Ink plastisol is widely used in screen printing. Discover the 5 essential advantages and disadvantages of using plastisol ink.
What are the disadvantages of plastisol?
Ink plastisol is a popular choice in screen printing due to its durability and vibrant colors. However, it does have a few disadvantages. One of the primary concerns is its environmental impact. Plastisol ink contains PVC (polyvinyl chloride) and often phthalates, which are harmful to both human health and the environment. Despite the availability of phthalate-free variants, plastisol remains non-biodegradable, contributing to plastic waste.
Additionally, plastisol requires high curing temperatures of around 320°F (160°C) to fully set, making it less energy-efficient compared to water-based inks. This can lead to higher energy costs, particularly in large-scale printing operations. Moreover, the final result of plastisol printing tends to feel less breathable, which can make garments feel stiffer or heavier than those printed with water-based inks.
Is plastisol better than water-based ink?
The debate between ink plastisol and water-based ink often depends on the needs of the project. Plastisol inks are known for their opacity and vibrant colors, which makes them ideal for printing on dark fabrics and intricate designs. Plastisol also provides a thick, raised texture on the fabric, which enhances its durability, making it resistant to fading over time. For high-contrast designs or larger print runs, plastisol is often preferred.
On the other hand, water-based inks offer several benefits in terms of eco-friendliness. They don’t contain PVC or phthalates, which makes them more environmentally friendly. Water-based inks are absorbed by the fabric, resulting in a softer finish. This makes them ideal for designs requiring a more natural, breathable feel, such as lighter garments or vintage-style prints.
In the end, the choice between plastisol and water-based inks depends on the specific requirements of the print job. However, if you prioritize an eco-friendly approach and a softer finish, water-based inks are a worthy alternative.
What are the disadvantages of water-based ink?
While water-based inks are considered more eco-friendly, they do have a few drawbacks. One of the main disadvantages is that they are less opaque compared to plastisol, especially when printing on dark fabrics. To achieve a similar opacity, multiple layers of water-based ink may be required, which can increase production time.
Water-based inks also need precise curing, as over-curing can cause cracking, while under-curing can result in incomplete drying, leading to smudging. Additionally, water-based inks are more sensitive to humidity, which can affect the printing process and the final quality of the design. This requires a controlled environment to achieve consistent results.
Moreover, water-based inks have a shorter shelf life than plastisol, and they can dry out in the screen if not used promptly. This adds to the complexity of using water-based inks, especially in high-volume printing setups where efficiency is key.
What is plastisol ink used for?
Ink plastisol is commonly used for screen printing on apparel such as t-shirts, hoodies, and sportswear. Its ability to produce bright, opaque prints makes it ideal for designs with bold colors or intricate details. Plastisol is particularly favored for printing on dark-colored fabrics, where its opacity ensures that the design stands out.
In addition to clothing, plastisol ink can also be used for printing on other materials like textiles, posters, and certain plastics. The durability of plastisol prints makes them well-suited for items that need to withstand frequent washing, such as promotional merchandise, team apparel, and workwear. Specialty prints, like puff, glitter, and high-density designs, are also made possible with plastisol ink.
Since plastisol sits on top of the fabric rather than being absorbed, it offers excellent color retention and resistance to fading, making it a go-to choice for designs that need to last.
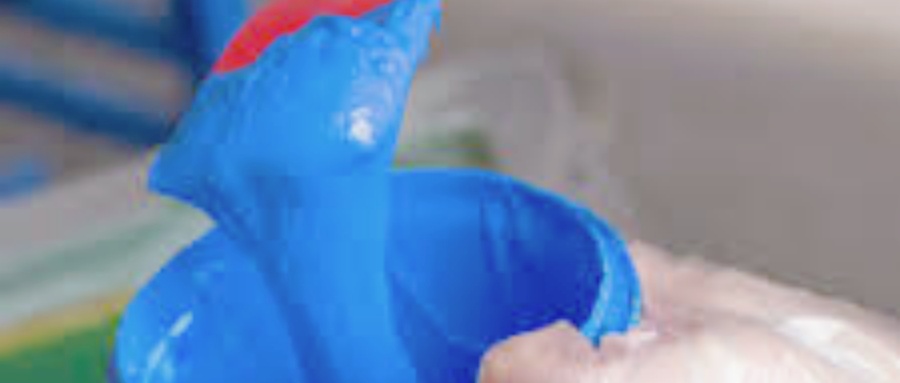
What ink is best for screen printing?
If your goal is a softer, more eco-friendly finish, then water-based inks might be the better option. Water-based inks penetrate the fabric, providing a smoother, softer feel and a more natural appearance. They are also better suited for lighter fabrics and designs that require a more subtle look.
Ultimately, both ink types have their strengths. If longevity and opacity are your priorities, ink plastisol is the way to go. For a greener option with a lighter feel, water-based inks may be the better fit.
How many washes does plastisol ink last?
One of the key advantages of ink plastisol is its durability. When properly cured, plastisol ink can last for 50 to 100 washes without significant fading or cracking. This makes plastisol a great choice for garments that will undergo heavy use, such as team shirts, promotional items, or work uniforms.
To ensure that plastisol prints last as long as possible, proper washing and care are essential. It’s recommended to wash garments printed with plastisol ink inside out in cold water and avoid using harsh detergents or drying them on high heat. This will help preserve the quality of the print and extend its lifespan.
Conclusion
Ink plastisol is a durable and versatile ink choice for screen printing, particularly when you need bold, long-lasting prints. While it has some environmental and comfort drawbacks, its ability to withstand multiple washes and produce vibrant, opaque designs makes it a popular choice for many screen printers. When deciding between ink plastisol and water-based ink, it ultimately comes down to your specific needs, whether that’s environmental impact, softness, or durability. Understanding the advantages and disadvantages of both inks will help you make the best decision for your screen printing projects.
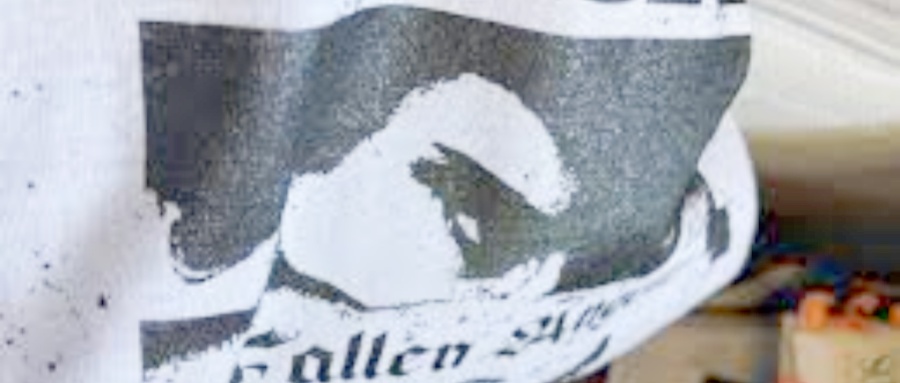