. This cooling period helps the ink set and reduces the risk of smudging or distortion.
Pros and Cons of Using a Heat Press:
- Pros: Provides consistent, even curing and is ideal for high-volume production.
- Cons: Less flexibility for curing complex or uneven designs, and the initial cost of a heat press can be higher than other methods.
Curing Via Conveyor Dryer
For screen printing businesses that produce high volumes of printed garments, a conveyor dryer is the most efficient and reliable method for curing plastisol ink. Conveyor dryers use a continuous belt that moves the garments through a heated chamber, ensuring even and consistent curing.
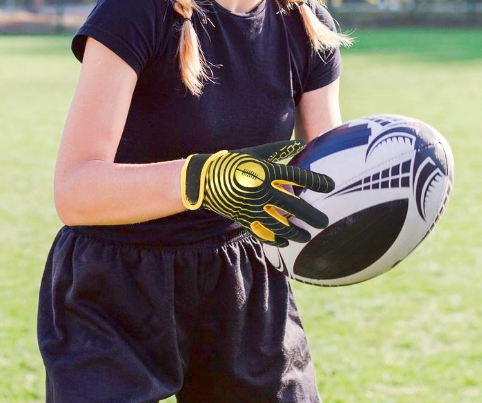
Steps to Cure Plastisol Ink with a Conveyor Dryer:
- Set the Dryer Temperature: Adjust the conveyor dryer to the correct curing temperature, typically around 320°F (160°C). Make sure the temperature is uniform throughout the dryer’s chamber.
- Adjust the Belt Speed: Set the conveyor belt speed to allow the garments to pass through the heated chamber for the necessary amount of time. The exact speed will depend on the thickness of the ink and the type of garment being printed.
- Place the Garments: Load the garments onto the conveyor belt, ensuring they are laid flat with no folds or wrinkles. This positioning helps avoid uneven curing.
- Monitor the Process: As the garments pass through the dryer, monitor the temperature to ensure it remains consistent. Some conveyor dryers have built-in temperature controls and alarms to help with this.
- Perform Quality Checks: After curing, check the garments for any signs of under-curing or over-curing. Perform a stretch test or wash test to confirm that the ink has fully cured.
Pros and Cons of Using a Conveyor Dryer:
- Pros: Best for large-scale production, provides consistent results, and can handle high volumes efficiently.
- Cons: High initial cost, requires more space, and may be unnecessary for smaller operations.
Conclusion
Curing plastisol ink properly is crucial to ensuring that your prints are durable, vibrant, and long-lasting. Whether you choose to use a heat gun, heat press, or conveyor dryer, understanding the principles of curing and the importance of achieving a full cure will help you produce high-quality screen prints every time. Each method has its advantages, and the right one for you will depend on your production needs and the scale of your operation. By following the steps outlined above, you can ensure that your plastisol ink prints are fully cured and ready to withstand the test of time.